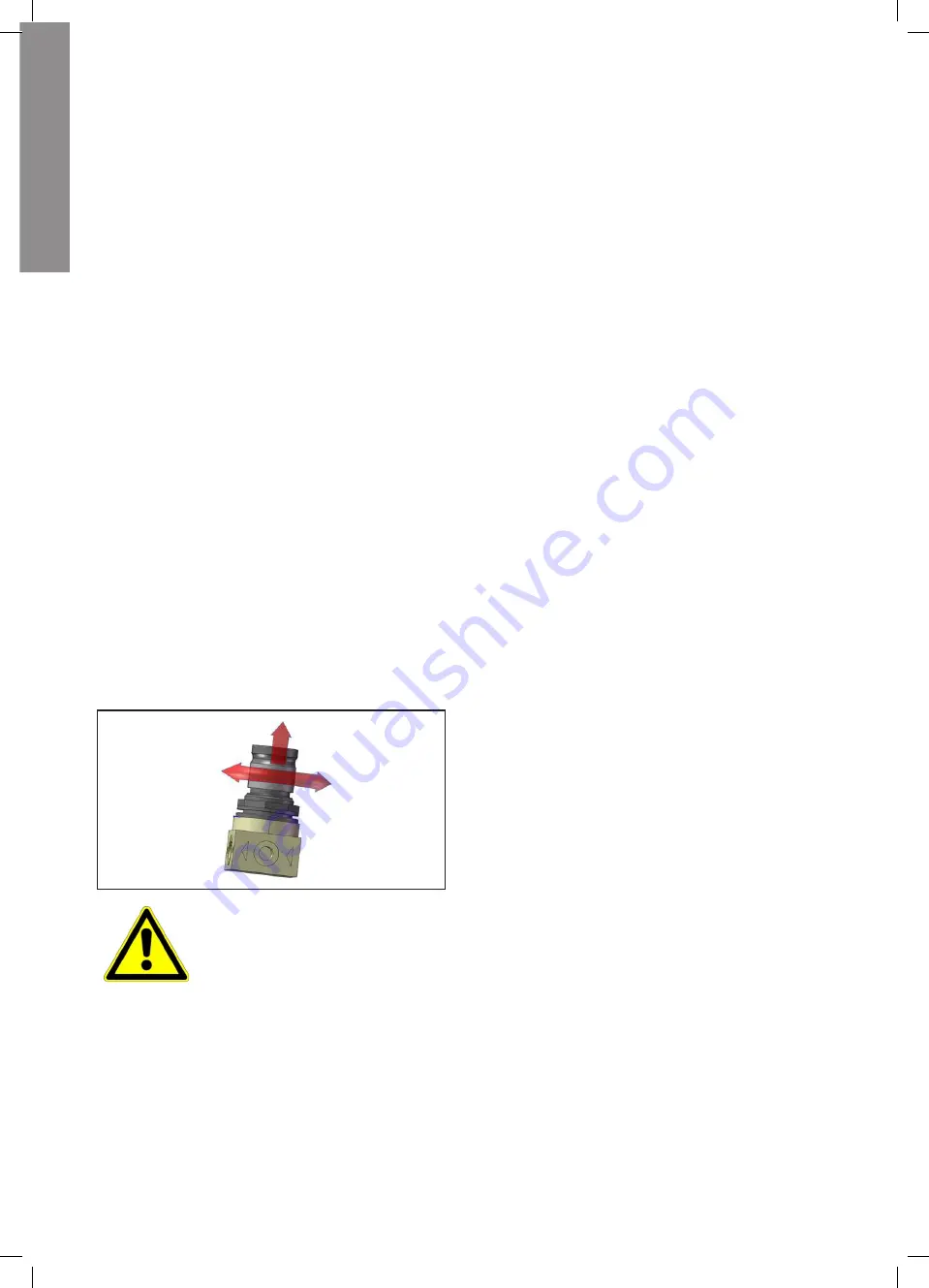
16
Eng
lis
h (
EN
)
7.2. Maintenance, trouble shooting and Service
Maintenance Instructions
1. Quick couplings; it is recommended to lubricate
all couplings parts regularly, (approx. once a
year) by food graded waterproof grease to pre-
vent leaks and damage of o-rings.
2. If the quick couplings leak, o-rings should be
replaced.
3. Depending on usage, maintenance should be
undertaken by an authorised service engineer at
least once a year in order to prevent defects and
failure of operation. Authorised engineers are
persons who due to their skills and experience
have sufficient knowledge of hygiene systems
and are confident with the state work safety regu-
lations, accident preventing regulations, lines and
generally acknowledged technical regulations
such as DIN-norms and VDE-provisions. For
your safety, this cleaning unit has been manufac-
tured according to all relevant regulations valid
in the EU and therefore it has been supplied with
the CE-marking. For further information, please
refer to the service department.
4.
When the cleaning process has been completed
or chemicals have been changed, it is important
to rinse the suction and injector systems in the
following way:
• Replace the can with a can containing clean
water.
•
Put the suction hose into the water can.
•
Connect the foam nozzle.
•
Open the spray gun/outlet valve and keep it open
until the injector has been rinsed through (approx.
30 seconds).
•
Remove the suction hose from the water can.
5.
It is recommended to delime the unit according to
paragraph 9.4
6.
It is recommended to clean the surface inside the
unit at least once a month in order to maintain
parts and avoid corrosion of parts.
Nozzle size in mm
Concentration by 20 Bar in %
0,5
1,9
0,6
2,8
0,7
4,2
0,8
5,6
0,9
6,5
1,1
9,4
1,3
11,5
1,5
13,2
In order to get your equipment adjusted properly we
recommend that your chemical supplier adjust it for
you .
7.1.7. Adjustment of Disinfection
Remove cover from the unit.
Adjustment of the disinfection can be done by means
of a limiting nozzle.
The limiting nozzle is placed in the suction nipple of
the non-return valve (110004589) and can be re-
placed with a smaller or larger nozzle depending on
the concentration needed, please also see table for
guidelines.
7.1.8. Adjustment of air
If adjustment is necessary.
Do not attempt to adjust the Air yourself always con-
tact an authorised service company.
WARNING
:
When working on the compressor be
care full, several parts of the Com-
pressor may be very hot.
The Typhoon/Dual is supplied with an
integrated thermal relay on the com-
pressor. As soon as the temperautre
gets too high,the relay switches off the
compressor (150°C). Once the com-
pressor temperature falls, the thermal
relay switches back on.
Summary of Contents for Hybrid Typhoon
Page 1: ...Hybrid Typhoon Directions for use Gebrauchsanweisung Mode d emploi Instrucciones de uso...
Page 80: ......
Page 86: ...8 2 4 5 6 1 3 7 110004550 Hybrid Typhoon...
Page 88: ...Hybrid Typhoon 1 3 2 4 5 110004554...
Page 90: ...17198_30 1 2 3 Hybrid Typhoon...
Page 92: ...Hybrid Typhoon 110004551 1 2...
Page 94: ...Hybrid Typhoon 1 2 3 4 9 8 7 6 5 10 7 8 12 11 13 110004548...
Page 96: ...Hybrid Typhoon 110004552 1 2 3...
Page 98: ...Installation 658 1435 1011 1107 110004599...
Page 100: ...El diagram 110004767E...
Page 101: ...El diagram...
Page 102: ...El diagram...
Page 103: ...110004775D El diagram...
Page 104: ...El diagram...
Page 105: ...El diagram...
Page 107: ...Pump curve 25 bar 50 Hz...
Page 109: ...Layout Hybrid MU...
Page 111: ......