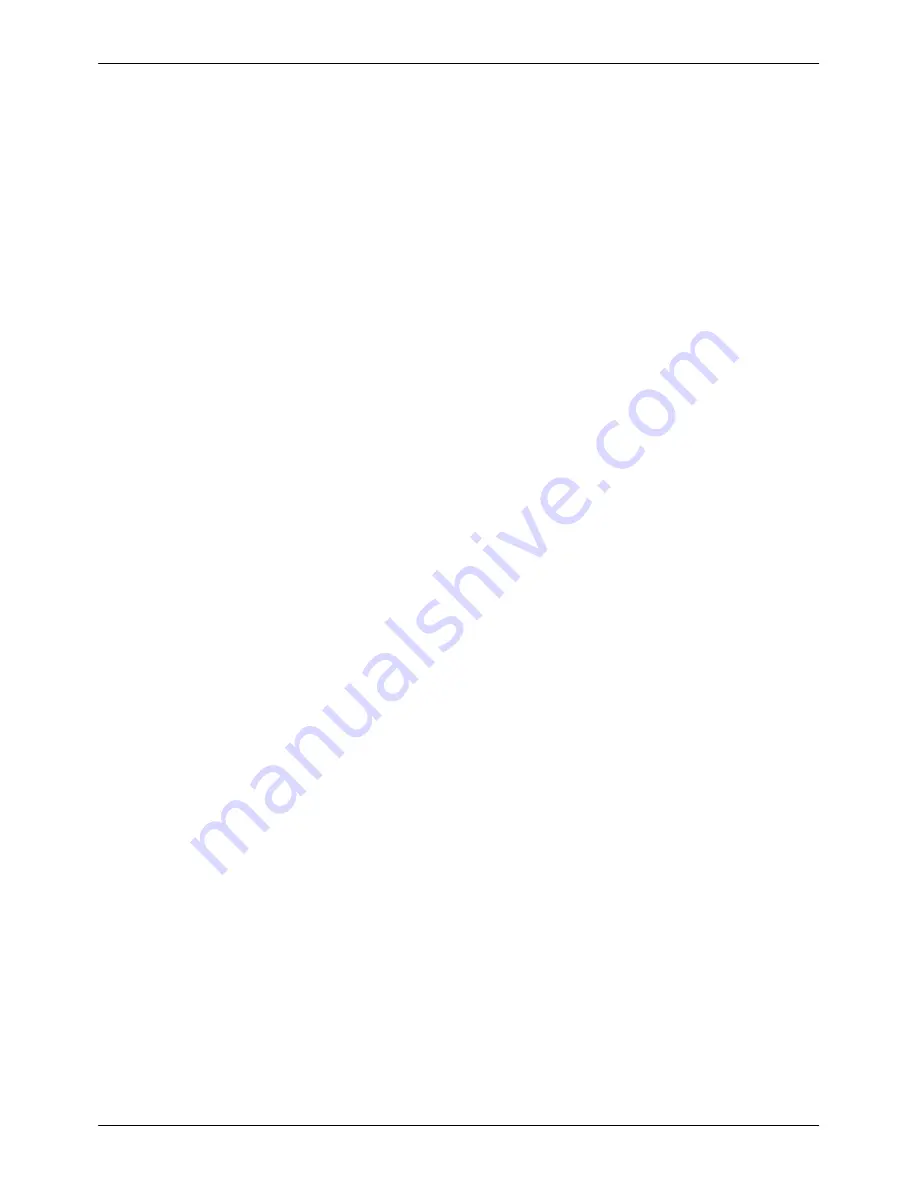
Pinch Valve Assembly
5
Part 768670A
.
2005 Nordson Corporation
Residual Risks
The Pinch Valve Assembly presents no particular risks to operators. The
only residual risks are :
:
Upper limbs of the body being trapped between the top edge of the
surge hopper and the bottom edge of the cyclone when the surge
hopper is being raised.
:
Possible entrapment of operators fingers inside the pinch valve sleeves
during operation, maintenance and cleaning.
:
Risk of powder ingestion if care is not taken when cleaning the surge
hopper. Operators should wear a safety mask and goggles at all times
when cleaning the Pinch Valve Assembly.