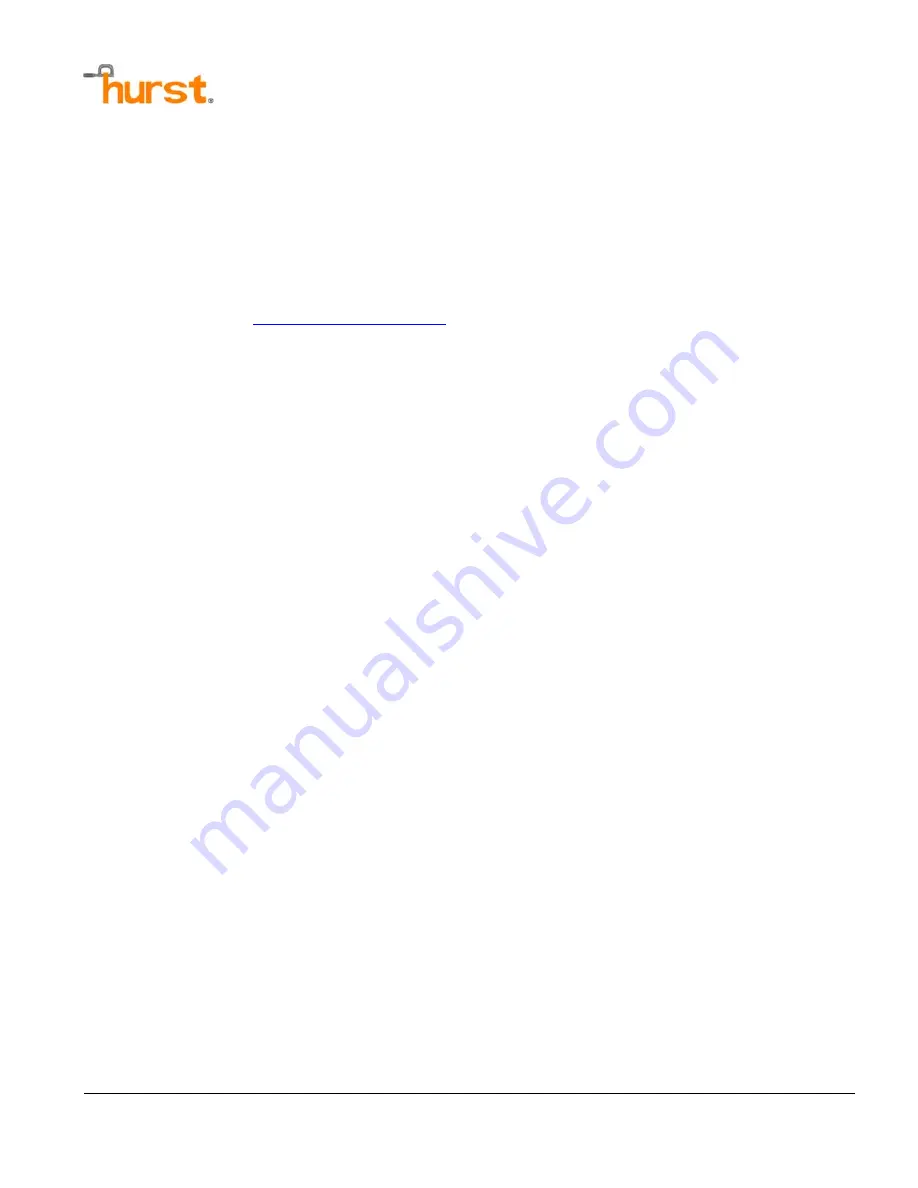
B R U S H L E S S D C M O T O R A N D G R E E N D R I V E
T M
M A N U A L
10
Nidec Motor Company
INTRODUCTION
Thank you for selecting the Dynamo Motor powered by the integrated GreenDrive
TM
control.
This manual contains all basic and necessary information concerning the brushless DC motor and
GreenDrive
TM
control.
If you require any additional information, please contact Nidec Motor Company/Hurst Division
at 812-385-2564 or
hurst@nidec-motor.com
.
Features
NEMA 17 Motor
Ball Bearing System
Stainless Steel Shaft
12 to 36 Vdc Input Voltage
Closed Loop Speed Operating Mode
Pulse Width Modulated (PWM) Control Method
Enable and Direction Inputs
Efficiency up to 85%
Tachometer Output
4-Quadrant Operation
Current Limit Protection
Under Voltage Protection
Industry Standard Connectors
Product Description
The Nidec brushless DC motion control system is an integrated, variable-speed brushless DC
motor and control package. This system includes a low voltage customer interface that can be
connected to a system controller or connected to an external potentiometer, forward/reverse
switch, run/stop switch, or other user I/O. The motor is equipped with a triple-fixed preloaded
ball bearing system and multiple mounting arrangements. The system also includes internal
current limiting, and under voltage protection for system safeguarding.
Two channel encoder signals are available to close system loop internally or externally. The
encoder also permits the user to determine speed and direction of the motor. A Tachometer
signal is also accessible for a low cost alternative to the encoder.
The integrated motor control includes a power amplifier designed to operate directly from a DC
voltage input of 12 to 36 volts. The power amplifier contains an inverter and an optional low