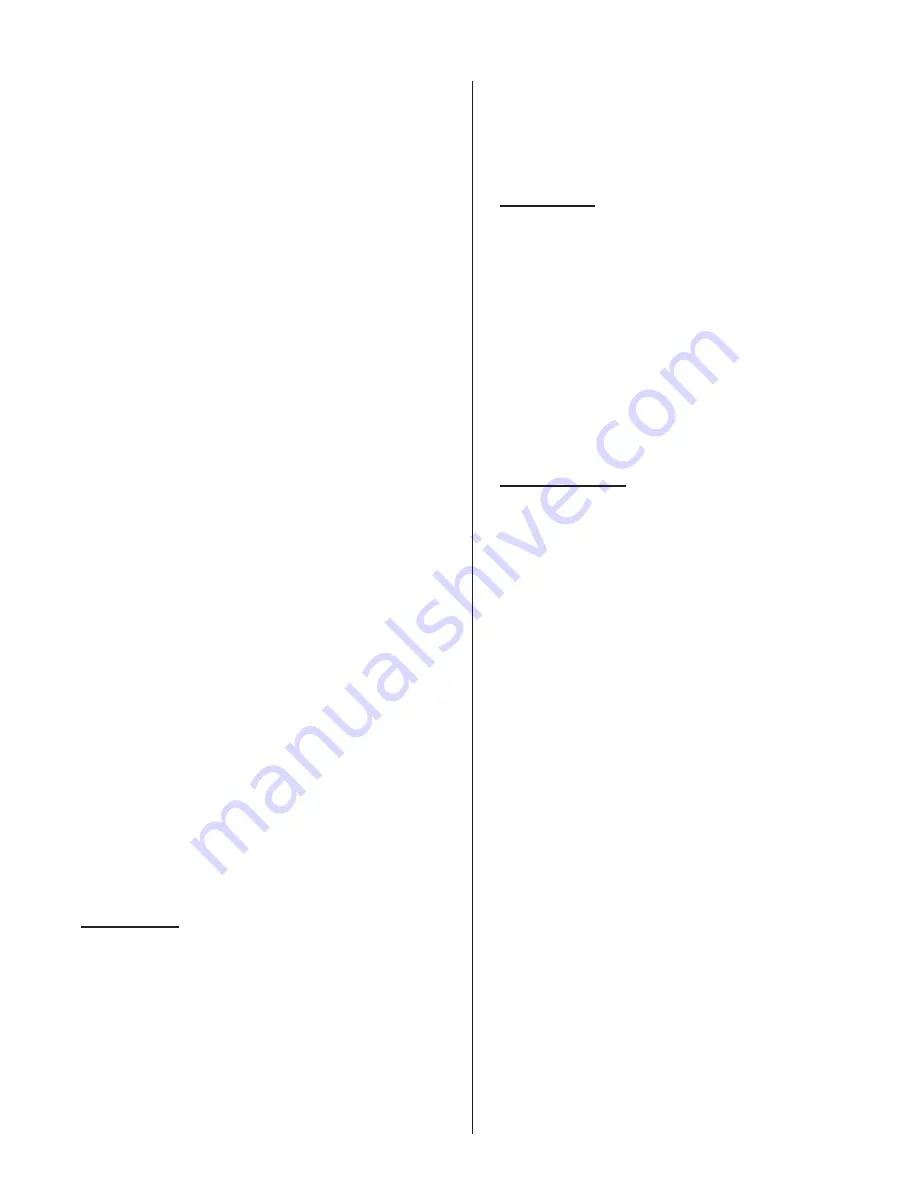
The switch board must be replaced into the same
position as before cleaning and the tie -wrap must be
used to hold the float chamber in position.
SERVICING THE UNIT
Caution:
Disconnect power before servicing this
appliance.
Caution:
Label all wires prior to disconnection
when servicing controls. Wiring errors can cause
improper and dangerous operation.
The combustion chamber, heat exchanger and
flue baffles are all fabricated from stainless steel and
do not require internal cleaning.
Should the main burner fail to light, or flame is not
detected during the first trial for ignition period, the gas
valve is de-energized and the control goes through an
interpurge delay before another ignition attempt. The
control will attempt two additional ignition trials before
going into lockout. The valve relay will be
de-energized immediately, and the combustion blower
will be turned off.
SERVICE CHECKS
COMBUSTION BLOWER
The combustion air blower motors are
permanently lubricated and do not require lubrication.
Clean out any dust that has accumulated in the blower
housing using an air gun.
BURNER
The burners are made of ceramic fabric material
and operate in the infrared mode. Depending on the
environment, the burner(s) may require removal of lint
or grease-laden dust periodically. This may be
achieved by removing the burner and applying
pressurized air to the external surface of the material.
Refer to the Servicing Section related to burner
removal.
Flame Sensor
Flame current is the current which passes through
the flame from the sensor to ground. The ignition
module must detect a minimum flame current of 0.7
microamps or a flame proving lockout will occur. To
measure flame current, connect an DC micrometer to
the FC- FC+ terminals on the module. Meter should
read 0.7 uA or higher. If meter reads below “0” on
scale, meter leads are reversed. Disconnect power
and reconnect meter leads for proper polarity.
NOTE:
Proper polarity of supply voltage to the
unit is necessary for flame sensing to occur. Oxidation
on flame sensing rod can reduce measured current.
The oxidation can be cleaned from the sensing rod
using steel wool or an emery cloth.
Igniter Check
If the igniter is suspected of being defective then
the following test may be carried out;
1.
Ensure that the power and gas is switched off
before servicing.
2.
To test the igniter, disconnect the igniter leads
from their terminal connections.
3.
Using a multimeter set the Ohm’s scale and
place one of the meter leads on one of the
igniter wire ends and the other meter lead on
the end of the other igniter wire.
Gas Valve Setting
The gas valves used in the GS series humidifier
are negative-pressure-regulated valves. The valve
setting listed on the product rating plate is shown
relative to atmosphere – this setting will always remain
constant.
The valves come preset from the factory for the
correct gas type. If an adjustment is required, use the
following steps:
1.
Remove the screw from the pressure port
marked “out” on the back side of the gas
valve.
2.
Connect a hose from a digital manometer (or
an inclined manometer capable of reading
below 0.1”w.c.) to the “out” pressure port.
3.
Activate the humidifier and measure the gas
valve pressure once the valve is energized
and a flame is established in the combustion
chamber. Verify this pressure to the pressure
listed on the unit specification label.
4.
If the pressure needs adjusting, remove the
locking cap on the top of the gas valve.
5.
Below the locking cap is an adjustment screw.
Increase the pressure by turning the
adjustment screw clockwise, decrease by
turning counter-clockwise.
NOTE: The pressure will fluctuate slightly as
the unit operates, especially with very
sensitive measuring devices. Use the mean
pressure value as the set pressure.
- 31 -
Summary of Contents for GS 100
Page 76: ......