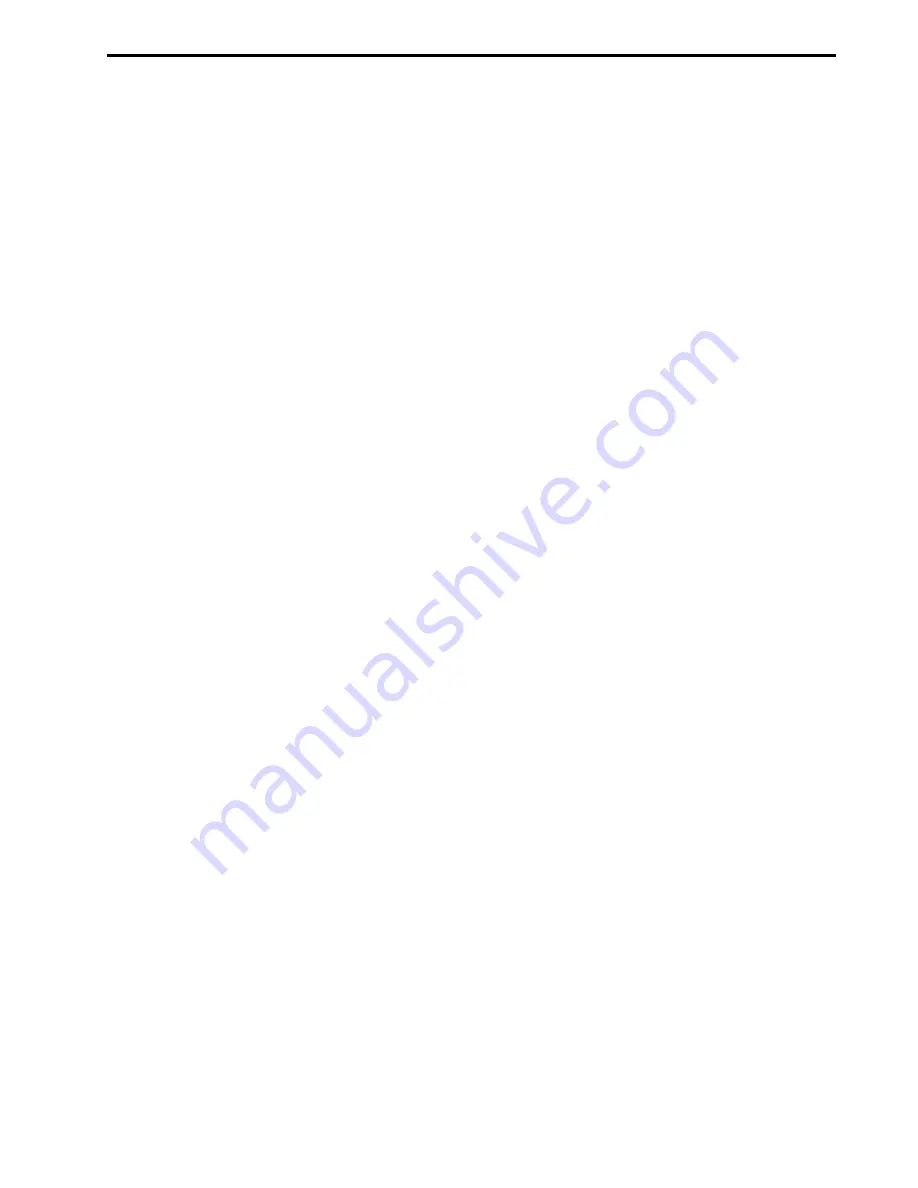
56043021
- 260, 32, 38, 320, 380
SOLUTION SYSTEM
6
Remove the solution cable from the chassis mount (take note of its location in the mount).
7
Tip the solution and recovery tanks to the sides of the machine.
8
Remove the access panel from the front side of the control panel.
9
Disconnect solution cable “M” from solution lever “N”.
10
Remove the solution cable from the chassis mount (take note of its location in the mount).
11
Work the solution cable up and out of the machine.
12
Reassemble in reverse order and test for proper operation.
________________________________________________________________________________________________________________________________________________________________________________________________________________________________________________________________________
TROUBLESHOOTING
________________________________________________________________________________________________________________________________________________________________________________________________________________________________________________________________________
Problem: Not Enough Solution Flow To The Scrub Brushes
1
Kinked solution hoses.
2
Solution valve cable needs adjustment.
3
Plugged screen in the solution tank (32, 38, 320, 380).
4
Plugged solution filter (260 / see figure 1).
________________________________________________________________________________________________________________________________________________________________________________________________________________________________________________________________________
Problem: Solution Leaks With The Valve In The Off Position
1
Solution valve cable needs adjustment.
2
Solution valve defective.
________________________________________________________________________________________________________________________________________________________________________________________________________________________________________________________________________
Problem: More Solution Flow To One Brush Than The Other
1
Kinked solution hoses.
________________________________________________________________________________________________________________________________________________________________________________________________________________________________________________________________________
SOLUTION CABLE REPLACEMENT - 32, 38, 320, 380 (continued...)
13