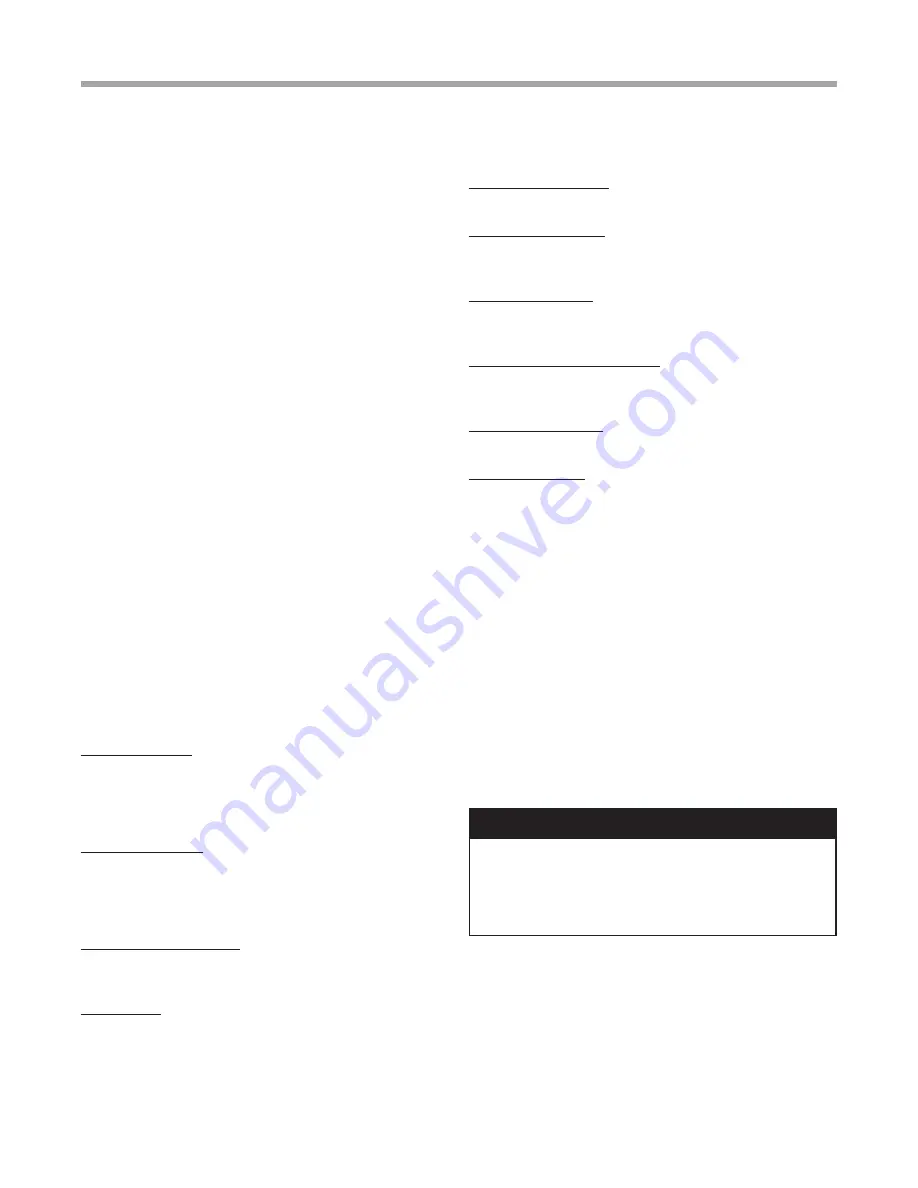
61
c l i m a t e m a s t e r.c o m
Tranquility
®
22 Digital (TZ
)
Series - 60Hz
R e v. : N o v e m b e r 1 8 , 2 0 2 2
Troubleshooting, Cont’d.
⚠
WARNING!
