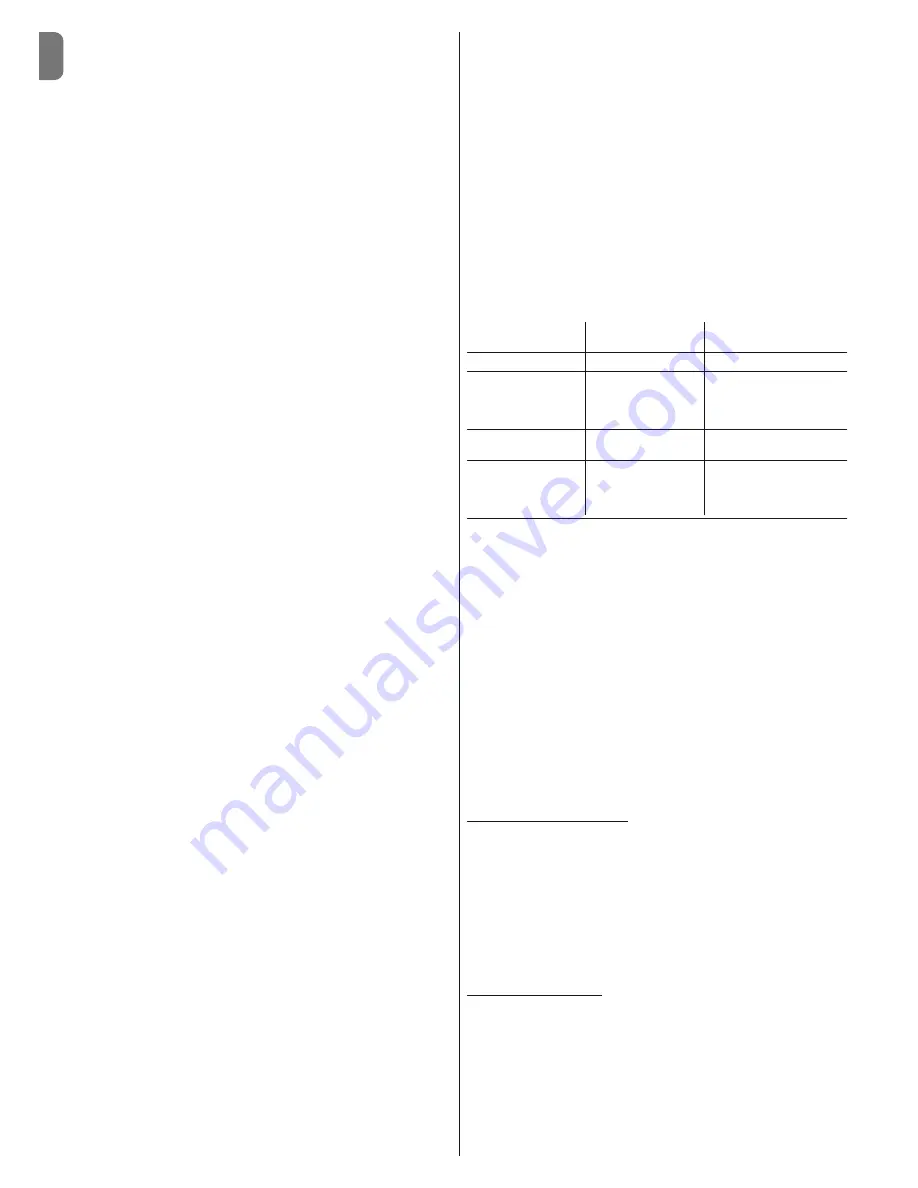
embedded in concrete and other preparation work for the installation can
be completed to finalise the site ready for subsequent installation opera-
tions.
In particular, for digging the pit used to anchor the gearmotor to the
ground, proceed as follows:
01.
Dig the foundation pit in the gearmotor fixture point.
Note
– The
dimensions of the pit must be the same or greater than those of the
foundation plate.
02.
Lay the ducting for the routing of cables.
CAUTION!
– In general, position the ends of the ducting used for
electrical cables in the vicinity of the points envisaged for fixture of
the various components.
Note:
The ducting serves to protect electrical cables and prevent acciden-
tal damage in the event of impact.
To prepare the electric cables required in the system, refer to
fig. 10-10a
and Table 1 – Technical specifications of electric cables.
TABLE 1: Technical specifications of electric cables
Connection
Cable type
Maximum admissible
length
A:
POWER Cable
Cable 3 x 1,5 mm
2
30 m (
note 1
)
B:
FLASHING
Cable 2 x 0,5 mm
2
30 m
LIGHT
with aerial cable
RG58 type shielded
20 m
cable
(less than 5 m recommended)
C:
PHOTOCELL
Cable 2 x 0,5 mm
2
(TX) 30 m
Cable
Cable 4 x 0,25 mm
2
(RX) 30 m
D:
KEY-OPERATED
Cables 4 x 0,25 mm
2
30 m
SELECTOR SWITCH
cable DIGITAL
KEYPAD
General note:
The cables required for the set-up of the system (not included in
the pack) may vary according to the quantity and type of devices envisaged for
the installation.
Note 1:
If greater lengths are required, a cable with a diameter of 3x2.5 mm
2
may be used; in this case earthing is required in the vicinity of the automation
.
CAUTION!
