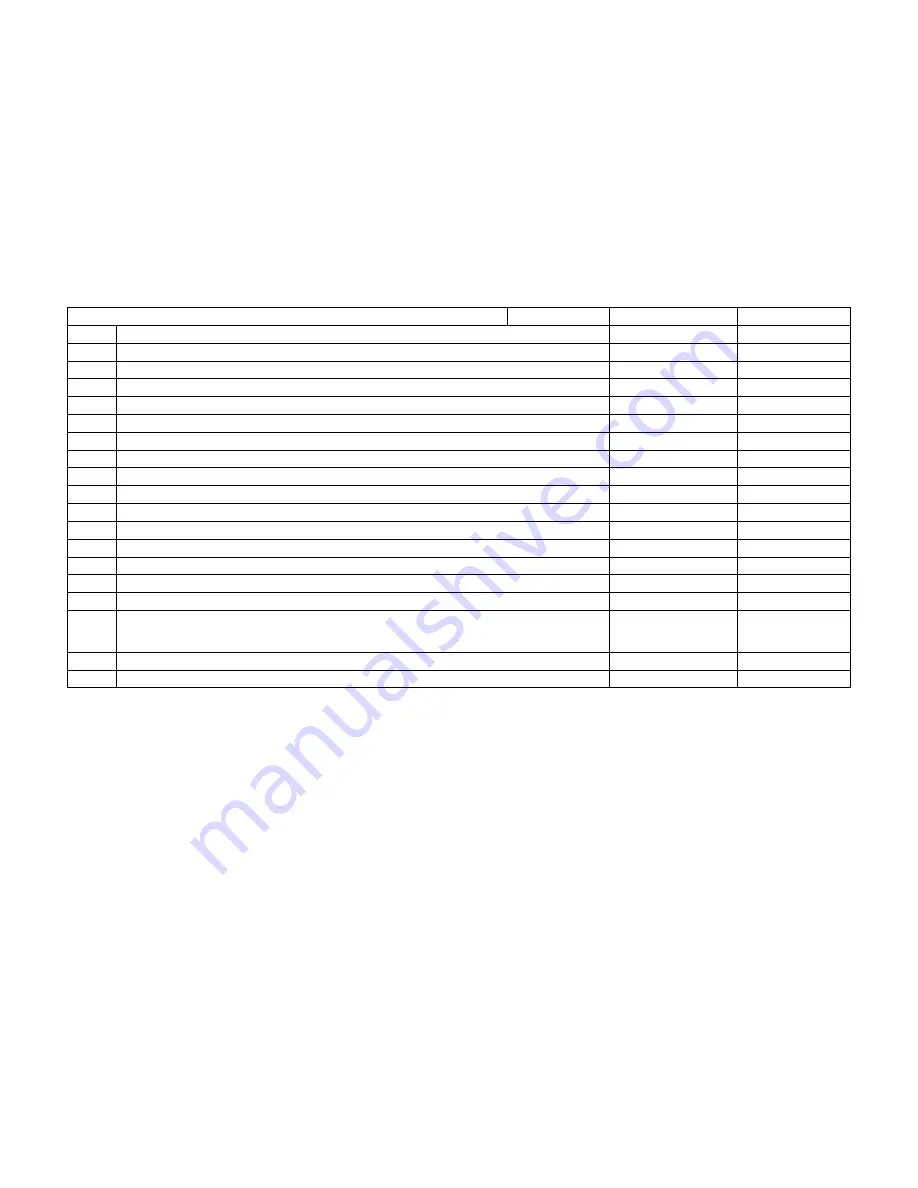
39
INSTALLER INFORMATION
NAME
:___________________________________
COMPANY
________________________________
The homeowner should telephone (____)__________________for a service call or for additional information.
APPLIANCE INITIAL TEST AND SERVICE INFORMATION
MODEL :___________________________INSTALLATION DATE :______________________________
DATE
1
FUEL INPUT (GPH)
2
FUEL PRESSURE (PSIG)
3
DRAFT @ BREECH
4
DRAFT @ OVERFIRE
5
NOZZLE ANGLE/PATTERN
6
CO
2
PERCENT
7
BURNER MODEL
8
FLUE GAS TEMP
0
F
9
ROOM TEMP
0
F
10
SMOKE DENSITY N
O
.
11
FUEL GRADE N
O
.
12
STATIC PRESSURE IN WC (BONNET)
13
AIR TEMP. INLET
0
F
14
AIR TEMP. OUTLET
0
F
15
AIR TEMP RISE
0
F
16
LIMIT CONTROLS FUNCTIONING PROPERLY
17
A
PRIMARY CONTROL
SHUT OFF TIME (FLAME FAILURE)
B
SHUT OFF TIME (IGNITION FAILURE)
18
PULLEY TURNS OPEN
Summary of Contents for CL 115-170C
Page 7: ...6 FIG 6 FLUE PIPE CONNECTION MINIMUM INSTALLATION CLEARANCES...
Page 8: ...7 FIG 7 CONTROL LOCATIONS...
Page 18: ...17 FIG 10 TYPICAL A C COIL INSTALLATION...
Page 19: ...18 FIG 11 WIRING DIAGRAM WITH AIR CONDITIONING...
Page 20: ...19 FIG 12 CL SERIES WIRING DIAGRAM...
Page 21: ...20 FIG 13 COMBINATION AIR FLOW FIG 14 AIR CONDITIONING INSTALLATION...
Page 26: ...25 FIG 16 1G THERMO DISC MOUNTING ON BURNER PLATE...