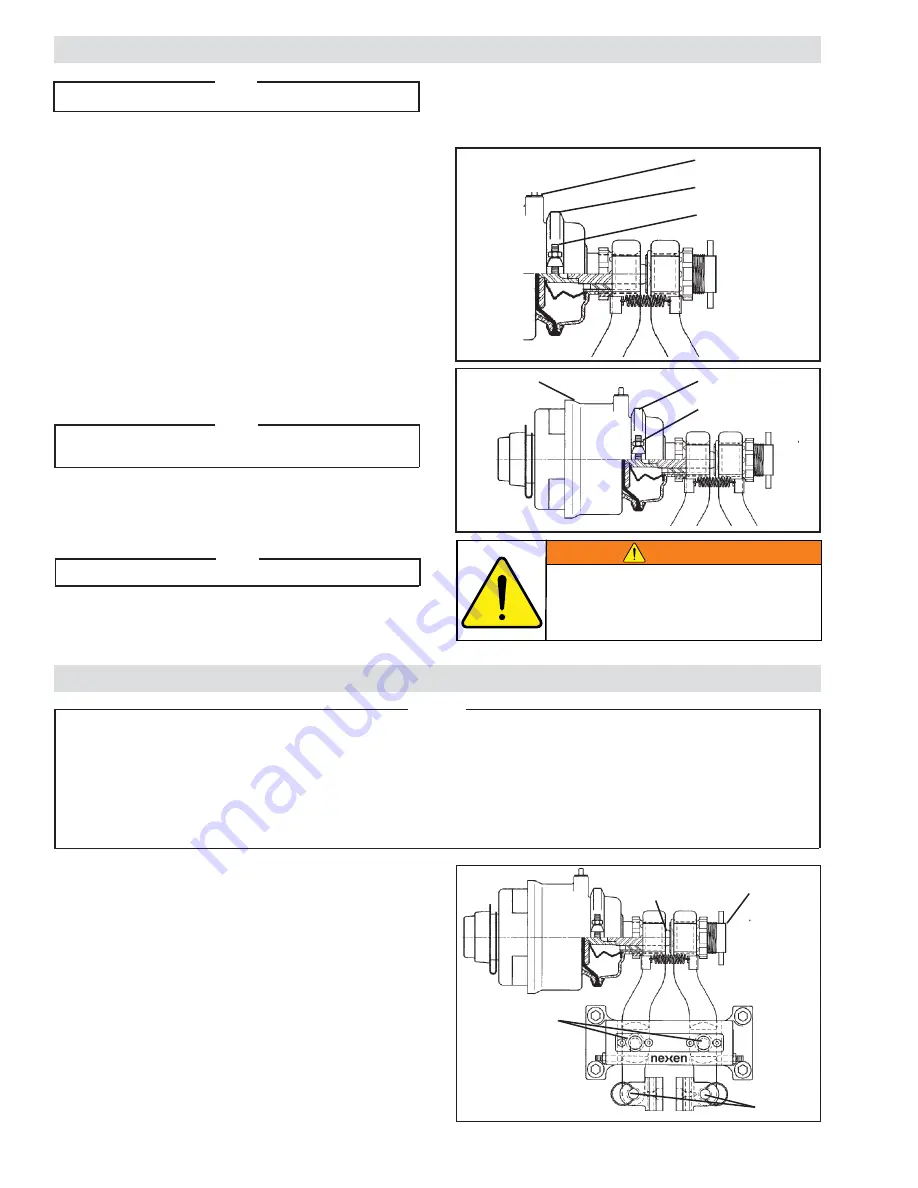
10
FORM NO. L-20063-AG-1216
Figure 7
Actuator
Ring Clamp Bolt
Ring Clamp
Figure 8
Actuator
Ring Clamp
Ring Clamp Bolt
NOTE
Maximum operating pressure is 6.90 bar [100 psi].
Pneumatically actuated devices require clean, pressure
regulated, and lubricated air for maximum performance and
long life. Your Nexen Distributor carries filters, regulators,
and lubricators specifically designed to operate with Nexen
clutches, brakes, and valves.
Piping diagrams are included in this manual for a variety
of braking functions. Refer to OPERATIONAL MODES
(See Page 12-14).
The actuator air connections may be rotated 360
o
by
loosening the Ring Clamp and rotating the Actuator Head.
If the actuator is spring engaged, first deactuate the brake
and cage the spring.
1. Apply hold-off air pressure to release the spring Actuator
(See Figure 6).
Note
Before performing step two, determine the actuator type
and select either step 2a or 2b.
2.
Manual Disengagement:
Refer to pages 16 & 17 for
manual disengagement and re-engagement instructions.
3. Adjust the ring clamp as required.
Note
Tighten Ring Clamp Bolts to 25-35 ft-lbs [34-47 Nm] torque.
AIR CONNECTIONS–GENERAL
A Hose Assembly (Item 23) is supplied and must be
connected to the brake with sufficient slack to allow the
Arms (Item 2) full movement without putting stress on the
hose or hose couplings.
Do not use rigid pipe or tubing when connecting
directly to the brake. Care must also be taken
to prevent an unshielded air hose from rubbing
on metal surfaces or edges; this will cause rapid
deterioration of the hose.
WARNING
LUBRICATION
FIGURE 9
Piston Rod
(Item 10)
Bearing
(Item 15)
Bearing
(Item 14)
Adjustment
Screw
(Item 8)
All pivot points on the BD Caliper Brake use self-lubricated
high PV bearings.
For tension control applications where the disc is held at
elevated temperatures for extended periods, use a light
machine oil on Bearings (Items 14 and 15) (See Figure 9).
The sliding spherical contact between the Adjustment Screw
(Item 8) and Piston Rod (Item 10) should be lubricated
with a molybdenum disulfide based grease (See Figure 9).
NOTE
Nexen pneumatically actuated devices require clean, pressure regulated air for maximum performance and life.
All seals in Nexen pneumatically operated devices are lubricated for life, and do not require additional lubrication.
However, some customers prefer to use an air line lubricator, which injects oil into the pressurized air, forcing
an oil mist into the air chamber. This is acceptable, but care must be taken to ensure once an air mist lubrica-
tion system is used, it is continually used over the life of the product as the oil mist may wash free the factory
installed lubrication.
Locate the lubricator above and within ten feet of the product, and use low viscosity oil such as SAE-10.
Synthetic lubricants are not recommended.