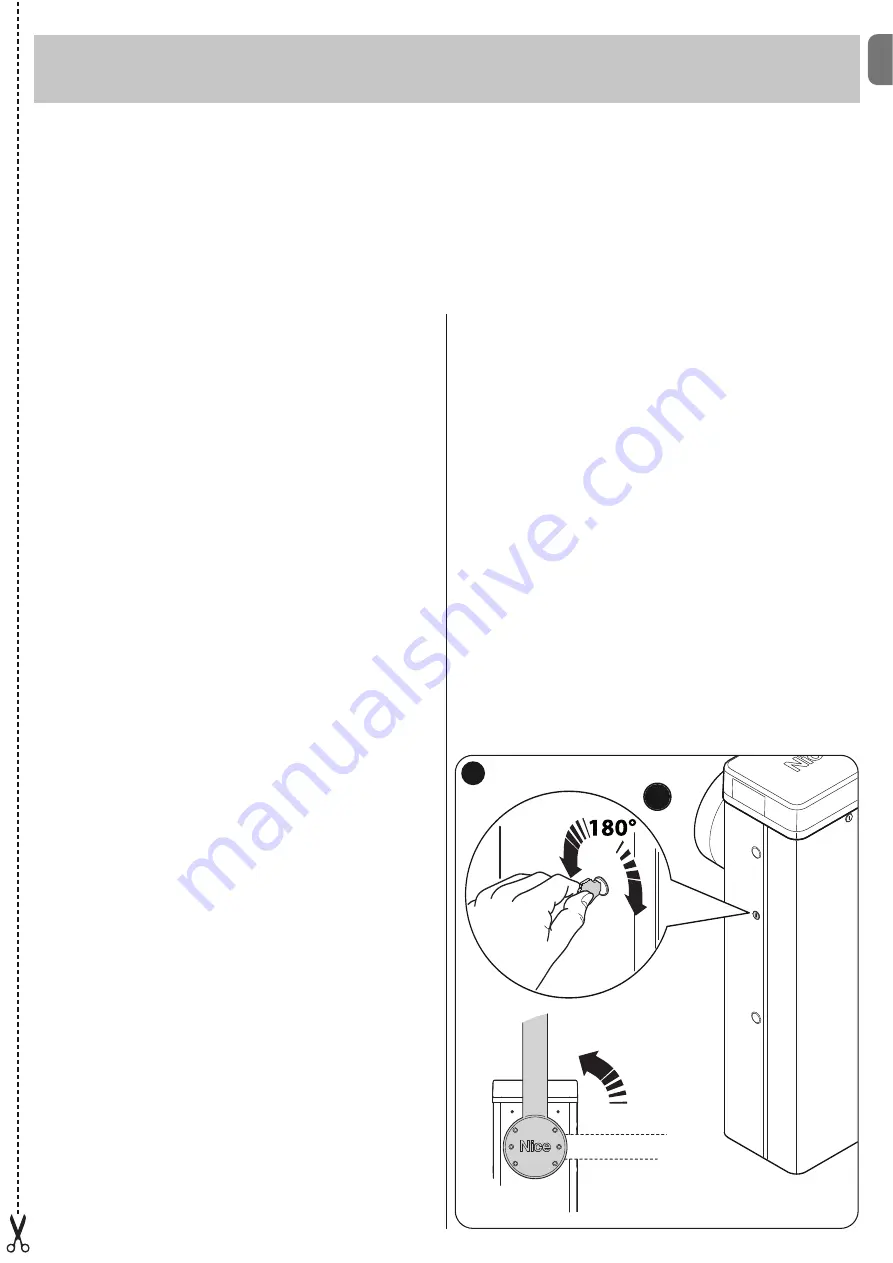
EN
English –
A
IMPORTANT! – The gearmotor release and locking operations
must be performed only when the pole is horizontal and sta-
tionary.
To manually lock and release the barrier, insert the key supplied and
turn it by 180° (
fig. A
); the key can be turned to the left or to the right.
Operation manual
(to be given to the final user of MBAR and LBAR)
Warnings
1 - Children:
An automation system guarantees a high level of safety,
using its detection systems to prevent movement in the presence of
persons or objects, and ensuring constantly foreseeable and safe acti-
vation. Nonetheless, it is advisable to ensure that children do not play
in the vicinity of the automation. This is not a toy!
