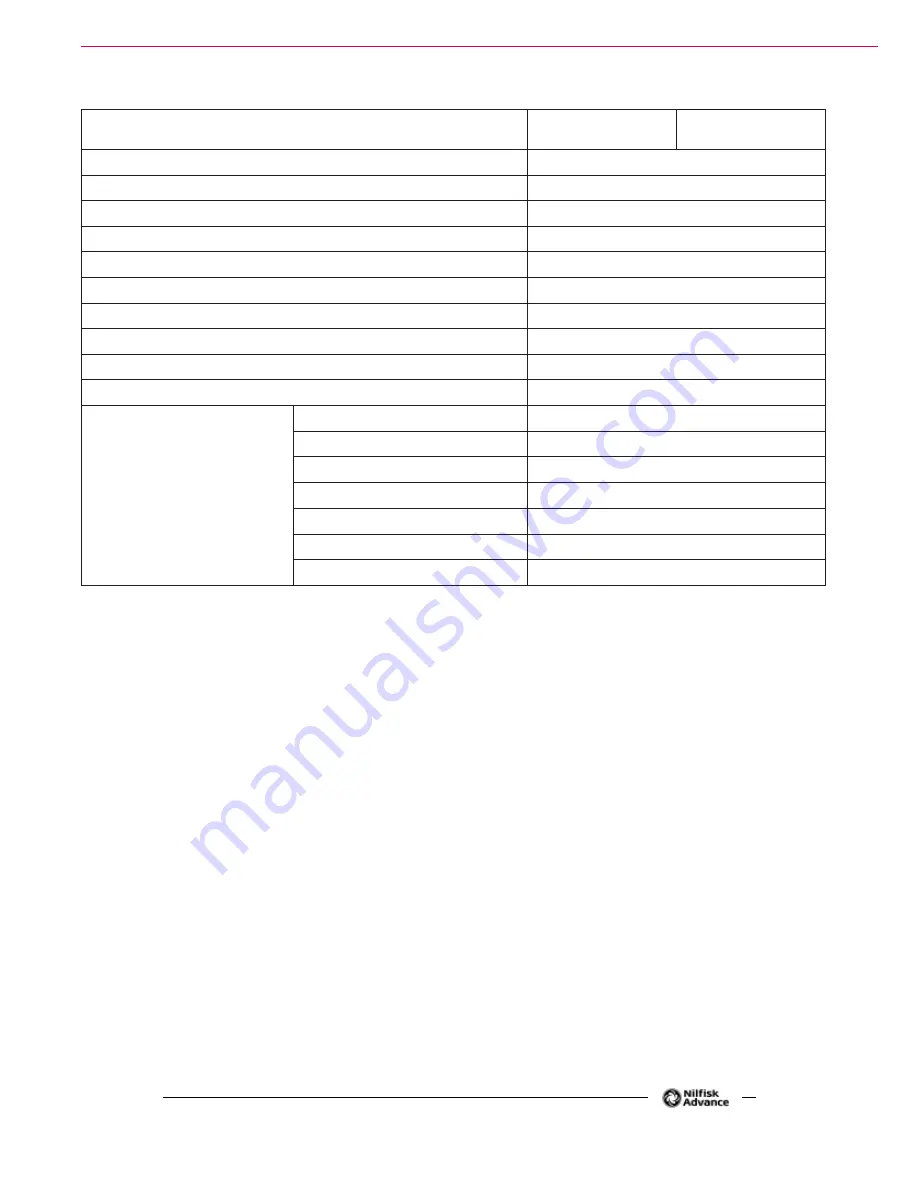
Scrub System, Disc
73
Service Manual – SC2000
Specifications
Description / Model
Advance / Nilfisk
SC2000 53 B
Advance / Nilfisk
SC2000 53 B FULL PKG
Cleaning width
21 in (530 mm)
Brush/pad diameter
21 in (530 / 508 mm)
Brush pressure with extra pressure function turned off
33 lb (15 kg)
Brush pressure with extra pressure function turned on
66 lb (30 kg)
Brush deck right/left offset
65 / 15 mm (2.5 / 0.6 in)
Brush distance from the floor (when lifted)
1.6 in (40 mm)
Brush motor power
0.6 hp (450 W)
Brush rotation speed
155 rpm
Protection class
IP 20
Insulation class
F
Actuator technical data
Spring load
105 ÷ 155 N
Regulated travel
2.6 in (66 mm)
Total travel
3.6 in (98 mm)
Maximum speed
16 mm/s
Voltage
24V
Protection class
IP 44
Insulation class
A