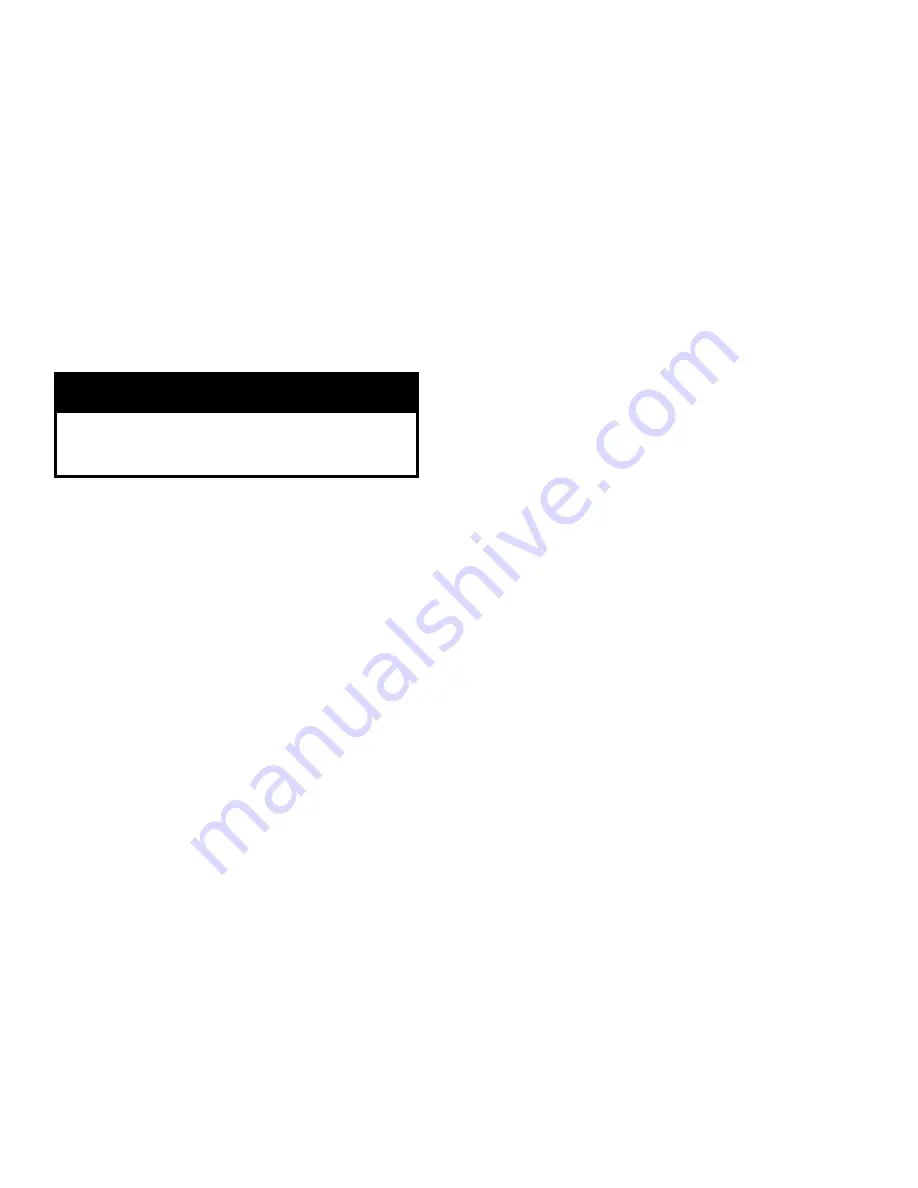
22
R.
Boil-out boiler.
1. Follow instructions TO TURN OFF GAS TO
APPLIANCE. See Figure 21 for continuous
ignition (standing pilot) or Figure 22 for intermittent
ignition (EI).
2. Drain boiler until 1" of water is visible in gauge
glass.
3. Run temporary hose or piping from boiler drain
valve to an open drain or some other location where
hot water may be discharged safely. Do not install
valve in this line.
4. Drain about 5 gallons of hot water from boiler into a
container and dissolve into it an appropriate amount
of recommended boil out compound. Remove
safety valve and add solution to boiler water through
exposed tapping using a funnel.