2 -
This product is not designed to be used by persons (including chil-
dren) whose physical, sensorial or mental capacities are reduced, or
with lack of experience or skill, unless suitable instructions regarding
use of the product have been provided by a person responsible for
safety or under supervision of the latter.
3 - Malfunctions
: if the automation is seen to perform abnormally,
disconnect the electrical power supply from the system and manually
release the gearmotor. Never attempt to perform repairs; contact your
local installer for assistance. In the meantime the system can be used
as a manual access point, after releasing the gearmotor as described
be low in this document.
In the event of breakage or a power fail-
ure
, while waiting for the installer or the electrical power supply to
return, if the buffer battery is not fitted, the automation can still be
used. Manually release the gearmotor (see step 9 - Gearmotor manu-
al releasing and locking) and move the pole manually as required.
4 - Safety devices disabled:
the barrier can be operated even when
the safety device on the barrier does not work correctly:
- Activate the barrier command (with the transmitter or key-operated
selector switch, etc.); if all is in working order, the pole opens or
closes normally; otherwise the flashing light emits a number of flash-
es and the manoeuvre is not started (the number of flashes depends
on the reason for which the manoeuvre does not start).
- In this case, the user must press and hold the command within three
seconds.
- After approx. 2 seconds the barrier will start to operate in “hold-to-
run” mode, i.e. the pole will continue to move while the command is
activated; THE POLE STOPS AS SOON AS THE COMMAND IS
RELEASED.
If the safety devices are out of service, the automation must be
repaired as soon as possible.
5 -
Even if you possess the skills, never modify the system or pro-
gramming and setting parameters of the automation: this is the
responsibility of the installer.
6 -
Testing, periodic maintenance and any repairs must be document-
ed by the person performing the operations and the relevant docu-
ments must be kept by the system owner. The only operations that
can be performed by the user periodically are to clean the photocell
lenses and the automation. To prevent anyone from activating the bar-
rier, release the automation system before proceeding with the opera-
tions (as described below). Use a slightly damp cloth to clean.
7 - Disposal
: At the end of the automation’s lifetime, ensure that it is
disposed by qualified personnel and that the materials are recycled or
scrapped according to current local standards.
8 - Gearmotor manual release and locking
: The gearmotor is
equipped with a mechanical system that enables manual opening and
closing of the pole. These operations are required in the event of a
power failure or malfunctions.
Before using the automation for the first time, ask the installer to explain the origin of residual risks and devote a few minutes to reading this user
instruction and warning manual given to you by the installer. Keep the manual for reference when in doubt and pass it on to new owners of the
automation.
IMPORTANT! – Your automation is a machine that performs your commands faithfully; negligent or improper use may constitute
a hazard:
– Never activate automation controls if persons, animals or objects are present in the operating range.
– Never touch parts of the automation while the pole is moving!
– Transit is only permitted if the pole is completely open and stationary!
A
a
Summary of Contents for M3BAR
Page 2: ......
Page 26: ......
Page 30: ...II 4 3 b a c d g h f e c a b...
Page 31: ...III 5 6 MBAR a c d b...
Page 32: ...IV 90 8 9 MBAR a b c a b 7 a b...
Page 33: ...V 180 10 11 LBAR c a a b...
Page 34: ...VI 13 14 12 LBAR c a b...
Page 35: ...VII 15 16 18 17...
Page 36: ...VIII 19 20 21 23 22...
Page 37: ...IX 24 26 25 28 1 cm 27 29...
Page 38: ...X 33 34 30 31 32 c a b c a b...
Page 39: ...XI 35 36 37 45 38 a b a b c...
Page 41: ...XIII 42 43 44 STOP 45 46 LIGHT 47...
Page 42: ...XIV 48 49 50 a b c...
Page 43: ...XV 51 52 a b...
Page 44: ...XVI 53 a b c d e f g...
Page 46: ...XVIII F1 F1 F2 F2 55...
Page 47: ......
Page 48: ...ISTML BARR01 4865_07 10 2011 www niceforyou com Nice SpA Oderzo TV Italia info niceforyou com...