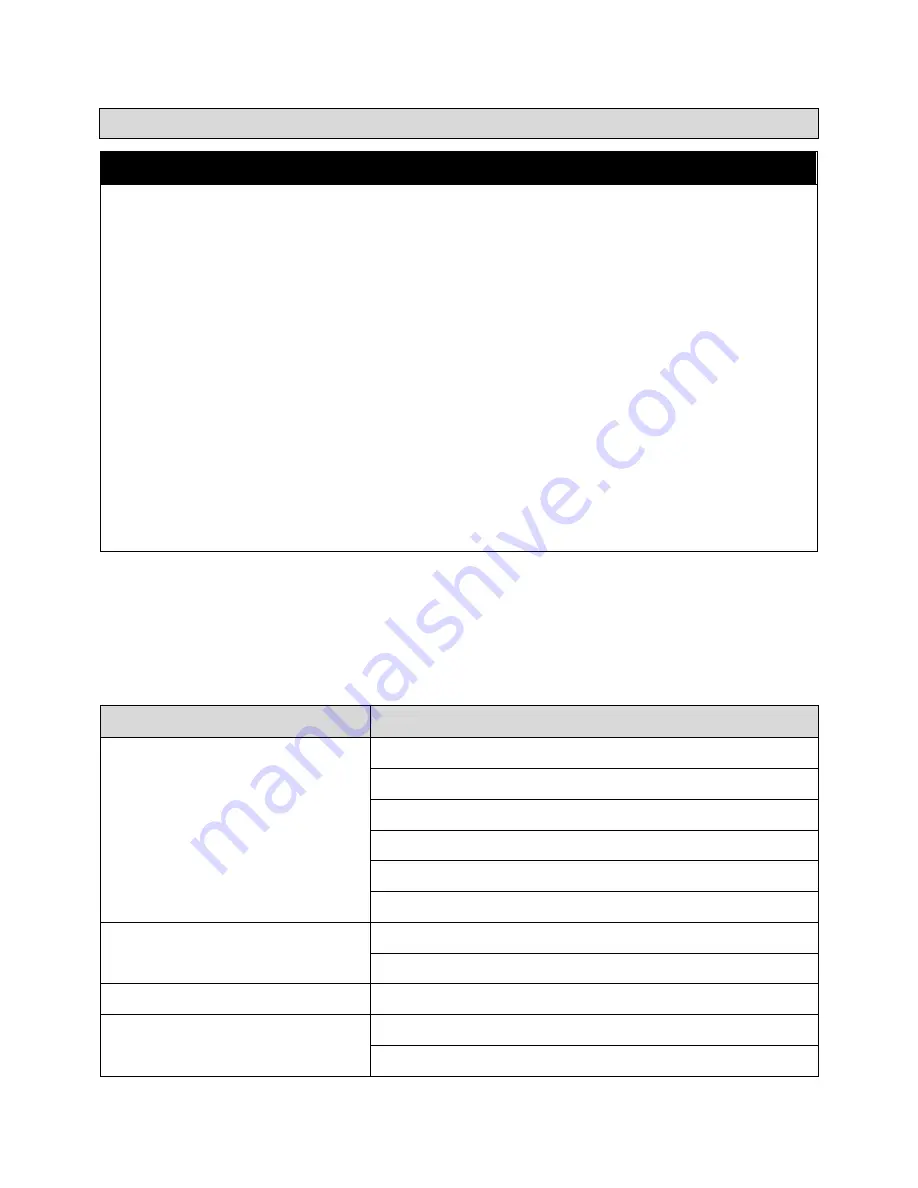
Page 20 of 36
Maintenance
⚠
WARNING
•
Risk of unsafe operation.
Unit cycles automatically when power is on. When performing
maintenance, you may be exposed to voltage sources, compressed air, or moving parts. Personal
injuries can occur. Before performing any maintenance or repair, disconnect power source from the
compressor and bleed off all air pressure.
•
Risk of bursting.
If the safety valve does not work properly, over-pressurization may occur, causing
air tank rupture or an explosion.
•
Risk of burn.
Tubes, pump head, and surrounding parts are very hot; do not touch these. See the
Hot Surfaces section with areas identified in Figure B. Allow compressor to cool prior to servicing.
•
Risk from flying objects.
Always wear certified safety equipment: ANSI Z87.1 eye protection
(CAN/CSA Z94.3 with side shields).
•
Risk from noise.
Use ear protection ANSI S12.6 (S3.19) as air flow noise is loud when draining.
•
Risk of bursting.
Water will condense in the air tank. If not drained, water will corrode and weaken
the air tank causing a risk of air tank rupture.
•
Drain tank to release air pressure before removing the oil fill cap or oil drain plug.
To ensure efficient operation and longer life of the air compressor outfit, a routine maintenance schedule
should be prepared and followed. The following routine maintenance schedule is geared to an outfit in a
normal working environment operating on a daily basis. If necessary, the schedule should be modified to
suit the conditions under which your compressor is used. The modifications will depend upon the hours of
operation and the working environment. Compressor outfits in an extremely dirty and/or hostile
environment will require a greater frequency of all maintenance checks. NOTE: See Operation section for
the location of controls.
Maintenance Interval
Maintenance Point
Daily
Drain air tank
Check pump oil level
Oil leak inspection
Inspect drive belt
Check for any unusual noise/vibration
Check for air leaks*
Weekly
Inspect air
Clean compressor exterior
Monthly
Check drive belt tension
1 Year or 100 operating hours
Change pump oil **+
Check pulley/flywheel alignment