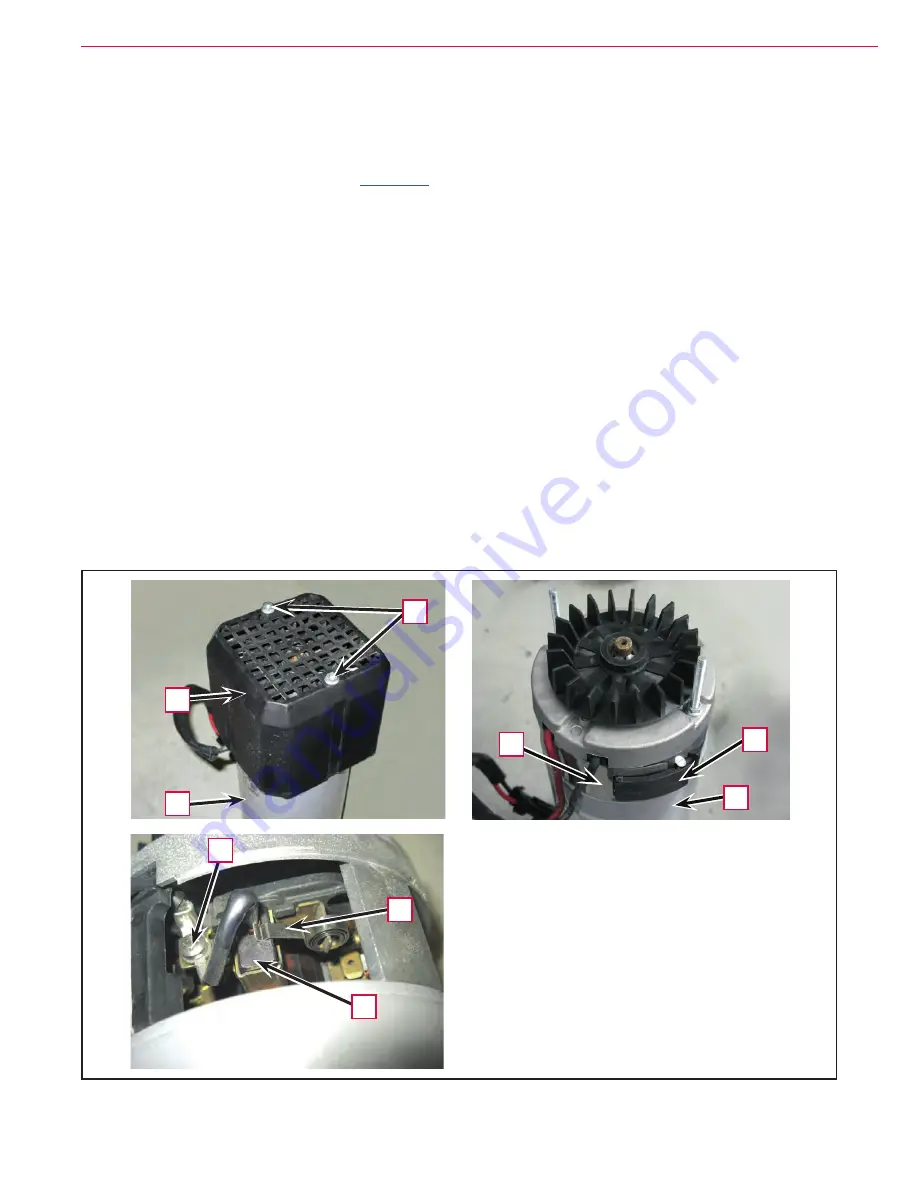
221
Service Manual – SW5500, FLOORTEC R 985
42 - Sweep System, Main Broom
Main Broom Motor Carbon Brush Check/Replacement
Disassembly
1 Remove the main broom motor (see
2 At the workbench, remove the nuts (A) and the guard (B) of the main broom motor (C)
3 If necessary, clean the external side of the motor (C) in the area of the protection band (D)
4 Disengage the cam lever (E) and remove the protection band (D)
5 Remove the fastening screws (F) of the electrical connections of the four carbon brushes (G)
6 Remove the four carbon brushes (G) from their housings, by disengaging them from the retaining
springs (H)
7 Check the two carbon brushes (G) for wear Replace the carbon brushes when: the contact with the
motor armature is insufficient, the carbon brushes are worn, the carbon brush contact surface is not
integral, the thrust spring is broken, etc. If the length of the carbon brushes is insufficient, these must
be replaced
In this cases, replace all motor carbon brushes
Assembly
8 Assemble the components in the reverse order of disassembly
Figure 19:
C
B
D
E
A
G
H
F
C