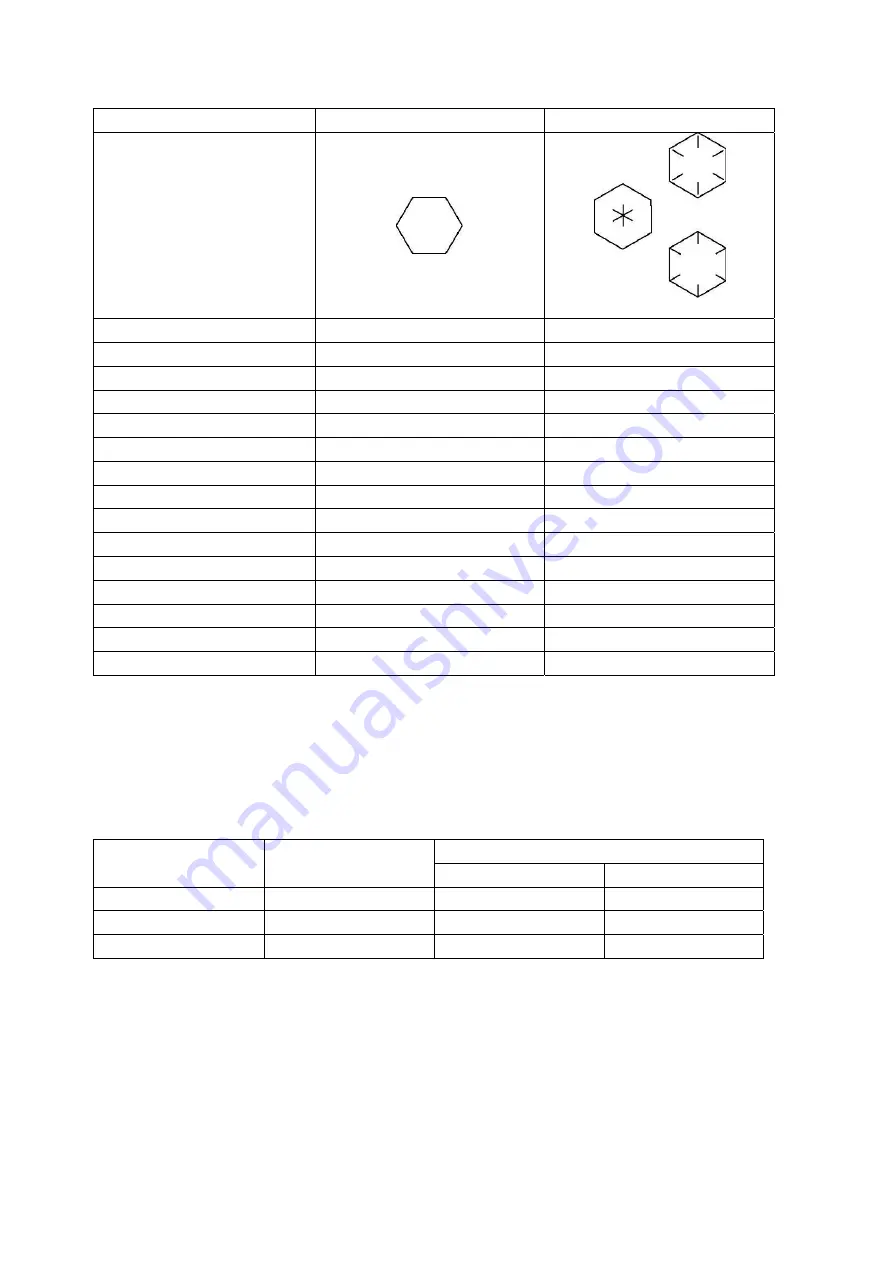
9
INCH TABLE
4T, 5T
10T
Classification Bolt type
Bolt size
Torque kgf · m (lbf · ft)
Torque kgf · m (lbf · ft)
1/4
0.6 ± 0.06
1.7 ± 0.2
5/16
1.2 ± 0.12
3.0 ± 0.3
3/8
2.0 ± 0.20
5.6 ± 0.5
7/16
3.2 ± 0.32
8.9 ± 0.9
1/2
4.7 ± 0.47
13.4 ± 1.3
9/16
6.8 ± 0.68
19.0 ± 1.9
5/8
9.3 ± 0.93
26.1 ± 2.6
3/4
16.0 ± 1.60
45.1 ± 4.5
7/8
25.5 ± 2.55
71.6 ± 7.2
1
38.0 ± 3.80
106.9 ± 10.7
1-1/8
54.1 ± 5.41
152.2 ± 15.2
1-1/4
74.2 ± 7.42
208.9 ± 20.9
1-3/4
98.8 ± 9.88
277.8 ± 27.8
1-1/2
128.2 ± 12.82
360.7 ± 36.1
The torque specifications in above table shall not be applied to the bolts with nylon packings and nonferrous
metal washers, or the ones with specifically designated torque and standard.
H
Newton meter : 1 N·m
=
0.1kgf·m
TIGHTENING TORQUE OF SPLIT FLANGE BOLTS
The following torque shall be applied to the split flange bolts.
Torque
Diameter
(mm)
Flat width
(mm)
kgf·m N·m
10
14
6.7 ± 0.7
66.7 ± 6.8
12
17
11.5 ± 1
112 ± 9.8
16
22
28.5 ± 3
279 ± 29
Summary of Contents for LPT22
Page 15: ...14 3 ELECTRICAL SYSTEM 3 1 ELECTRICAL DIAGRAM WIRING DIAGRAM ...
Page 16: ...15 CONNECTION DIAGRAM ...
Page 30: ...29 3 7 CURTIS CONTROLLER ...
Page 63: ...62 8 2 TROUBLE SHOOT ...
Page 64: ...63 ...
Page 65: ...64 ...