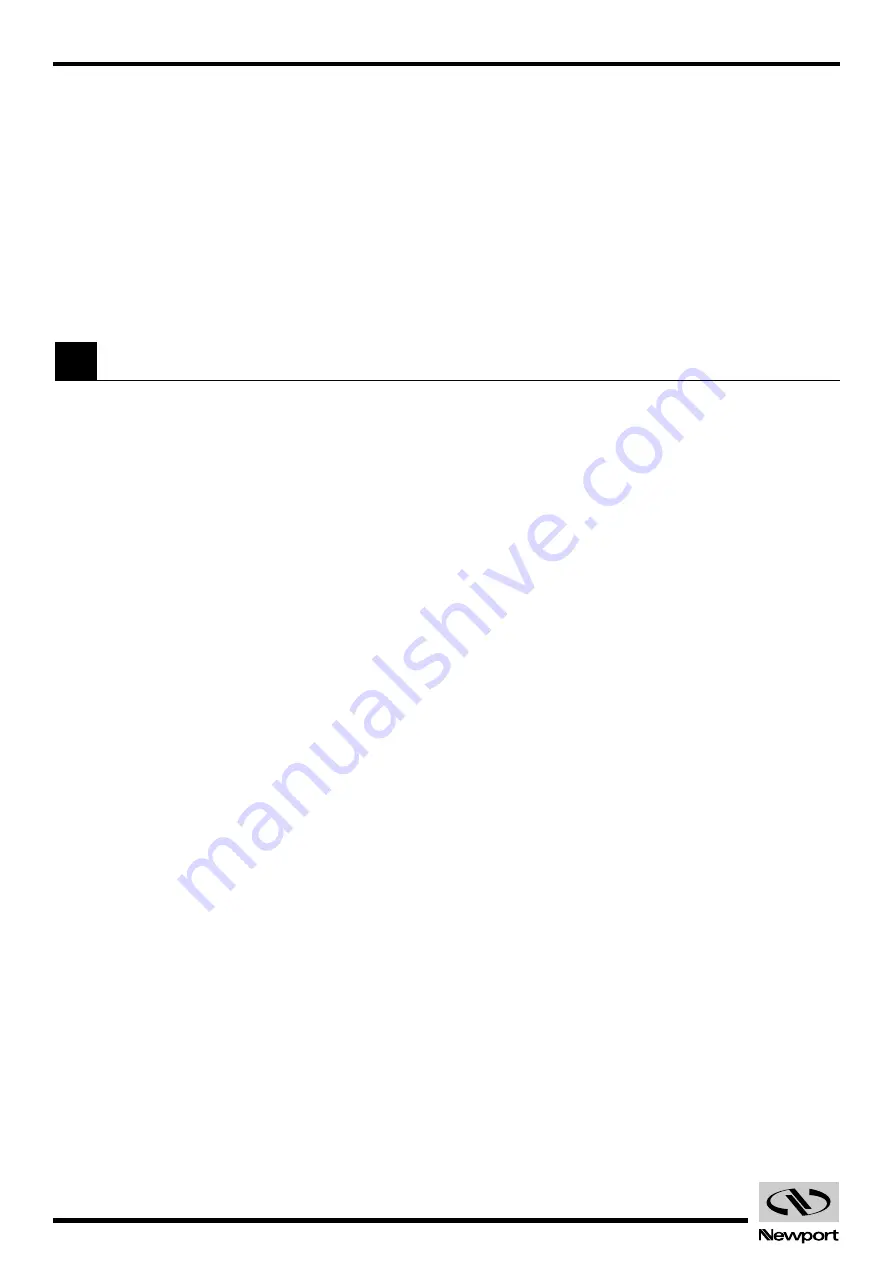
EDH0162En1040 – 06/99
4.4
MM4005
Motion Control Tutorial
If you are like most motion control users, you started by selecting a motion
device that matches certain specifications needed for an application. Next,
you chose a controller that can satisfy the motion characteristics required.
The chances are that you are less interested in how the components look
or what their individual specs are, but want to be sure that together they
perform reliably according to your needs.
We mentioned this to make a point: A component is only as good as the
system lets (or helps) it to be.
For this reason, when discussing a particular system performance specifi-
cation, we will also mention which components affect performance the
most and, if appropriate, which components improve it.
Specification Definitions
People mean different things when referring to the same parameter name.
To establish some common ground for motion control terminology, here
are some general guidelines for the interpretation of motion control terms
and specifications.
• As mentioned earlier, most motion control performance specifications
should be considered system specifications.
• When not otherwise specified, all error-related specifications refer to
the position error.
• The servo loop feedback is position-based. All other velocity, accelera-
tion, error, etc. parameters are derived from the position feedback and
the internal clock.
• To measure the absolute position, we need a reference, a measuring
device, that is significantly more accurate than the device tested. In our
case, dealing with fractions of microns (0.1 µm and less), even a stan-
dard laser interferometer becomes unsatisfactory. For this reason, all
factory measurements are made using a number of high precision inter-
ferometers, most of them connected to a computerizes test station.
• To avoid unnecessary confusion and to more easily understand and
troubleshoot a problem, special attention must be paid to avoid
bundling discrete errors in one general term. Depending on the applica-
tion, some discrete errors are not significant. Grouping them in one gen-
eral parameter will only complicate the understanding of the system
performance in certain applications.
4.2.1
Following Error
The Following Error is not a specifications parameter but, because it is at
the heart of the servo algorithm calculations and of other parameter defini-
tions, it deserves our attention.
As will be described later in the Control Loops paragraph, a major part of
the servo controller’s task is to make sure that the actual motion device fol-
lows as close as possible an ideal trajectory in time. You can imagine hav-
ing an imaginary (ideal) motion device that executes exactly the motion
profile you are requesting. In reality, the real motion device will find itself
deviating from this ideal trajectory. Since most of the time the real motion
device is trailing the ideal one, the instantaneous error is called Following
Error.
To summarize, the Following Error is the instantaneous difference between
the actual position as reported by the position feedback device and the
ideal position, as seen by the controller. A negative following error means
that the load is trailing the ideal motion device.
4.2
Artisan Technology Group - Quality Instrumentation ... Guaranteed | (888) 88-SOURCE | www.artisantg.com