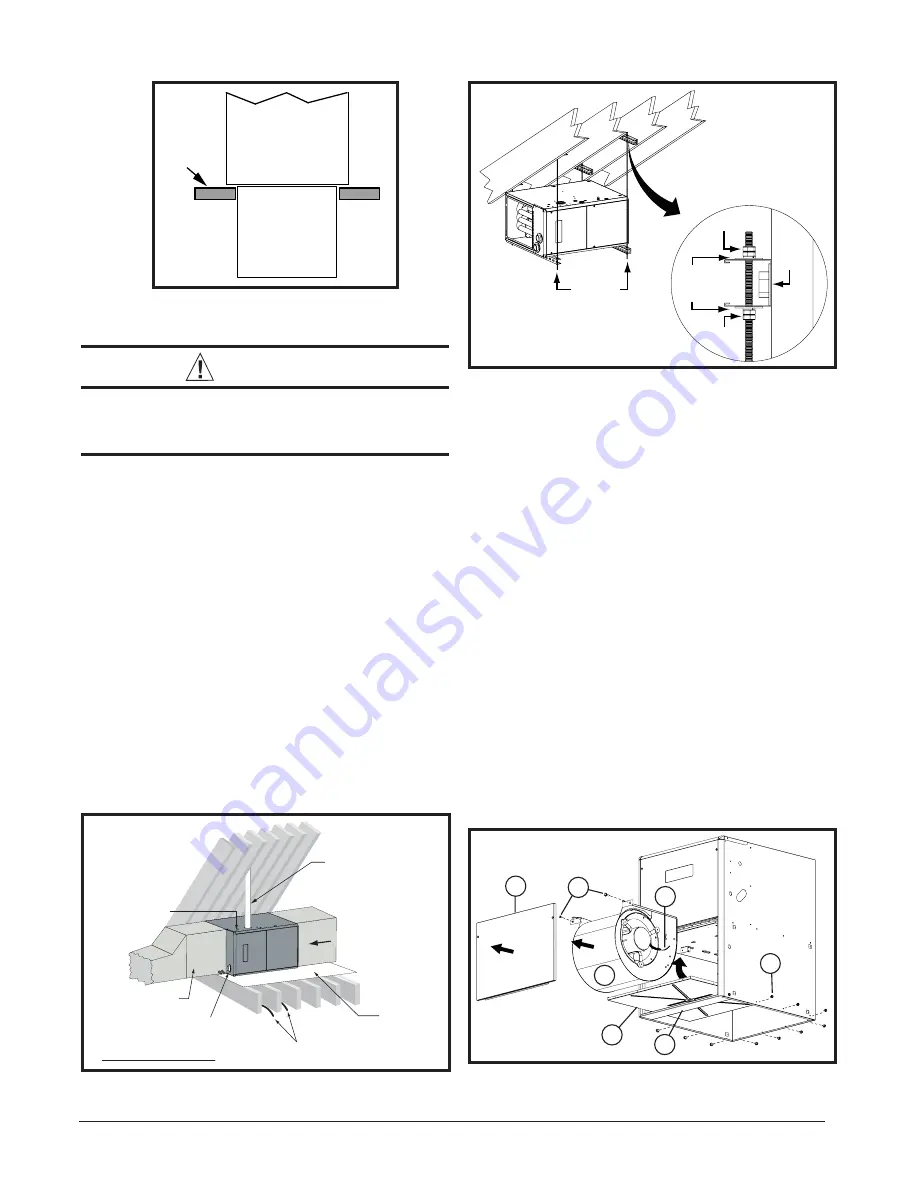
17
Figure 11. Furnace on a Concrete Slab
Concrete
Floor
Furnace
Sheet
Metal
Plenum
Horizontal Installation
WARNING:
The furnace must not be installed directly on
carpeting, tile, or any combustible material other
than wood fl ooring.
The *TC series gas furnace can be installed horizontally
(Figure 12) in an attic, basement, crawl space or alcove.
It can also be suspended from a ceiling in a basement
or utility room in either a right to left airfl ow or left to right
airfl ow as shown in Figure 13.
*TC series furnaces are shipped with the bottom panel
installed. If furnace is installed horizontally, remove the
bottom panel from the furnace before attaching the duct
system. See Bottom Panel Removal section.
If installing the furnace in an attic, it is required that a drip
pan be placed under the furnace. If the installation is on
a combustible platform (Figure 12), it is recommended
that the drip pan extend at least 12 inches past the top
and front of the furnace.
If the furnace will be suspended from the ceiling, assemble
a support frame (Figure 13) using slotted iron channel
and full threaded rod. Fasten the frame together with nuts,
Figure 12. *TC Horizontal installation on a Platform
Exhaust Pipe
Vented to Outside
Combustible
Platform
Coil Plenum
Combustion Air
Condensate Drain Lines
Must Be Trapped
With J-Trap or Field Supplied Loop.
One-Pipe Installation Shown
Airflow
Electrical Supply
Connection
washers, and lockwashers. Secure the support frame to the
rafters with lag bolts. The furnace can also be suspended
using steel straps around each end of the furnace. The
straps should be attached to the furnace with sheet metal
screws and to the rafters with bolts.
It is recommended for further reduction of fi re hazard
that cement board or sheet metal be placed between the
furnace and the combustible fl oor and extend 12 inches
beyond the front of the door and top of the furnace.
Bottom Panel Removal
The steps listed below describe how to remove the bottom
panel from the furnace. See Figure 14.
1. Remove the door (1) from the blower compartment.
2. Disconnect the blower motor wiring harness (2) from
the control board.
3. Remove two screws (3) securing the blower assembly
(4) to the furnace.
4. Carefully pull the blower assembly (4) out thru the
front of the furnace.
Figure 13. *TC Horizontally Suspended
in Attic or Crawl Space
Lag
Bolt
Nuts (x2)
Washer
and
Lockwasher
Nuts (x2)
Threaded
Rod
6
7
5
1
2
3
4
Figure 14. Bottom Panel Removal