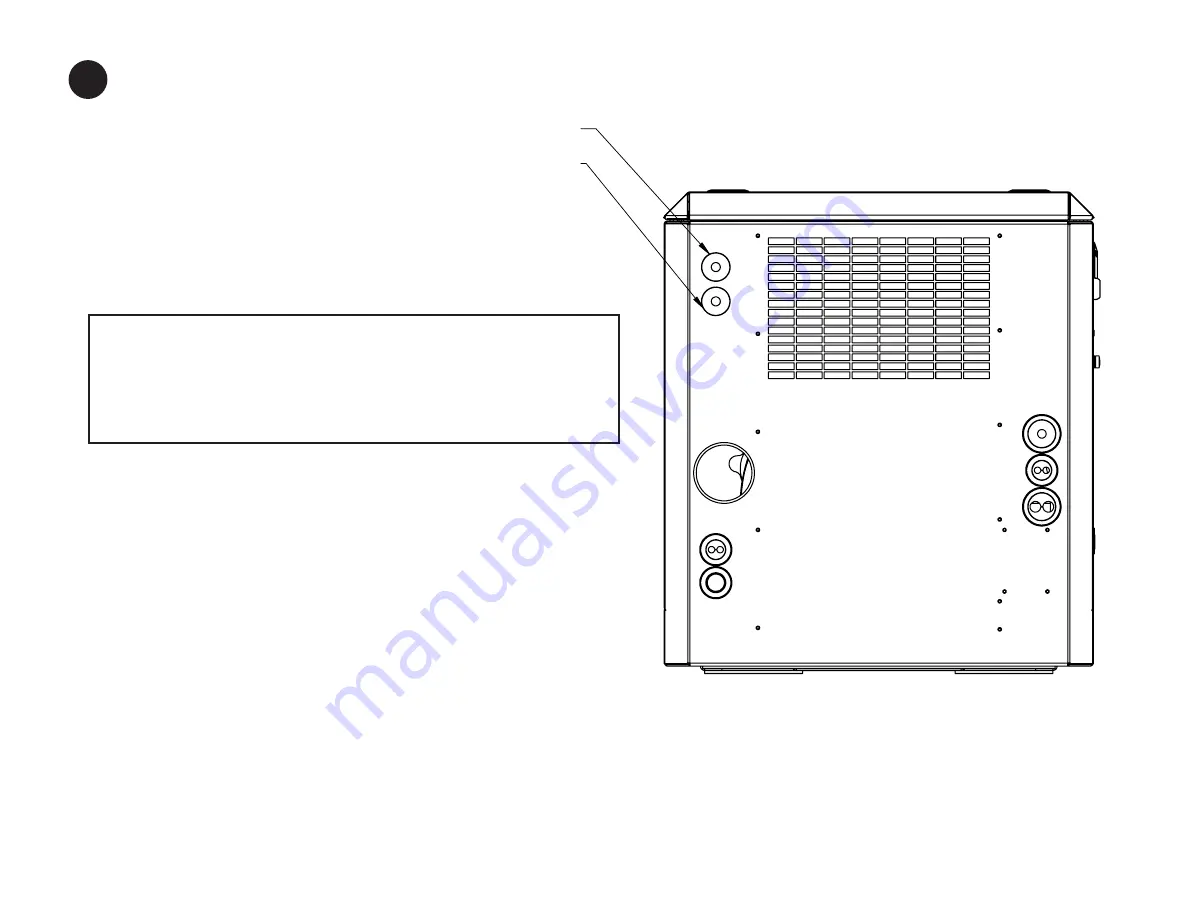
K
REAR PANEL VIEW
FROM SEA WATER PUMP OUTLET TO SIPHON BREAK
FROM SIPHON BREAK TO HEAT EXCHANGER INLET
06-78700 M864W3 GEM Page 13
13.
IF YOU HAVE CHOSEN TO INSTALL A SIPHON BREAK:
Note the two plugged penetrations in the top left corner
of the rear panel. These are the ports through which the
siphon break lines will be routed.
At this time you should refer to the plumbing diagram in the
mounting and exhaust sections of the IM1000 Installation manual.
Remove the white plastic hole plugs by pushing them out
from the inside and replace with the two rubber grommets
(ITEM#14) provided.
CAUTION. GENERATOR SETS WITH WET EXHAUST THAT ARE
INSTALLED NEAR OR BELOW THE VESSEL'S HULL WATER LINE
MUST USE A SIPHON BREAK TO PREVENT BACK FLOW OF
WATER INTO THE ENGINE. THIS BACKFLOW CAN RUIN AN
ENGINE AN POSSIBLY SINK THE VESSEL.
Disconnect the hose from the sea water pump output and
a.
the inlet to the heat exchanger. Replace this single hose
with two 3/4" ID lines, one from the sea water output and
the other to the heat exchanger inlet. These hoses must
be of adequate length to mount a siphon break a min
of 12 inches above the vessel's loaded water line.
b. Pass these lines through the two holes in the rear panel,
as indicated per the diagram.
c. For more information, see the "Exhaust" section of the
IM 1000 Installation Manual.
OUT TO VENTED LOOP
IN FROM VENTED LOOP
FOR APPLICATIONS USING A SIPHON BREAK:
Remove the white plastic hole plugs by pushing them out from the inside and
replace with the two rubber grommets (item 15) provided.
a. Disconnect the hose from the seawater pump output and from the rubber
elbow on the expansion tank. Install two lengths of 3/4” hose. The hoses
must be of adequate length to allow mounting of a siphon break, a minimum
of 12 inches above the vessel’s loaded water line.
b. Pass the seawater pump output hose through the top hole in the panel. The
hose from the expansion tank must go through the bottom hole in the panel.
c. For more information, see the “Exhaust” section of IM1000 Installation
Manual.
CAUTION: GENERATOR SETS WITH WET EXHAUST THAT ARE
INSTALLED NEAR OR BELOW THE VESSEL’S WATER LINE MUST USE
A SIPHON BREAK TO PREVENT BACKFLOW OR WATER INTO THE
ENGINE. THIS BACKFLOW CAN RUIN AN ENGINE AND POSSIBLY
SINK THE VESSEL.
14
Summary of Contents for GEM M864W3
Page 17: ......