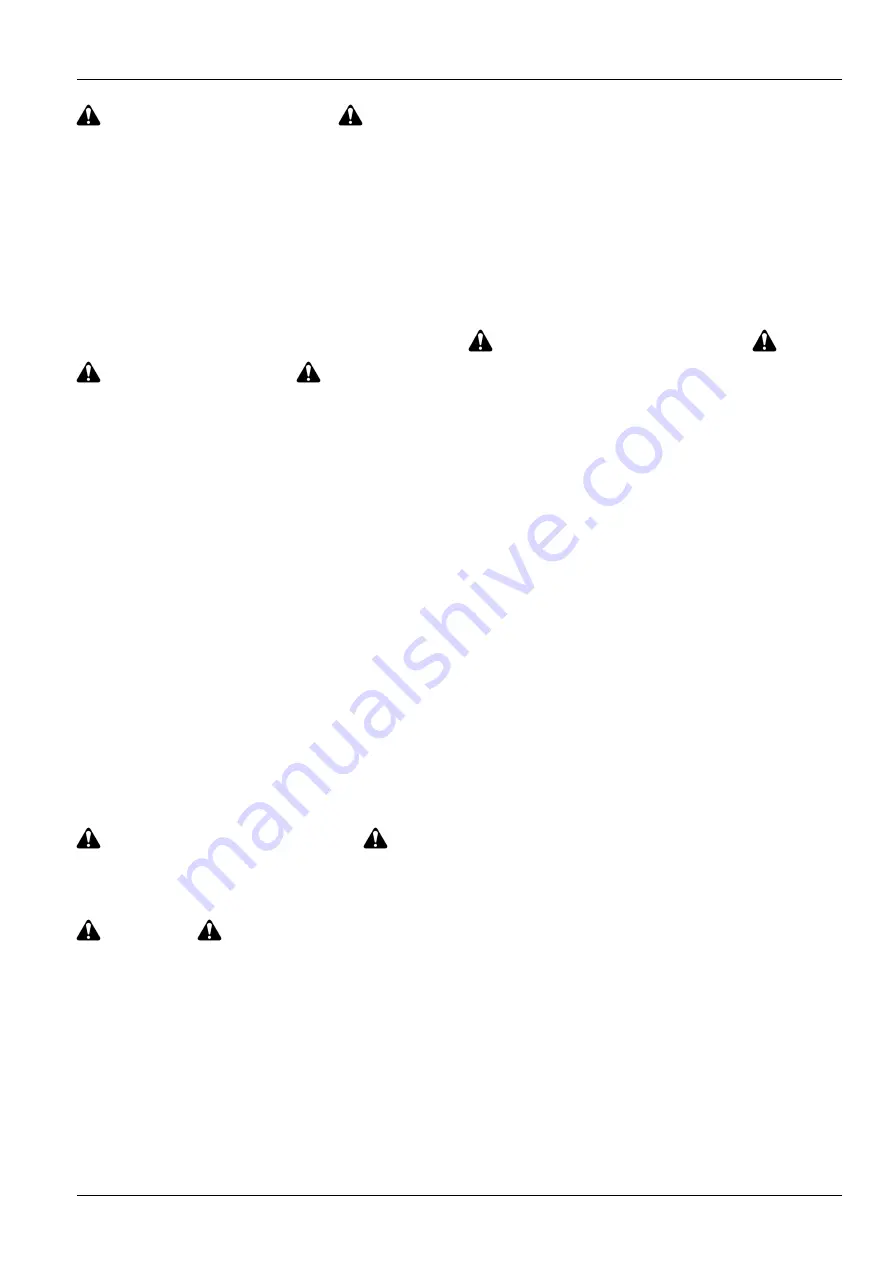
2 - SAFETY INFORMATION
Operator presence system
Your machine is equipped with an operator presence sys-
tem to prevent the use of some features while the operator
is not in the operator’s seat.
Never disconnect or bypass the operator presence sys-
tem.
If the operator presence system is inoperable, then it must
be repaired.
See page
6-5
for more information on how the operator
presence system functions on your tractor.
