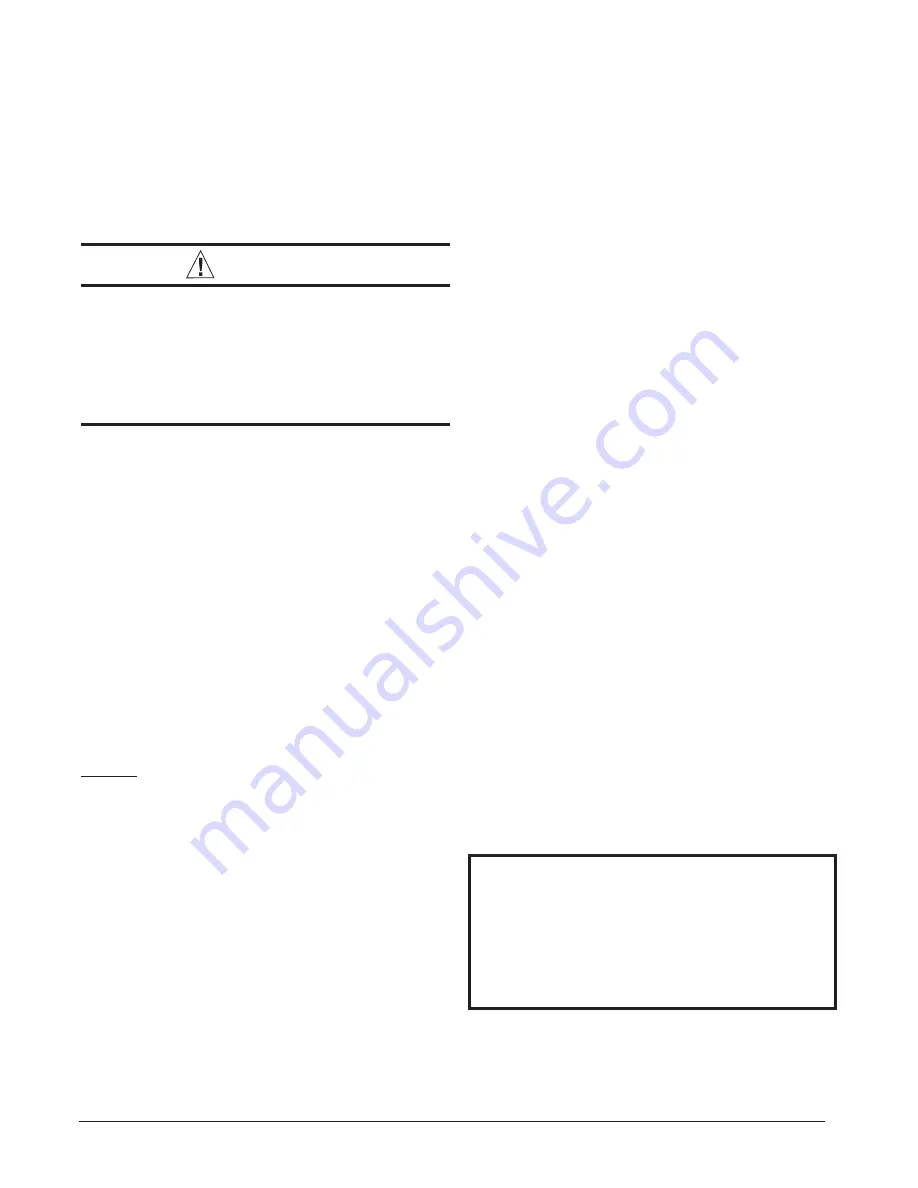
23
IMPORTANT NOTE:
Proper line voltage polarity must
be maintained in order for the control system to
operate correctly. Verify the incoming neutral line is
connected to the white wire and the incoming “hot”
line is connected to the black wire. The furnace will not
operate unless the polarity and ground are properly
connected as shown in Figure 20 (page 22).
Grounding
WARNING:
To minimize personal injury, the furnace cabinet
must have an uninterrupted or unbroken electrical
ground. The controls used in this furnace
require an earth ground to operate properly.
Acceptable methods include electrical wire or
conduit approved for ground service. Do not
use gas piping as an electrical ground!
Twinning
Single stage G7 furnaces are not supplied with a built-
in twinning capability. Other valuable features and
enhancements were made to the new control that made it
necessary to remove the twinning capability. All standard
two-stage furnaces equipped with the fi xed speed iSEER™
motor include a twinning terminal on the blower control
board.
However, if both Single stage G7 furnaces are upgraded
to the fi xed speed iSEER ™ blower, the twin terminal on
the blower control boards may be used. Alternately, off-
the-shelf furnace twinning kits such as Johnson Controls
(P/N 2TC03700124) may be used. Using this control also
provides the additional feature of two-stage operation by
individually controlling the heat section of each furnace.
Contact your furnace distributor for technical details.
IMPORTANT NOTE: G7 furnaces equipped with
variable speed iSEER ™ motors may not be twinned
under any circumstances.
START-UP AND ADJUSTMENTS
Pre-Start Check List
√
V
erify the polarity of the connections are correct, the
line voltage power leads are securely connected and
the furnace is properly grounded.
√
V
erify the thermostat wires (
R
,
W
,
Y
, and
G
) are
securely connected to the correct leads on the
terminal strip of the circuit board.
√
V
erify the gas line service pressure does not exceed
10.0 inches of W.C., and is not less than 4.5 inches
W.C. for natural gas. For LP gas the line service pres-
sure must not exceed 14 in. W.C., and must not be
less than 11.0 in. W.C.
√
V
erify the roll-out and manual reset switch is closed.
If necessary, press the red button to reset a switch.
Note: DO NOT install a jumper wire across a
switch to defeat its function.
If a switch reopens on
startup, DO NOT reset the switch without identifying
and correcting the fault condition.
√
V
erify the blower door is in place, closing the door
switch in the line voltage circuit.
√
V
erify the gas line has been purged and all connections
are leak free.
Start-up Procedures
Do not perform these steps until all of the checks in the
previous steps have been completed:
1. Set the thermostat to the lowest setting.
2. Turn off all electrical power to the furnace.
3. Follow the Operating Instructions on the label attached
to the furnace.
4. Set the thermostat above room temperature and verify
the Operating Sequence (page 25).
5. After 5 minutes of operation, set the thermostat
below room temperature and verify steps 9-10 of the
Operating Sequence (page 25).
Verifying and Adjusting Input Rate
IMPORTANT NOTE:
The input rate must not exceed
the rate shown on the furnace rating plate. At altitudes
above 2,000 feet, it must not exceed that on the rating
plate less 4% for each 1,000 feet.
The input rate must be verifi ed for each installation to
prevent over-fi ring of the furnace. To determine the exact
input rate, perform the following procedures:
1. Shut off all other gas fi red appliances.
2. Start the furnace and run it for at least 3 minutes.
3. Measure the time (in seconds) required for the gas
meter to complete one revolution.
4. Convert the time per revolution to cubic feet of gas
per hour using Table 8 (page 35).
5. Multiply the gas fl ow rate in cubic ft per hr by the
heating value of the gas in Btu per cubic ft to obtain
the input rate in Btuh or see the example.
Example
:
• Time for 1 revolution of a gas meter with a 1
cubic ft dial = 40 seconds.
• From Table 8 read 90 cubic ft gas per hr.
• Local heating value of the gas (obtained from
gas supplier) = 1,040 Btu per cubic ft.
• Input rate = 1,040 x 90 = 93,600 Btuh.
6. The manifold pressure must be set to the appropriate
value for each installation by a qualifi ed installer,
service agency or the gas supplier.