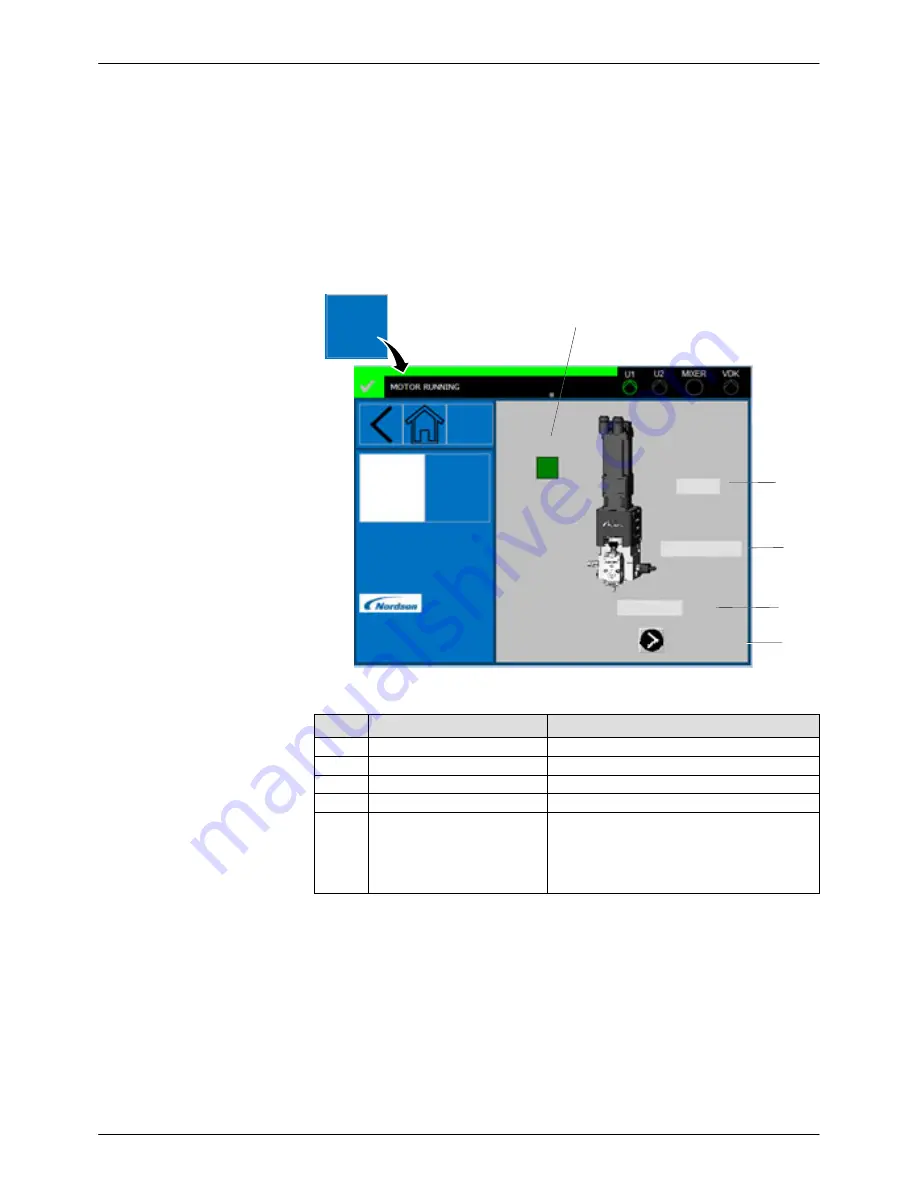
FoamMix Flex Foaming System
67
Part 1129048_01
E
2020
Nordson Corporation
VDK Pump Main Screen
Touch the VDK pump button in the navigation area on the Main screen to
access the VDK options.
VDK Main Screen
Touch the VDK Main button on the VDK main screen to view or change the
VDK pump options.
1
2
3
4
5
Advanced
FoamMix
Version:
DV1
Status
M
VDK
Main
Drive
Setup
VDK
Main
Reset Total KG.:
VDK Pressure:
Volume/Flow OK:
Mpa
NNN
##.####
RPM
NNNN.N
Not enough access rights
MOTOR RUNNING
U1
U2
MIXER
VDK
Total/Flow
Figure 35
VDK Main screen
Item
Component
Function
1
Volume/Flow OK
View whether the volume/flow is okay.
2
RPM
View the current VDK pump speed.
3
Total/Flow
View the flow/volume of the trigger.
4
VDK Pressure
View the actual VDK pump pressure.
5
Reset Total KG
Touch the arrow button to reset the
total amount of dispensed sealant.
NOTE:
You must have proper access
rights to change this option.
Summary of Contents for FoamMix Flex
Page 6: ...Table of Contents iv Part 1129048_01 E 2020 Nordson Corporation...
Page 105: ......
Page 106: ......