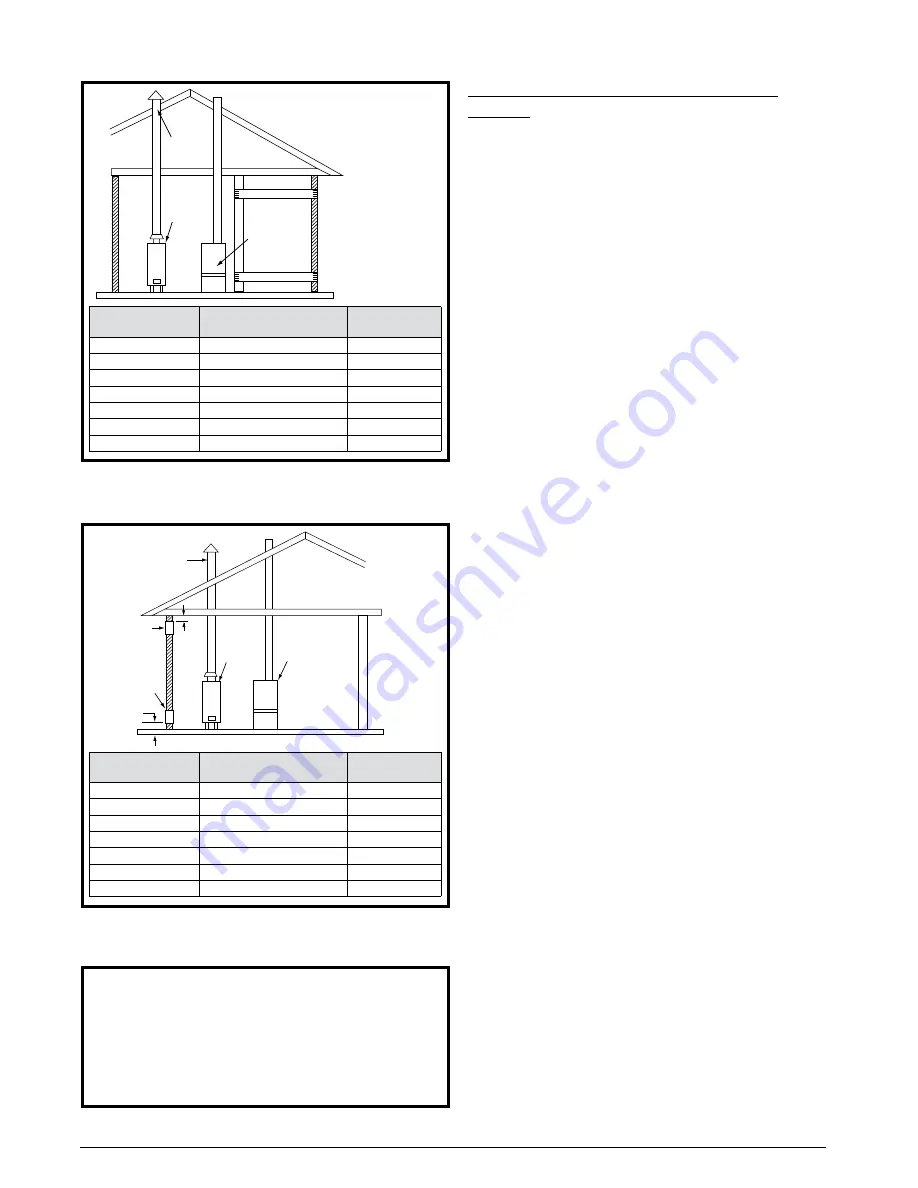
9
Example
:
A space with a water heater rated at 45,000 Btuh
input and a furnace rated at 75,000 Btuh requires a
volume of 6,000 cubic feet [50 x (45 + 75) = 6,000] to
be considered unconfined. If the space has an 8 foot
ceiling, the floor area of the space must be 750 square
feet (6,000 / 8 = 750).
Figure 6
Total Input Rating
(Btuh)
Minimum Free Area
(Each Opening)
Round Duct
Diameter
40,000
10 sq. In
4 inches
60,000
15 sq. In
5 inches
80,000
20 sq. In
5 inches
100,000
25 sq. In
6 inches
120,000
30 sq. In
6 inches
140,000
35 sq. In
7 inches
160,000
40 sq. In
8 inches
NOTE:
Each opening to outside
must be at least 1 sq. in. per
4,000 Btuh of total input rating.
12" Max.
-----
----
-----
----
Furnace
Water
Heater
Vent or
Chimney
12"
Max
See
Note
See
Note
Figure 6.
Combustion Air Drawn from Outside
Through an Exterior Wall
Figure 5
Figure 5.
Combustion Air Drawn from Outside
Through Horizontal Ducts
Total Input Rating
(Btuh)
Minimum Free Area
(Each Opening)
Round Duct
Diameter
40,000
20 sq. In
5 inches
60,000
30 sq. In
6 inches
80,000
40 sq. In
7 inches
100,000
50 sq. In
8 inches
120,000
60 sq. In
9 inches
140,000
70 sq. In
10 inches
160,000
80 sq. In
10 inches
Furnace
Water
Heater
Air Ducts must be
at least 1 sq. in.
per 2,000 Btuh of
total input rating.
Vent or
Chimney
Air Duct
Air Duct
Alternate Method of Providing Air from
Outside
If acceptable under local Codes, it is permitted to provide
outside air using one opening (See NFGC).
Generally, confined spaces must have two openings in
the space for combustion air. One opening must be within
12 inches of the ceiling, and the other must be within
12 inches of the floor. However, an alternative method
recently adopted by the NFGC uses one opening within
12 inches of the top of the space. This method may be
used if it is acceptable to the local codes.
The following conditions must be met:
1. The opening must start within 12” of the top of the
structure and connect with the out of doors through
vertical or horizontal ducts or be ducted to a crawl or
attic space that connects with the out of doors.
2. The opening must have a minimum free area of 1 sq.
in. per 3,000 Btu per hour of the total input rating of all
equipment located in the enclosure.
3. The free area must not be less than the sum of all the
areas of the vent connectors in the enclosure.
Installation in Unconfined Spaces
An unconfined space is an area including all rooms not
separated by doors with a volume greater than 50 cubic
feet per 1,000 Btuh of the combined input rates of all
appliances which draw combustion air from that space.
In general, a furnace installed in an unconfined space will
not require outside air for combustion. However, in homes
built for energy efficiency (low air change rates), it may
be necessary to provide outside air to ensure adequate
combustion and venting, even though the furnace is
located in an unconfined space. See example.
Category IV Venting
This furnace is classified as a “Category IV” appliance,
which requires special venting materials and installation
procedures. This section specifies installation requirements
for Conventional (1-pipe) and Direct Vent (2-pipe) piping.
This type of appliance operates with positive vent pressure
and therefore requires the furnace to be vented to the
outdoors and thoroughly sealed. They also produce
liquid condensate, which is slightly acidic and can cause
severe corrosion of ordinary venting materials. Furnace
operation can be adversely affected by restrictive vent
and combustion air piping.
Summary of Contents for M4RC-072D-35C
Page 47: ...47...