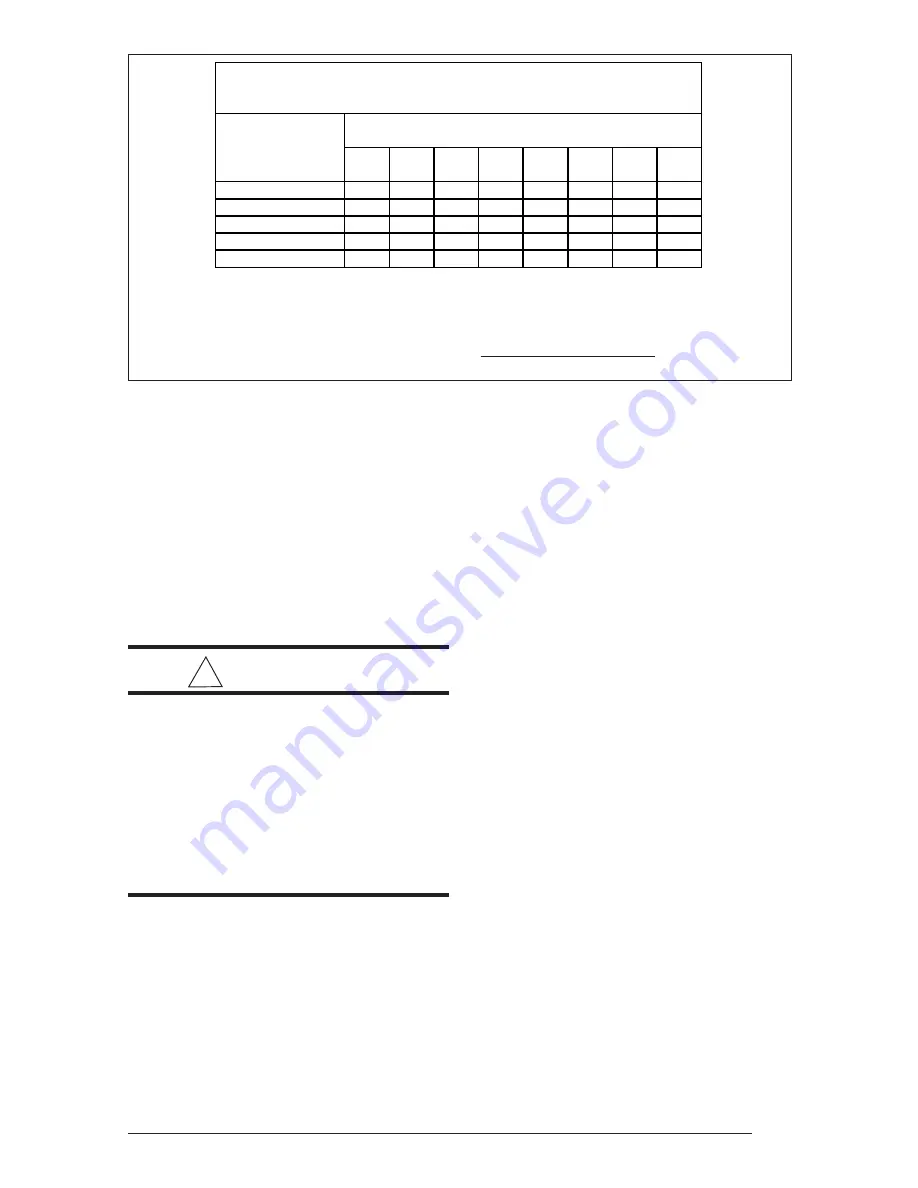
23
Table 6. Capacity of Black Iron Gas Pipe (cu. ft. per hour)
for Natural Gas (specific gravity = .60)
The cubic feet per hour listed in the table above must be greater than the cubic feet per hour of gas
flow required by the furnace. To determine the cubic feet per hour of gas flow required by the
furnace, divide the input rate of the furnace by the heating value of the gas:
Cubic Feet Per Hour Required =
Input To Furnace (Btu/hr)
Heating Value of Gas (Btu/Cu. Ft.)
NOMINAL
LENGTH OF PIPE RUN
BLACK IRON
(feet)
PIPE DIAMETER
(in.)
10
20
30
40
50
60
70
80
1/2
130
90
75
65
55
50
45
40
3/4
280
190
150
130
115
105
95
90
1
520
350
285
245
215
195
180
170
1 1/4
1050
730
590
500
440
400
370
350
1 1/2
1600 1100
890
760
670
610
560
530
CAPACITY OF BLACK IRON GAS PIPE (CU. FT. PER HOUR)
FOR NATURAL GAS (SPECIFIC GRAVITY - 0.60)
NOTE: When pressure testing gas supply lines
at pressures greater than 1/2 psig (14 in. water
column), the furnace must be disconnected from
the gas supply piping system to prevent damage
to the gas control valve.
If the test pressure is less than or equal to 1/2
psig (14 in. water column), the furnace must be
isolated from the gas supply line by closing the
manual shut-off valve.
!
WARNING:
This furnace was equipped at the fac-
tory for use with natural gas only. A
special kit, supplied by the manufac-
turer, is required to convert the fur-
nace to operate on LP/propane gas.
Failure to use the proper conversion
kit can cause fire, explosion, property
damage, carbon monoxide poisoning,
personal injury, or death.
Conversion
Conversion of this furnace to use LP/propane
gas must be made by qualified service
personnel, using only approved parts.
High Altitude Application
High altitude application with this furnace can be
field performed by a simple adjustment of
manifold pressure, and if necessary changing
the orifices. The changes required depend on
the installation altitude and the heating value of
the gas. The gas heating value based on sea
level can be obtained from your local gas utility.
The heating value of gas at high altitude is
always lower than the sea level heating value.
The heating values used in Tables 7 & 8 are
based on sea level values.
Natural Gas High Altitude
Conversion
All factory shipped furnaces are ready to operate
between zero and 4999 ft. above sea level. For
higher altitudes (between 5000 and 10,000 ft.
above sea level), conversion can be achieved
simply by adjusting the furnace manifold pressure
as shown in Table 7.
LP/Propane Gas Sea Level and
High Altitude Conversion
Conversion of this furnace to utilize LP/propane
gas must be made by qualified service personnel,
using factory authorized or approved parts.
Conversion to LP/propane gas can be
accomplished by first replacing the natural gas
orifices with the appropriate LP/propane orifices
shown in Table 9 or 10. Note: for installations
between zero and 5000 ft. above sea level, a
#54 or #55 drill size orifice should be used
depending upon the rated firing rate of the unit
(see Table 9 or 10). However for installations
above 5000 ft. above sea level, a # 55 or #56 drill
size orifice should be used. After changing the
orifices, use Table 8 to determine the appropriate
manifold pressure for your installation.
Summary of Contents for G6RC 90+
Page 2: ......