Power Take-Off (PTO)
PTO-driven machinery can cause death or serious injury.
Before you work on or near the PTO shaft or service or
clear the driven machine, put the PTO lever in the disen-
gage position, stop the engine, and remove the key.
Whenever a PTO is in operation, a guard must be in place
to prevent death or injury to the operator or bystanders.
When doing stationary PTO work, keep clear of all moving
parts and make sure that appropriate guards are in place.
Never use a spline adaptor:
• Match the right tractor PTO spline and speed with the
PTO driveshaft provided with an implement. This will
assure proper geometry and operating speed.
• Never operate
540 RPM
implements at
1000 RPM
.
• Never operate
1000 RPM
implements at
540 RPM
.
• Use of PTO adaptors will void the warranty of the drive-
shaft, and the PTO drive train of the machine and im-
plement.
• For correct hitch geometry, refer to the operator’s man-
ual for each implement you connect.
Reflectors and warning lights
You must use flashing amber warning lights when you
operate equipment on public roads.
Seat belts
Seat belts must be worn at all times.
Seat belt inspection and maintenance:
• Keep seat belts in good condition.
• Keep sharp edges and items than can cause damage
away from the belts.
• Periodically check belts, buckles, retractors, tethers,
slack take-up system, and mounting bolts for damage
and wear.
• Replace all parts that have damage or wear.
• Replace belts that have cuts that can make the belt
weak.
• Check that bolts are tight on the seat bracket or mount-
ing.
• If the belt is attached to the seat, make sure that the
seat or seat brackets are mounted securely.
• Keep seat belts clean and dry.
• Clean belts only with soap solution and warm water.
• Do not use bleach or dye on the belts because this can
make the belts weak.
Operator protective structure
Your machine is equipped with an operator protective
structure, such as:
a Roll Over Protective Structure
(ROPS), Falling Objects Protective Structure (FOPS),
or a cab with a ROPS. A ROPS may be a can frame
or a two-posted or four-posted structure used for the
protection of the operator to minimize the possibility of
serious injury.
The mounting structure and fasteners
forming the mounting connection with the machine are
part of the ROPS.
The protective structure is a special safety component of
your machine.
DO NOT attach any device to the protective structure for
pulling purposes. DO NOT drill holes to the protective
structure.
The protective structure and interconnecting components
are a certified system. Any damage, fire, corrosion, or
modification will weaken the structure and reduce your
protection. If this occurs, THE PROTECTIVE STRUC-
TURE MUST BE REPLACED so that it will provide the
same protection as a new protective structure. Contact
your dealer for protective structure inspection and re-
placement.
After an accident, fire, tip over, or roll over, the following
MUST be performed by a qualified technician before
returning the machine to field or job-site operations:
• The protective structure MUST BE REPLACED.
• The mounting or suspension for the protective struc-
ture, operator’s seat and suspension, seat belts and
mounting components, and wiring within the operator’s
protective system MUST be carefully inspected for
damage.
• All damaged parts MUST BE REPLACED.
DO
NOT
WELD,
DRILL
HOLES,
ATTEMPT
TO
STRAIGHTEN, OR REPAIR THE PROTECTIVE STRUC-
TURE. MODIFICATION IN ANY WAY CAN REDUCE
THE STRUCTURAL INTEGRITY OF THE STRUCTURE,
WHICH COULD CAUSE DEATH OR SERIOUS INJURY
IN THE EVENT OF FIRE, TIP OVER, ROLL OVER,
COLLISION, OR ACCIDENT.
2-5
Summary of Contents for Workmaster 25 Tier 4B
Page 74: ...3 CONTROLS AND INSTRUMENTS 3 28 ...
Page 110: ...5 TRANSPORT OPERATIONS 5 8 ...
Page 116: ...6 WORKING OPERATIONS 6 6 ...
Page 178: ...8 TROUBLESHOOTING 8 6 ...
Page 187: ...9 SPECIFICATIONS NHIL12CT00862HA 1 9 9 ...
Page 188: ...9 SPECIFICATIONS 9 10 ...
Page 190: ...10 ACCESSORIES 10 2 ...