– The cables used must be suited to the installation envi-
ronment; for example a cable type H03VV-F for indoor environments
is recommended and a cable type H07RN-F for outdoor environ-
ments is recommended.
3.5 - Installing the automation components
WARNINGS
•
Incorrect installation may cause serious physical injury to those
working on or using the system.
• Before assembly of the automation, perform the preliminary checks
as described in paragraphs “3.2 – Suitability of environment and gate
to be automated” and “3.3 – Product application limits”.
• Fit one or more sheaths for routing the electric cables.
Fixing the foundation plate
01.
For each of the 4 anchor bolts provided, hand tighten 1 thin M 12 nut
along the entire thread.
02.
Insert the four anchor bolts in the foundation plate (
fig. 3
).
03.
Fit one or more sheaths for routing the electric cables.
04.
Embed the plate in the concrete making sure that it is perfectly level.
In order to use the gearmotor’s slot mounting (
fig. 4
) the correct distance
between the foundation plate and the rack must be observed (so it is nec-
essary to know in advance whether it will be welded to the gate or fixed
with screws and spacers).
Gearmotor installation
01.
Remove the gearmotor cover using a screwdriver to loosen the lateral
screws (
fig. 5
).
Note
– Leave the gearmotor without the cover until the
installation and programming phases have been completed.
02.
Remove the two screw covers, pulling them upwards (
fig. 6
).
03.
Place TH1500 on the already walled foundation plate;
04.
Tighten the 4 low nuts if you wish to adjust the height of the gearmo-
tor (10 mm maximum), otherwise do not use them (
fig. 7
);
05.
Fit the 4 washers;
06.
Tighten firmly the M12 nuts, and any low counter nuts, with a 19 mm
size spanner
• Manually move the leafs to any position and leave stationary, ensuring
that they do not move from this position and that the gate leaf remains bal-
anced.
• Ensure that there is no risk of gate leaf guides coming out of their seats.
• Ensure that the gearmotor fixing zone is not subject to the risk of flood-
ing; if necessary install the gearmotor in a position raised from the ground.
• Ensure that the space around the gearmotor enables safe and easy
manual gate release.
• Ensure that the crushing points between the gate leaf and fixed parts of
the latter are protected during the
Opening
and
Closing
manoeuvres.
• Ensure that the selected surfaces for installation of the various devices
are solid and guarantee a stable fixture. In particular, ensure that the
selected surfaces for fixing the photocells are flat and enable correct align-
ment between photocells.
• Ensure that all devices to be installed are in a sheltered location and pro-
tected against the risk of accidental impact.
• Ensure that the operating temperature range as specified on the prod-
uct dataplate is compatible with the climatic conditions of the place of
installation.
• If the gate leaf incorporates a pedestrian access door or if this door is
positioned in the gate movement area, ensure that this does not prevent
normal gate travel; if necessary install a compatible interlock system.
• Connect the control unit to an electric power line equipped with an earth-
ing system.
• On the power line from the automation, install a device for disconnection
from the power mains, to guarantee a gap between contacts and com-
plete disconnection in the conditions of overvoltage category III. If the pow-
er disconnect device is not in the vicinity of the automation, fit a block sys-
tem against possible inadvertent or unauthorised connection.
3.3 - Product application limits
To ascertain suitability of the product with respect to the specific features
of the gate and area to be automated, the following checks should be per-
formed as well as a check for compliance of the technical data in this para-
graph and the chapter 8 “
Product technical specifications
”.
• Ensure that the dimensions and weight of the gate are within the follow-
ing limits of use:
maximum length
14 m
maximum weight
1500 kg
• Check the overall dimensions of the gearmotor with reference to
fig
.
1
.
Note – These measurements also serve as a reference to calculate the spa -
ce occupied by the foundation pit for routing the electrical cable ducting.
• Ensure that the dimensions of the selected area for mounting the gear-
motor is compatible with the overall dimensions.
• On the gate leaf, ensure that the surface for mounting the rack is suitable
and solid.
Caution!
– If the results of these checks do not conform to specifica-
tions, this model cannot be used for automation of your gate.
3.4 - Preliminary set-up work
Fig. 2
, shows an example of an automation system set up with
Nice
com-
ponents. These parts are positioned according to a typical standard lay-
out.
With reference to
fig. 2
, locate the approximate position for installation of
each component envisaged in the system.
Warning
- the “fixed” control devices must be visible from the gate but
positioned far from moving parts.
The gearmotor is factory set to be installed on the right-hand side of the
gate.
CAUTION!
- If forced to install the gearmotor on the left-hand
side of the gate refer to the instructions in chapter 4 (paragraph 4.1 -
point 07).
Components required to set-up a complete system (fig. 2):
1
- electromechanical gearmotor
2
- pair of photocells
3
- key-operated selector switch or digital keypad
4
- flashing light with incorporated aerial
5
- limit switch brackets
6
- rack
7
- posts for phocells
Before starting installation, ensure that there is all equipment and materials
required for the work concerned. Also ensure that all items are in good
condition and comply with local safety standards.
Dig the routes for the ducting used for electrical cables, or alternatively
external ducting can be laid, after which the pipelines can be
2
– English
EN
Summary of Contents for thor1500
Page 2: ......
Page 65: ...10 A B C C D 6 7 8 9 1 2 mm ...
Page 66: ...11 10a a f g q o r h i l m s b n c d e p ...
Page 67: ...1 2 12 13 ...