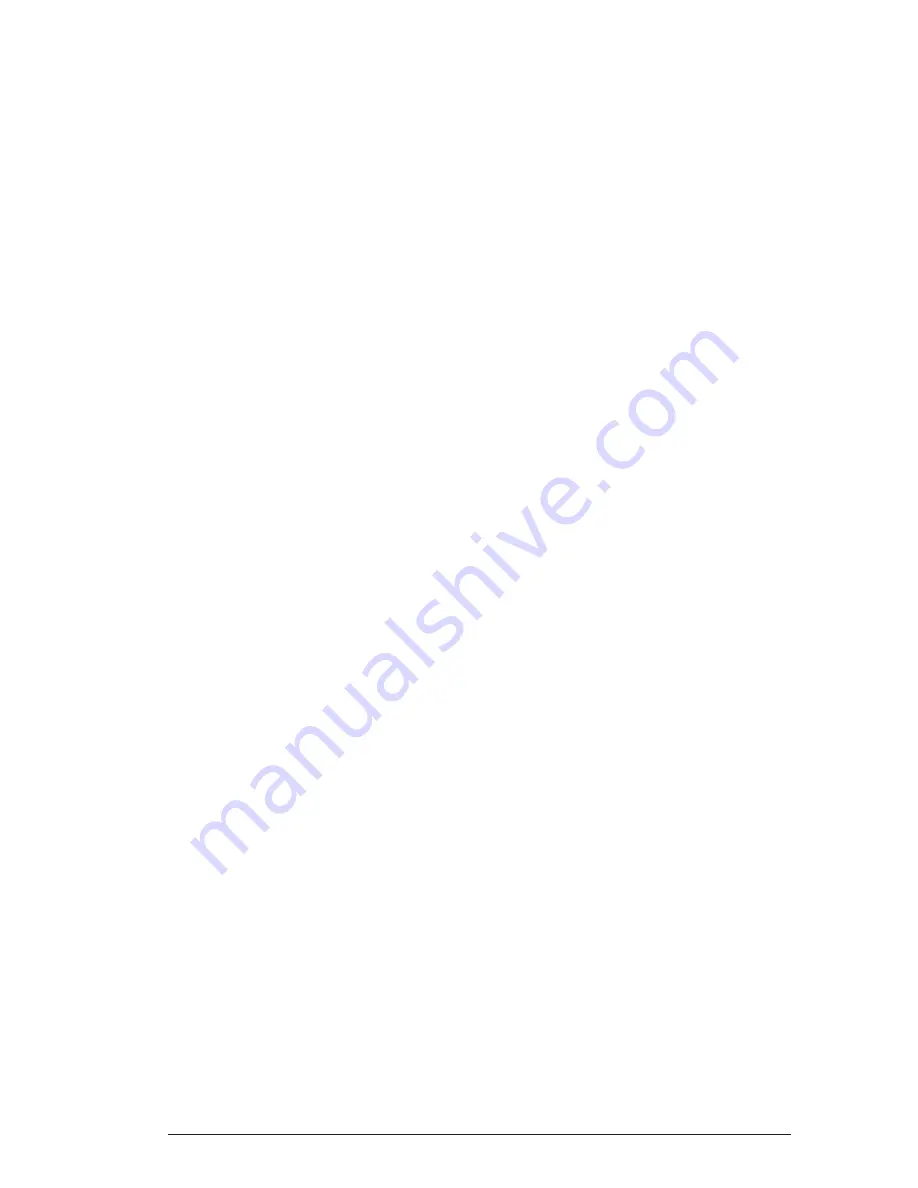
6
All local codes having jurisdiction shall also
apply.
Air Duct Codes and Specifications
Air ducts must be installed in accordance with
National Fire Protection Association standards
NFPA 90A and NFPA 90B, these instructions,
and all applicable local codes.
• Materials: Air ducts must be aluminum, tin
plate, galvanized sheet steel, or other ap-
proved materials for outlet or return air ducts.
• Construction: Snap-Lock or Pittsburgh-Lock
seams are preferred. All other types of
seams must be made tight to prevent leak-
age.
• Sizing: Supply duct system must be designed
for proper air distribution. Static pressure
measured externally to furnace shall not ex-
ceed static pressure rating listed on furnace
nameplate.
• Location of Openings: Duct system must be
designed so that no supply registers are
located in duct system directly below furnace.
Return Air Codes and
Requirements
Non-ducted return air systems may be used for
closet or alcove installations.
NOTE: Applicable installation codes may limit
the furnace to installation in a single-story resi-
dence only. Furnace installations other than
closet or alcove installations require ducted
return air systems.
Air return to the furnace must have a minimum
free area opening (see Table 1).
Acceptable floor or ceiling return air systems for
closet installations with return air entering
through an opening in the closet floor or ceiling
must meet all of the following requirements:
• Return air opening into closet, regardless of
its location, must not be smaller than size
specified on unit data label.
• If located in floor of closet, return air opening
must be provided with means of preventing
its inadvertent closure by a flat object placed
over opening.
• Materials located in return air duct system
must have a flame-spread classification of
200 or less.
• Noncombustible pans having 1" upturned
flanges must be located beneath openings in
a floor-return duct system.
• Wiring materials located in return duct sys-
tem must conform to NEC Article 300-22(c).
• Gas piping must not run in or through return
air duct system.
• If return air opening is located below top of
furnace, a minimum clearance must be pro-
vided between opening and furnace (see
“Accessibility for servicing” in Table 1).
Closed-Off Space Requirements
Living space not served by, and closed off from,
the return air ducts to the furnace by doors,
sliding partitions, and other means must be
provided with permanent, uncloseable open-
ings in the doors or partitions to allow air to
return to the furnace from all parts of the home.
Return air grilles, with a minimum open area of
one square inch for every five square feet of
living space closed off from the furnace, must be
provided in the door or room partition.
OPTIONAL EQUIPMENT
Contact your nearest NORDYNE distributor for
a complete list of electric furnace accessories.
Return Air Grille
A return air grille and frame assembly (see
Figure 2) is available for use in non-ducted
return air installations. In downflow alcove in-
stallations, the grille and frame assembly may
be mounted directly to the top of the furnace. In
closet installations, a wall mount grille is avail-
able for attachment to a door or wall.
Optional Automatic Furnace
Damper #901083 -
Furnace may (not required) be equipped with
the optional automatic damper when a pack-
aged air conditioner is installed and connected
to the warm air duct system. This damper pre-
vents cooled air from discharging through the
furnace cabinet, causing excessive cooling of
the immediate area. Refer to instructions sup-
plied with the damper for details.
Multi-Speed Blower Conversion
Package (4 or 5 ton):
Upgrade blower packages are available for
adding air conditioning or heat pump systems.
See furnace “Options and Compatibility” label
for systems available.