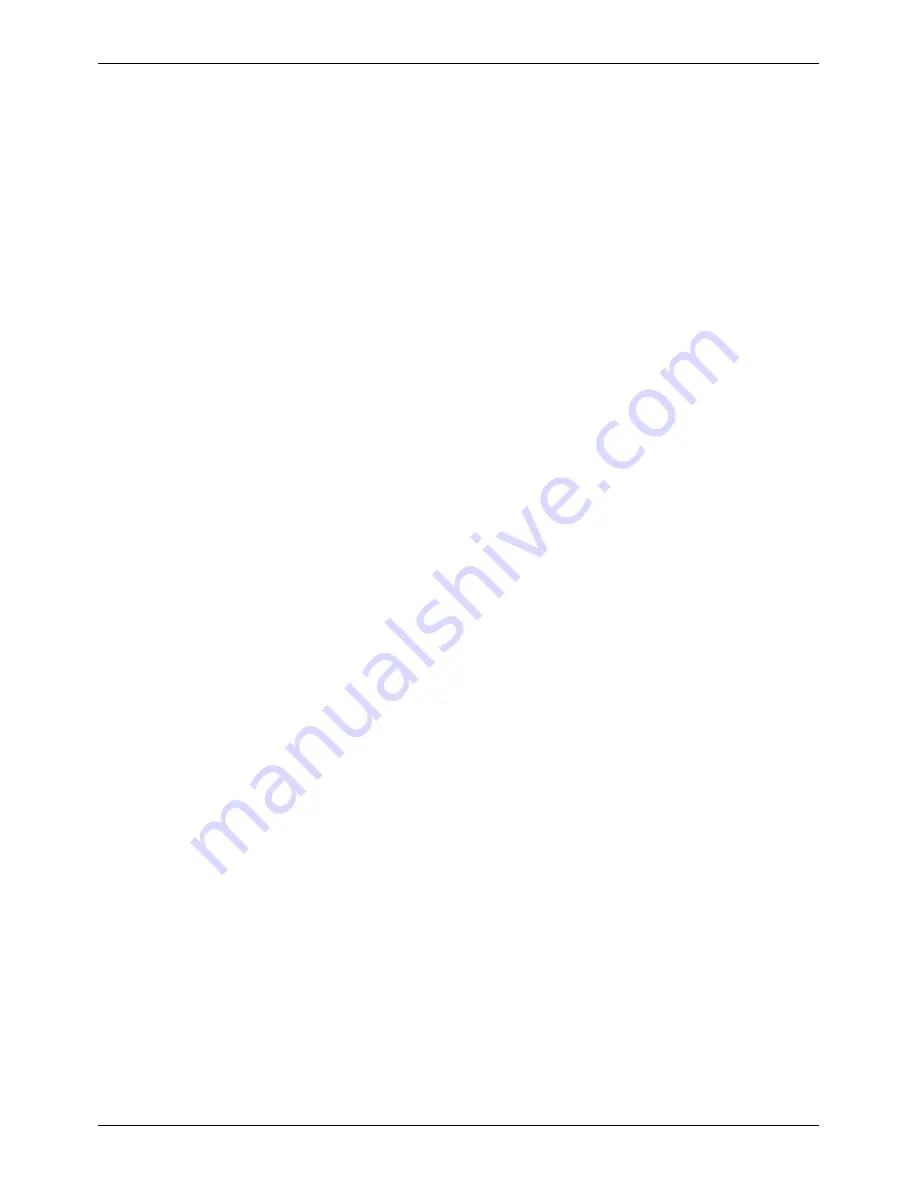
Specifications
9-2
Part 334598G03
E
2008 Nordson Corporation
Gun Electrostatics
Maximum voltage:
93 kV
Maximum output rating current: 122 microamps
NOTE:
Current draw greater than 50
A may affect spray pattern, transfer
efficiency and finish. If the conductivity of your material causes excessive
current draw, changing to the longer hose may be necessary.
Conductivity Range
For optimum electrostatics coating resistivity the conductivity range should
be greater than 25 megohms/cm.
Approvals
This spray gun has met the requirements for CE and FM approval.
Summary of Contents for kinetix
Page 6: ...Table of Contents iv Part 334598G03 E 2008 Nordson Corporation ...
Page 12: ...Safety 1 6 Part 334598G03 E 2008 Nordson Corporation ...
Page 24: ...Installation 3 8 Part 334598G03 E 2008 Nordson Corporation ...
Page 34: ...Maintenance 5 6 Part 334598G03 E 2008 Nordson Corporation ...
Page 60: ...Repair 7 20 Part 334598G03 E 2008 Nordson Corporation ...
Page 70: ...Parts 8 10 Part 334598G03 E 2008 Nordson Corporation ...
Page 75: ...Safety Note KINETIX TRILOGY ATEX Page 3 DOC13015B05 ...