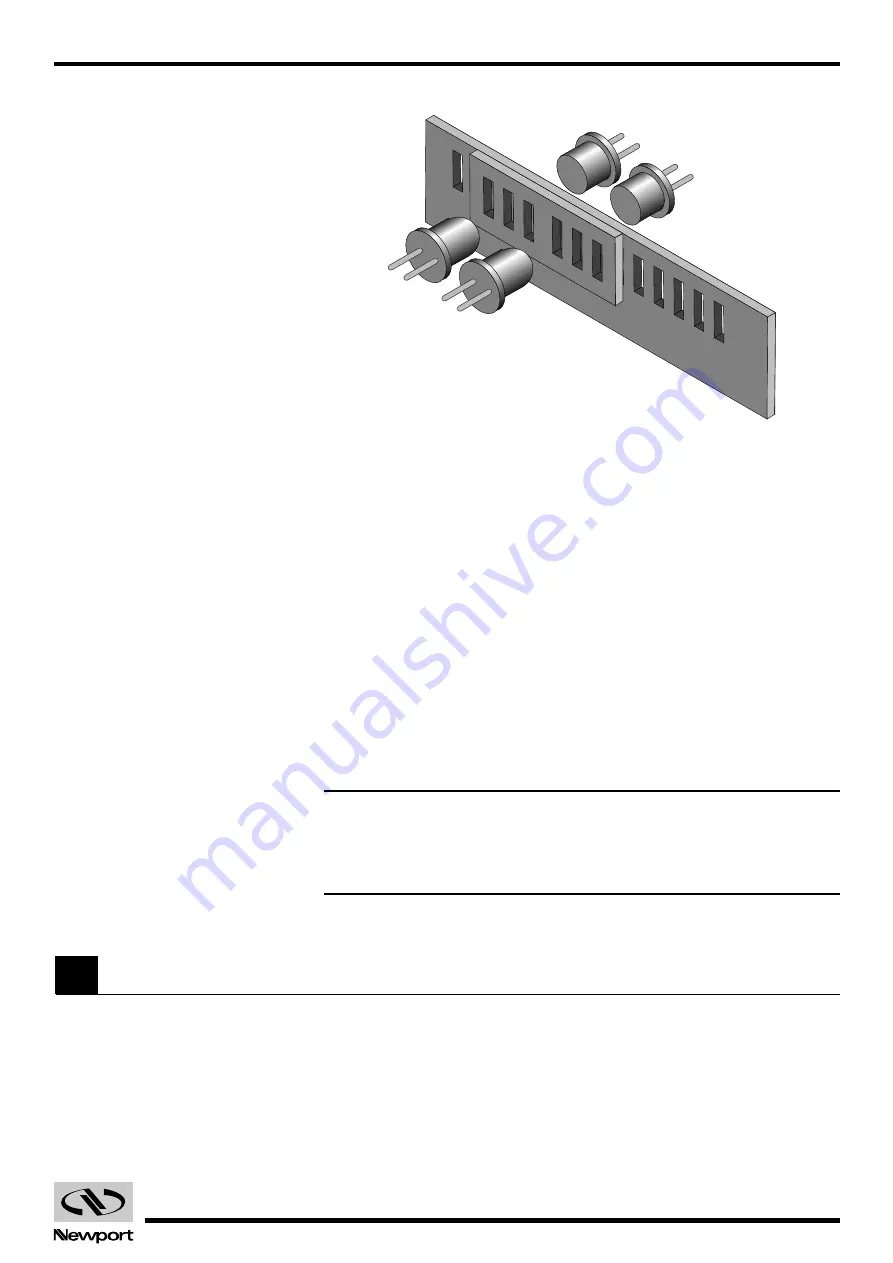
4.23
EDH0162En1040 – 06/99
MM4005
Motion Control Tutorial
Fig. 4.30
— Two-Channel Optical Encoder Scale and Read Head Assembly.
There are two basic types of encoders, linear and rotary. The linear
encoders, also called linear scales, are used to measure linear motion
directly. This means that the physical resolution of the scale will be the
actual positioning resolution. This is their main drawback since technologi-
cal limitations prevent them from having better resolutions than a few
microns. To get higher resolutions in linear scales, a special delicate cir-
cuitry must be added, called scale interpolator. Other technologies like
interferometry or holography can be used but they are significantly more
expensive and need more space.
The most popular encoders are rotary. Using gear reduction between the
encoder and the load, significant resolution increases can be obtained at
low cost. But the price paid for this added resolution is higher backlash.
In some cases, rotary encoders offer high resolution without the backlash
penalty. For instance, a linear translation stage with a rotary encoder on
the lead screw can easily achieve 1 µm resolution with negligible backlash.
NOTE
For rotary stages, a rotary encoder measures the output angle directly. In
this case, the encoder placed on the rotating platform has the same
advantages and disadvantages of the linear scales.
Motors
There are many different types of electrical motors, each one being best
suitable for certain kind of applications. The MM4005 supports two of the
most popular types: stepper motors and DC motors.
Another way to characterize motors is by the type of motion they provide.
The most common ones are rotary but in some applications, linear motors
are preferred. Though the MM4005 can drive both stepper and DC linear
motors, the standard motion device family supports only rotary motors.
4.6
Artisan Technology Group - Quality Instrumentation ... Guaranteed | (888) 88-SOURCE | www.artisantg.com