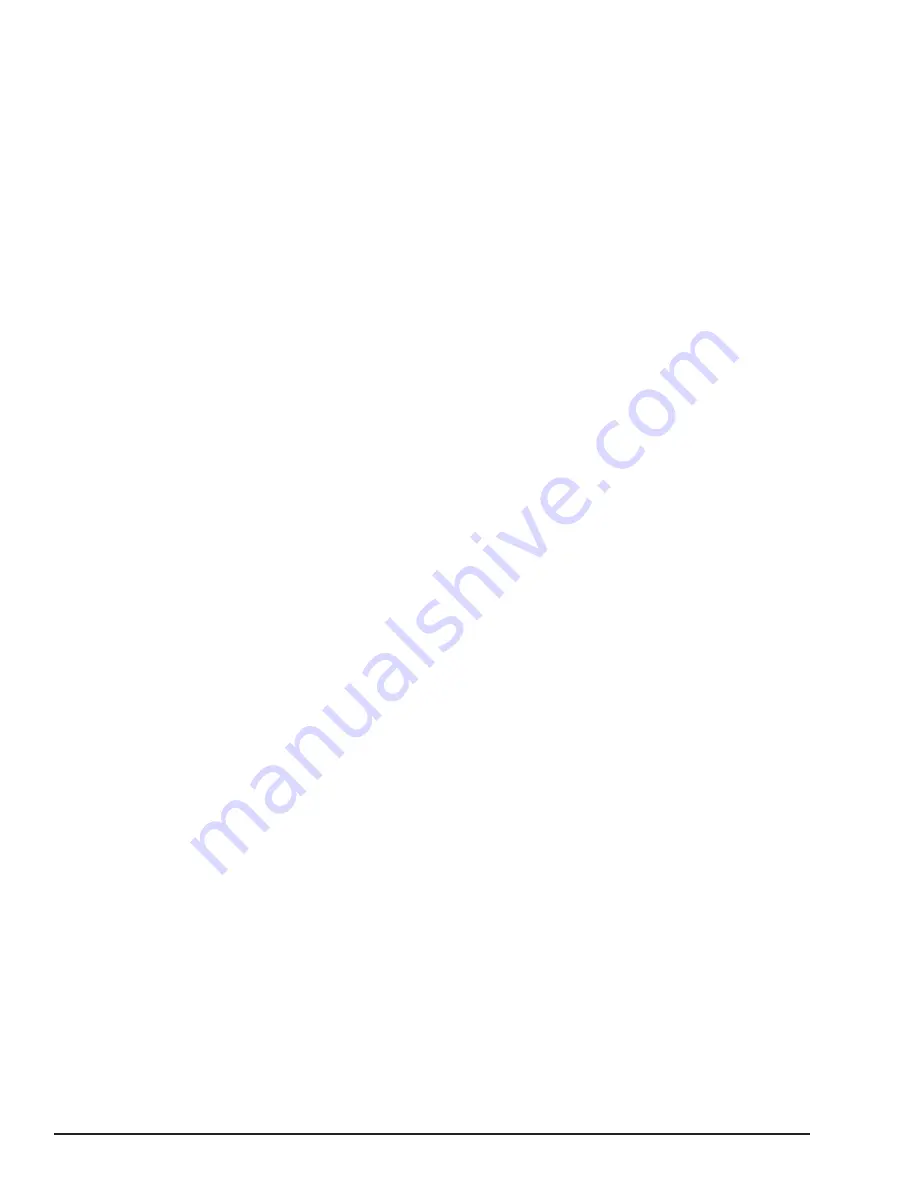
6
MAINTENANCE
Daily (or before each use)
1. Check oil level
2. Drain condensation from the air tank.
3. Check for any unusual noise or vibration.
4. Be sure all nuts and bolts are tight.
Weekly
1. Clean breather hole on Oil Breather Cap.
Monthly
1. Inspect air system for leaks by applying soapy
water to all joints. Tighten these joints if leaks
are discovered.
6 Months
(or after 250 hours of operation -
whichever comes first)
1. Change Air Compressor Oil.
Note:
Change oil more often if Air Compressor is
used near paint spraying operations or in dusty
environments.
Checking the Air Compressor Oil
1. Place Air Compressor on level surface. The oil
level should be at the red dot on the Oil Sight
Glass.
2. If oil level is low, remove Oil Breather Cap and
add enough oil to bring the oil level to the red
dot on the Oil Sight Glass.
3. Replace Oil Breather Cap before starting
compressor.
Changing the Air Compressor Oil
Note:
This compressor uses only SAE 5W-30
motor oil.
1. Remove the Drain Plug under the Oil Sight
Glass by turning the nut counter-clockwise with
wrench. (See Figure 2.)
Note:
Oil will begin to drain as Drain Plug is
loosened. Place a funnel and oil pan in place
BEFORE loosening Drain Plug.
2. Once Drain Plug is removed, tilt Air Compressor
backwards to allow all of the oil to drain out of
the crankcase.
3. Once oil is drained, replace Drain Plug and
securely tighten in place with a wrench. B
careful not to overtighten the Drain Plug, as this
could damage the rubber seal.
4. Place Air Compressor on level surface.
5. Remove the Oil Breather Cap.
6. Slowly pour the oil into the oil fill hole, until the
oil level rises to the center of the red dot on the
Oil Sight Glass.
7. Install the Oil Breather Cap into the oil fill hole.
8. Firmly hand tighten the Oil Breather Cap by
turning clockwise.
Always inspect the tool before use, and make sure
it is in good working condition. Make sure all air
vents are clear, (use compressed air to clean the
machine where possible). Check the power cable to
make sure it is intact and free from cracks, bare
wires etc. Avoid using solvents when cleaning
plastic parts. Most plastics are susceptible to
damage from the various types of commercial
solvents.
Summary of Contents for 123006
Page 1: ...2 HP 4 GALLON AIR COMPRESSOR OPERATING MANUAL Item 123006...
Page 10: ...9...
Page 11: ......