E
C
I
T
O
N
l
a
c
o
l
t
l
u
s
n
o
c
r
o
s
e
i
t
i
r
o
h
t
u
a
l
a
c
o
l
h
t
i
w
k
c
e
h
C
e
l
b
a
t
p
e
c
c
a
r
o
f
s
e
c
i
v
r
e
s
t
n
e
m
t
a
e
r
t
r
e
t
a
w
.
s
d
n
u
o
p
m
o
c
g
n
i
n
a
e
l
c
l
a
c
i
m
e
h
c
5. Run temporary hose or piping from boiler tapping
"E" to an open drain or some other location where
hot water may be discharged safely. Do not install
valve in this line (See Figure 4).
6. Follow Lighting or Operating Instructions to place
boiler in operation. See Figure 21 for continuous
ignition (standing pilot) or Figure 22 for intermittent
ignition (EI).
7. Operate sufficiently to boil the water without
producing steam pressure. Boil for about 5 hours.
Open boiler fill valve sufficiently to permit a steady
trickle of water from the pipe. Continue this slow
boiling and trickle of overflow for several hours
until the water coming from the overflow is clear.
8. Follow instructions TO TURN OFF GAS TO
APPLIANCE. See Figure 21 for continuous
ignition (standing pilot) or Figure 22 for intermittent
ignition (EI).
9. Drain boiler in a manner and to a location that hot
water can be discharged with safety.
10. Refill boiler to normal water line. If water in gauge
glass does not appear to be clear, repeat steps (1
thru 3) and boil out the boiler for a longer time.
S.
Second Boilout for Stubborn Cases.
If unsteady water
line, foaming or priming persist, proceed as follows:
1. Connect hoses from boiler and return main drain
valves to floor drain. Close shut off valve in
Hartford Loop and open drain valve in return main.
Fill boiler to normal water level.
2. Follow Lighting or Operating Instructions to place
boiler in operation. See Figure 21 for continuous
ignition (standing pilot) or Figure 22 for intermittent
ignition (EI).
3. Operate boiler at this water level for at least 30
minutes after the condensate begins to run hot.
4. Follow instructions TO TURN OFF GAS TO
APPLIANCE. See Figure 21 for continuous
ignition (standing pilot) or Figure 22 for intermittent
ignition (EI).
5. Close all radiator valves. Remove all supply main
air valves and plug the openings in supply main.
6. Draw about 5 gallons of hot water from boiler into a
container and dissolve into it the appropriate amount
of a recommended boilout compound. Remove
safety valve from boiler and pour this solution into
boiler, then reinstall safety valve.
7. Follow Lighting or Operating Instructions to place
boiler in operation. See Figure 21 for continuous
ignition (standing pilot) or Figure 22 for intermittent
ignition (EI).
8. Keep operating boiler while feeding water to boiler
slowly. This will raise water level in boiler slowly
so that water will be boiling hot and will rise slowly
into supply main and back through return main,
flowing from drain hose at about 180°F. Continue
until water runs clear from drain hose for at least 30
minutes.
9. Stop feeding water to boiler but continue operating
boiler until excess water in boiler flows out through
supply main and water lowers (by steaming) until it
reaches normal level in boiler.
10. Follow instructions to TURN OFF GAS TO
APPLIANCE. See Figure 21 for continuous
ignition (standing pilot) or Figure 22 for
intermittent ignition (EI).
11. Drain boiler. Open all radiator valves. Reinstall
all supply main air valves. Open shut off valve in
Hartford Loop.
12. When boiler has cooled down sufficiently (iron
sections are not too hot to touch), close the drain
valves at boiler and in return main and feed water
slowly up to normal level in boiler.
13. Follow Lighting or Operating Instructions to place
boiler in operation. See Figure 21 for continuous
ignition (standing pilot) or Figure 22 for
intermittent ignition (EI).
14. Allow boiler to steam for 10 minutes.
15. Follow instructions to TURN OFF GAS TO
APPLIANCE. See Figure 21 for continuous
ignition (standing pilot) or Figure 22 for
intermittent ignition (EI).
16. Draw off one quart of water from bottom gauge
glass fitting and discard. Draw off another quart
sample and if this sample is not clear, repeat the
cycle of draining the boiler and return main and
refilling the boiler until sample is clear.