⚠
OUTPUTS
The compressor and reversing valve relays are 24VAC
and can be verified using a voltmeter. For units with ECM
blower motors, the DXM2.5 controls the motor using serial
communications, and troubleshooting should be done with
a communicating thermostat or diagnostic tool. The alarm
relay can either be 24VAC as shipped or dry contacts for use
with DDC controls by clipping the JW1 jumper. Electric heat
outputs are 24VDC “ground sinking” and require a voltmeter
set for DC to verify operation. The terminal marked “24VDC”
is the 24VDC supply to the electric heat board; terminal
“EH1” is stage 1 electric heat; terminal “EH2” is stage 2
electric heat. When electric heat is energized (thermostat
is sending a “W” input to the DXM2.5 controller), there will
be 24VDC between terminal “24VDC” and “EH1” (stage 1
electric heat) and/or “EH2” (stage 2 electric heat). A reading
of 0VDC between “24VDC” and “EH1” or “EH2” will indicate
that the DXM2.5 board is NOT sending an output signal to
the electric heat board.
TEST MODE
Test mode can be entered for 20 minutes by pressing the
Test push button. The DXM2.5 board will automatically exit
test mode after 20 minutes.
ADVANCED DIAGNOSTICS
To properly troubleshoot advanced control features, and to
aid in troubleshooting basic control features, a
communicating thermostat or diagnostic tool must be used.
SERVICE MODE
The Service Mode provides the installer with several
functions for troubleshooting, including Manual Operation,
Control Diagnostics, Control Configuration, and Fault History.
Manual Operation –
The Manual Operation mode allows the
installer to bypass normal thermostat timings and operating
modes, to directly activate the thermostat inputs to the
DXM2.5, activate the DXM2.5 Test mode, and directly control
the ECM blower, internal flow center, and proportional valve.
Control Diagnostics –
The Control Diagnostics menus allow
the installer to see the current status of all DXM2.5 control
switch inputs, values of all temperature sensor inputs, control
voltage, ECM blower, internal flow center, and proportional
valve operating status and parameters.
DIP Switch Configuration
–
The DIP Switch Configuration
menus allow the installer to easily see the current DXM2.5
control configuration.
Fault History –
In addition to the fault code, the DXM2.5
stores the status of all control inputs and outputs when a
fault condition is detected. The fault history covering the
last five lockout conditions is stored and may be retrieved
from the DXM2.5. After a specific fault in the fault history
is selected, the operating mode and time when the fault
occurred are displayed, with options to select specific control
status values when the lockout occurred.
Fault Temp Conditions –
This option displays the DXM2.5
temperature and voltage values when the lockout occurred.
Fault Flow Conditions –
This option displays the DXM2.5
ECM blower, pump, and valve operating parameters when
the lockout occurred.
Fault I/O Conditions
–
This option displays the status of the
DXM2.5 physical and communicated inputs and the relay
outputs when the lockout occurred.
Fault Configuration Conditions
–
This option displays the
status of the DXM2.5 option selections when the lockout
occurred.
Fault Possible Causes –
This option displays a list of
potential causes of the stored fault.
Clear Fault History –
The Clear Fault History option allows
the fault history stored in the non-volatile memory of the
DXM2.5 to be cleared.
DXM2.5 FUNCTIONAL TROUBLESHOOTING FLOW CHART
The “DXM2.5 Functional Troubleshooting Flow Chart” is
a quick overview of how to start diagnosing a suspected
problem, using the fault recognition features of the
DXM2.5 board. The “Functional Troubleshooting Chart” on
the following page is a more comprehensive method for
identifying a number of malfunctions that may occur, and is
not limited to just the DXM2.5 controls. Within the chart are
five columns:
•
The “Fault” column describes the symptoms.
• Columns 2 and 3 identify in which mode the fault is
likely to occur, heating or cooling.
•
The “Possible Cause column” identifies the most likely
sources of the problem.
•
The “Solution” column describes what should be done
to correct the problem.
WARNING!
HAZARDOUS VOLTAGE! DISCONNECT
ALL ELECTRIC POWER INCLUDING REMOTE
DISCONNECTS BEFORE SERVICING.
Failure to disconnect power before servicing can cause
severe personal injury or death.