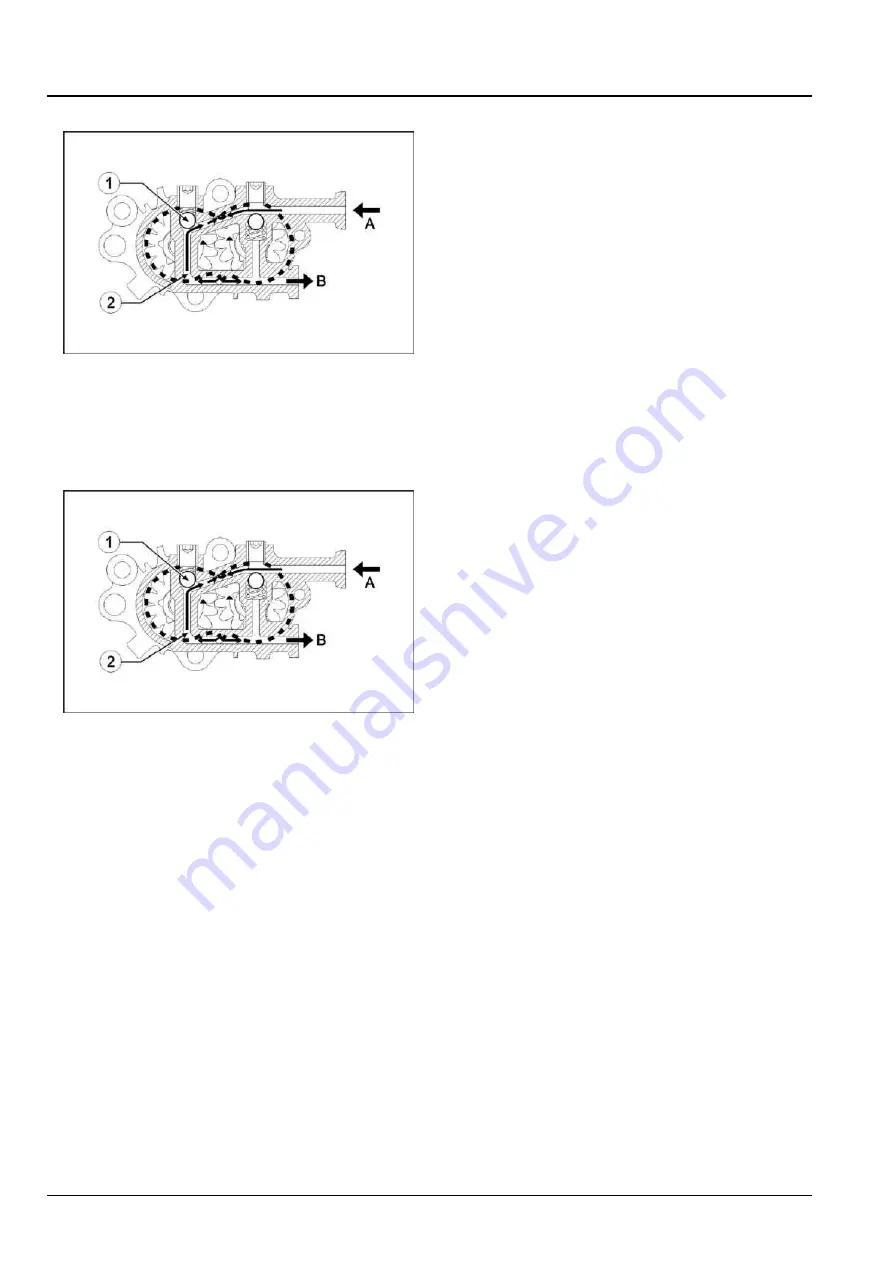
Engine - Engine and crankcase
Pressure control mode
RAIL15TR00370AA
34
When the fuel Pressure exceeds
5.0 bar
(
72.5 psi
), the
supply pump relief valve open opens and fuel is routed
to the inlet side of the pump.
(A) Supply fuel drawn from pre-filter
(B) Supply fuel to final filter
(1) Fuel supply relief valve
5.0 bar
(
72.5 psi
)
(2) Supply pump bypass valve (for bleeding)
Bypass mode
RAIL15TR00370AA
35
During lift pump operation, fuel will bypass the gear
pump through a check valve that opens at about
0.138
- 0.345 bar
(
2.0 - 5.0 psi
).
(A) Supply fuel drawn from pre-filter
(B) Supply fuel to final filter
(1) Fuel supply relief valve
5.0 bar
(
72.5 psi
)
(2) Supply pump bypass valve (for bleeding)
47917988 24/09/2015
10.1 [10.001] / 24