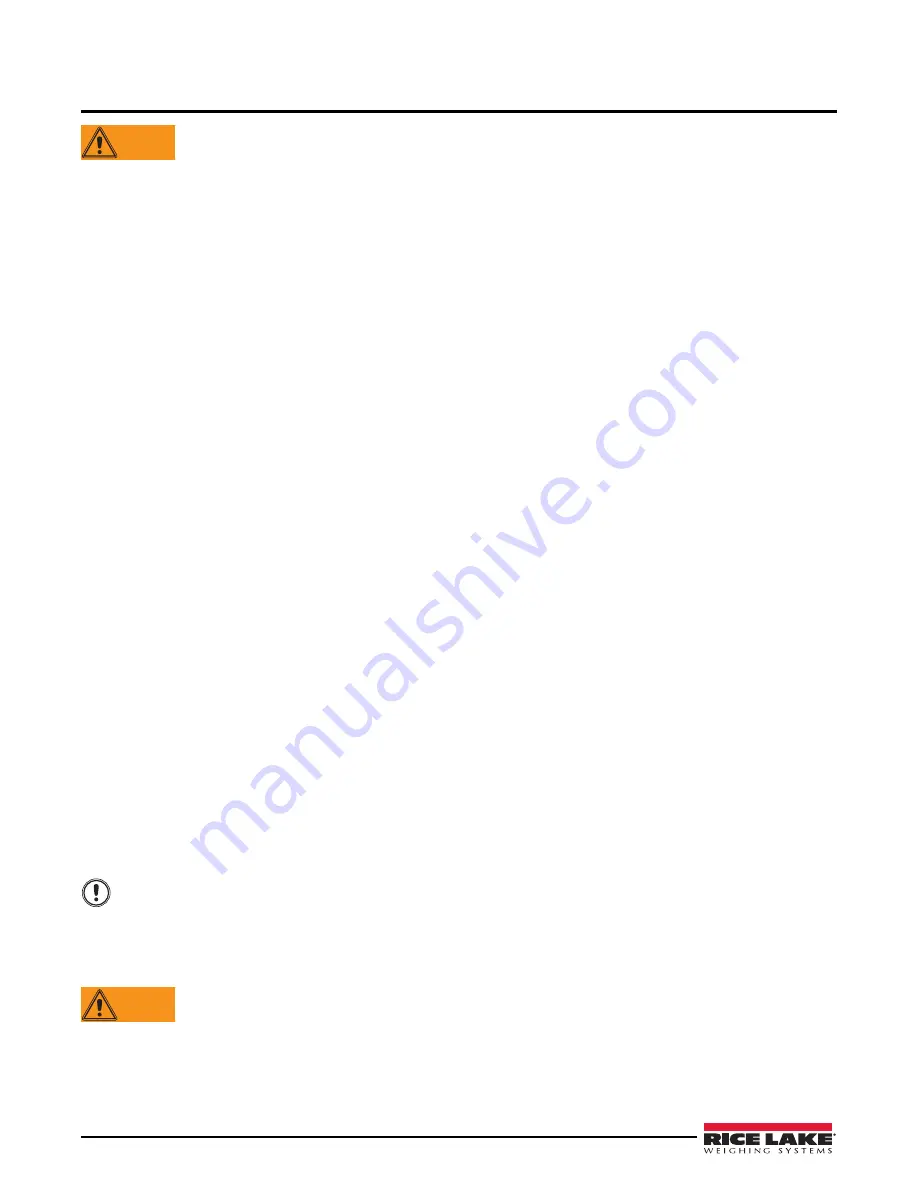
LoadRunner™ Series Installation & Service Manual
1.0
Considerations Before Installation
WARNING
Failure to observe these recommendations and instructions could result in a hazardous
operating condition.
This manual is intended to provide information for the mounting of Onboard Weighing Systems sensors in a
variety of applications. In applying the installation procedures, which follow, some fundamental precautions and
recommendations must be observed by the installer:
• Rice Lake Weighing Systems’ Onboard Scales are designed for applications covering a broad range of
vehicle types. Things to take into consideration are:
- Significant variations in mountings
- Variations in load sensor models
- Specifications
- System configurations
• Installation procedures are similar for both new vehicle mountings and retro-fit mountings. When doing a
retro-fit mounting, ensure that all vehicle structures are free from cracks, excessive wear, corrosion,
alignment problems, etc. that could affect safety and scale performance.
• Load cells, load cell bearing plates, mounting brackets and load cell hardware should be painted upon
installation to help protect the installation from corrosion. Industry appropriate, quality enamel paint is
recommended.
- For environments where high concentrations of salts are used on road surfaces, under-body coating is
recommended (3M™ Underseal™ part number 3M-8883 Universal Rubberized Undercoating).
- Load cells, bearing plates, brackets and hardware should be periodically inspected for any evidence of
rust or corrosion. If areas of corrosion are present, they should be cleaned with a wire brush and
re-painted or undercoated.
- Load cell connectors must be connected or capped during painting or undercoating.
• The instructions outlined herein are designed to ensure that a correct installation will provide maximum
safety, optimum system performance and accuracy, a long operating life, and reasonable installation costs. It
is required that the installer comply with all guidelines and material specifications outlined in this manual,
with special emphasis on detail and inspection of work.
• Installation must comply with appropriate regulations of the U.S. Department of Transportation (DOT), state
and local regulations, the recommended standards and practices of the Society of Automotive Engineers
(SAE), standards of the American Welding Society (AWS), and the recommendations of the truck, trailer and
body, hoist and/or suspension manufacturer.
1.1
Welding Specifications
Welding, metalworking and assembly should only be performed by qualified personnel experienced in welding on
vehicle body structures and sub frames. Only welding equipment of the highest quality should be used in the
welding of load cell bearing plates. When welding, use procedures that ensure high quality welds. Over-welding
may result in distortion and damage, while under welding may not develop adequate strength.
Important
Rice Lake Weighing Systems recommends removal of load cell after tack welding bearing plates in
position so that final welding is performed without load cell being subjected to excessive heat, weld
current, or cable damage.
If welding with load cells in position, the installer must ensure that electrical current cannot flow through the load
cell. All load cell terminals must be shorted together. Attach the ground strap directly to the vehicle frame member
to which the bearing plates will be welded. Never weld directly to a load cell.
WARNING
Always disconnect battery terminals before performing any welding.