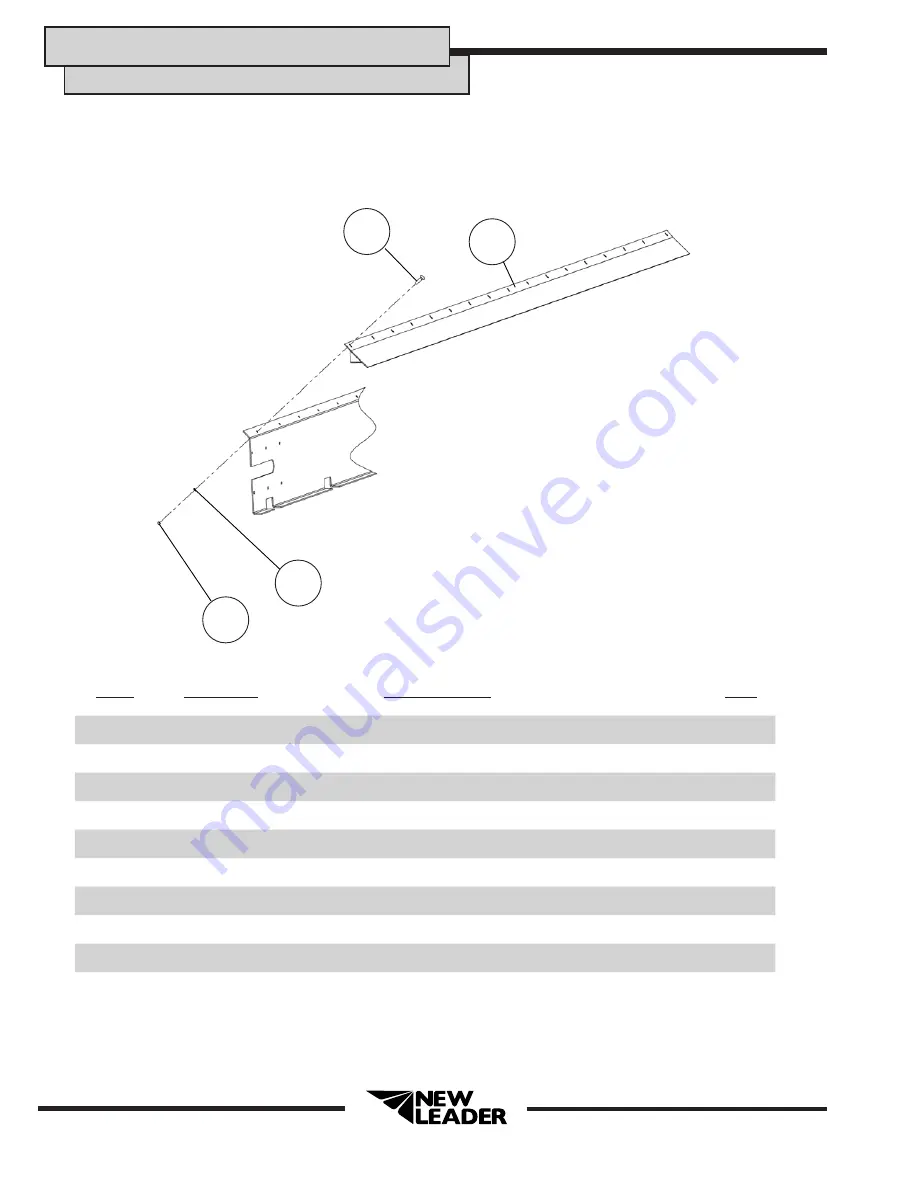
- 124 -
www.NewLeader.com
(800) 363-1771
305438-J
L5034G4
1
2
3
4
2
3
4
1
ITEM
PART NO�
DESCRIPTION
QTY
1
Chain Shield – Chain
305450-AB
13’ Unit
2
305450-AC
14’ Unit
2
305450-AD
16’ Unit
2
305450-AE
18’ Unit
2
305450-AF
21’ Unit
2
2
71829
Bolt – Carriage 3/8 x 1
AR
3
36420
Washer – Lock 3/8
AR
4
36414
Nut – Hex 3/8
AR
AR – As Required
Chain Shields
Conveyor
Summary of Contents for L5034 G4
Page 6: ...Insert Current New Leader Warranty Warranty...
Page 7: ...SAFETY...
Page 26: ...INSTALLATION...
Page 35: ...33 This page is intentionally left blank L5034G4 www NewLeader com 800 363 1771 305438 J Notes...
Page 36: ...34 This page is intentionally left blank www NewLeader com 800 363 1771 305438 J L5034G4 Notes...
Page 37: ...OPERATIONS MAINTENANCE...
Page 50: ...47 L5034G4 www NewLeader com 800 363 1771 305438 J Troubleshooting Hydraulic Schematic...
Page 54: ...CONTROLLER...
Page 91: ...SPREAD PATTERN...
Page 102: ...PARTS...
Page 114: ...108 www NewLeader com 800 363 1771 305438 J L5034G4 Main Bin Body Hydraulics...
Page 115: ...109 L5034G4 www NewLeader com 800 363 1771 305438 J Main Bin Cont Body Hydraulics...