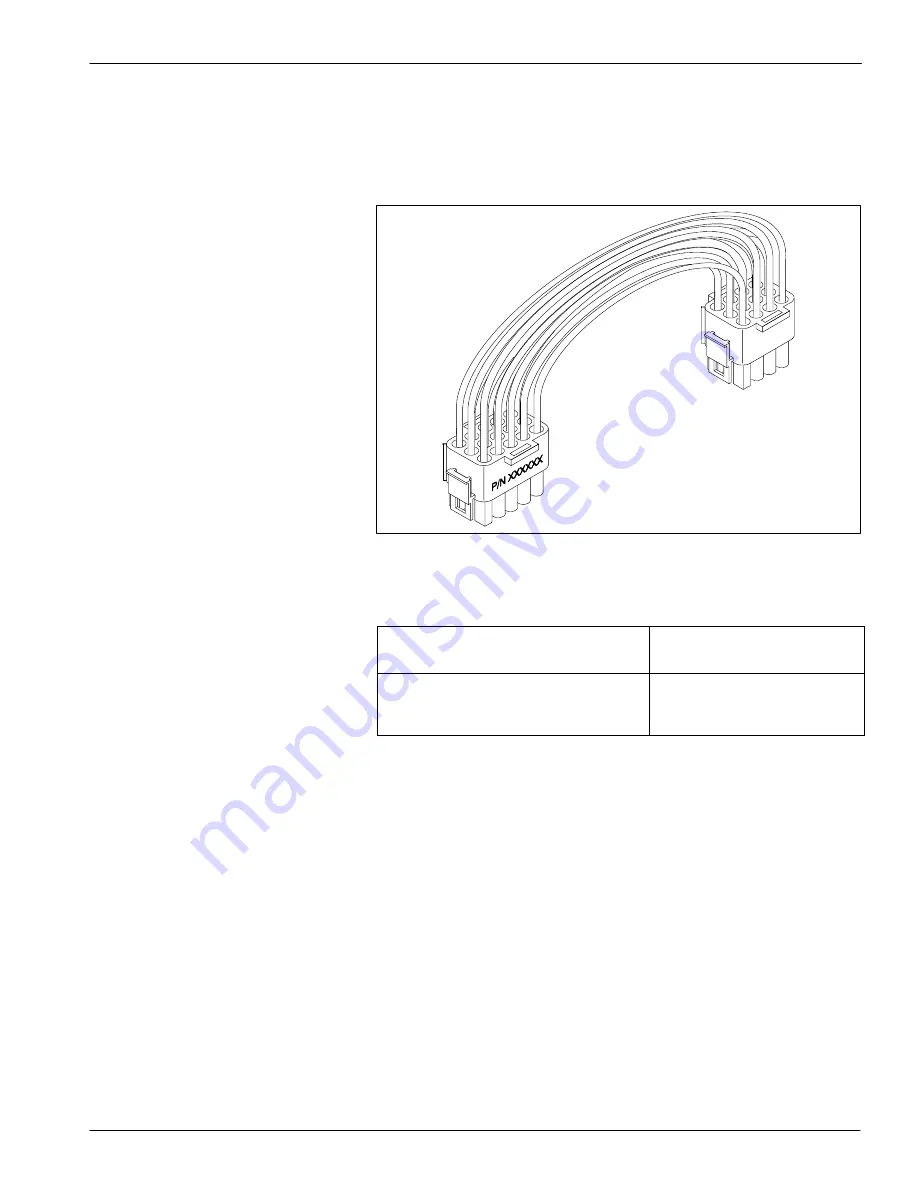
Installation
A 1-37
E
2000 Nordson Corporation
All rights reserved
41-3000
V
Issued 5/00
A3EN-04-[3V-A-AAXP]-12
6. Replace the harness you just removed with the appropriate
single-phase harness supplied in the installation kit. A wiring harness
is shown in Figure A 1-27. The part number of the wiring harness you
must install is listed in Table A 1-10 and on the label of the electrical
enclosure lid.
4130428
Fig. A 1-27 Contactor Board Wiring Harness
Table A 1-10 Wiring Harness Part Numbers
Type of Service
Part Number of Wiring
Harness to Install
200--240 VAC single phase
232 719
230 VAC (with neutral) single phase
232 709
7. Go to the next procedure,
Closing the Electrical Enclosure
.