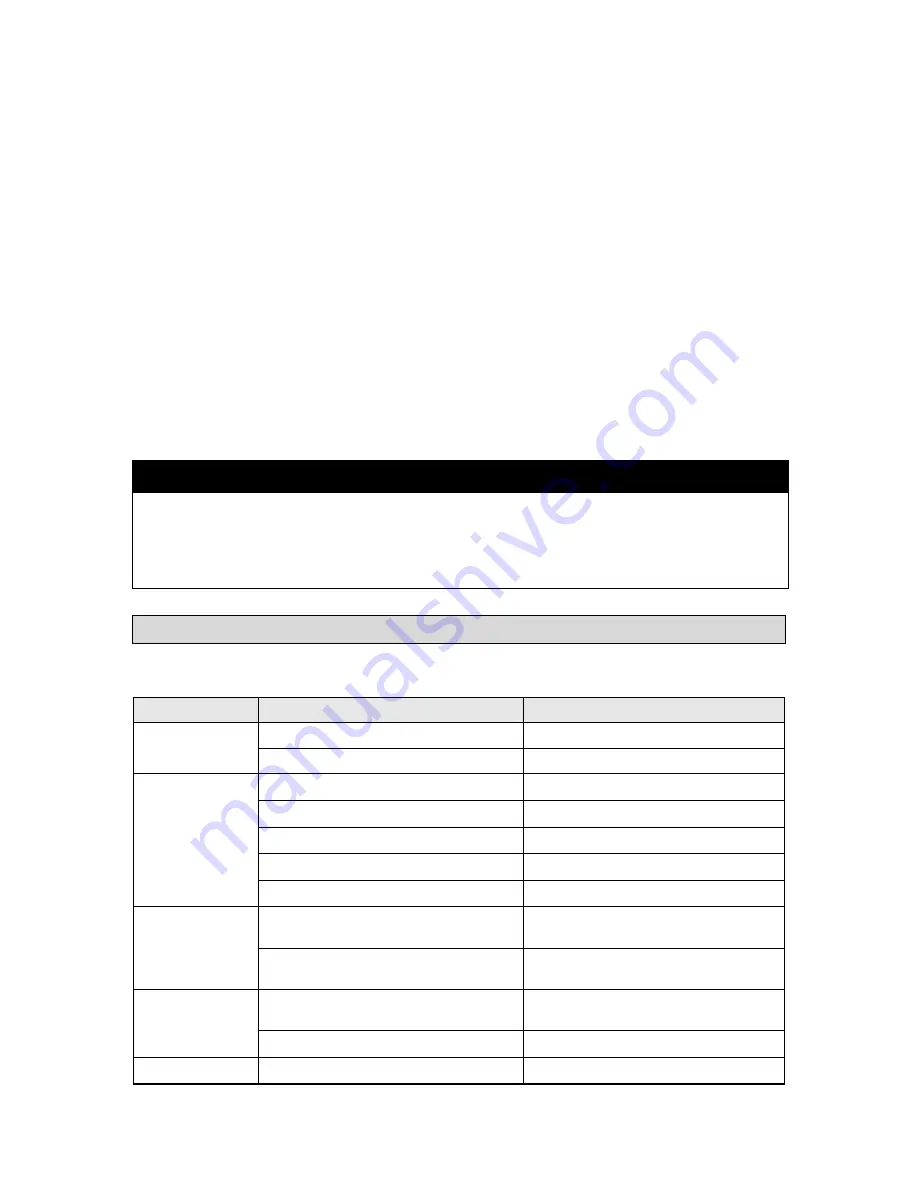
Page 18 of 24
Inspect Air Filter.
Inspect the compressor
’s air filter on a weekly basis. A dirty air filter will not allow
the air compressor to operate at full capacity.
Clean air filter if dirty and restricted air flow.
Replace the air filter every 12 months or 1000 hours.
Note: Do not operate with the air filter removed.
Keep Compressor Clean.
Do not allow air intakes to become blocked. If dust or debris accumulates
in the compressor, clean the compressor with a damp cloth or soft bristle brush.
Note: Do not spray compressor with a garden hose or pressure washer. Water may enter the
compressor and cause damage to the motor and pump.
Inspect Compressor for Air Leaks.
Inspect system for air leaks on a monthly basis. To test:
Squirt soapy water around joints during compressor operation and watch for bubbles.
Developing bubbles indicate a leak is present.
Tighten fittings, if necessary.
⚠
WARNING
If a part needs replacement, only use parts that meet the manufacturer’s part number
specifications. Replacement parts that do not meet specifications may result in a safety hazard or
poor operation of the compressor. Major service, including installation or replacement of parts,
should be made by a qualified electrical service technician.
Troubleshooting
Use the table below to troubleshoot problems before contacting service personnel or your local
dealer. If the problem continues after troubleshooting, call your local dealer for assistance.
Failure
Possible Cause
Corrective Action
Compressor won’t
start
Loose electrical connection
Check wiring connection
Fuse blew
Replace fuse
Compressor runs
continuously and
air flow lower than
normal
Malfunction in valves
Check inlet and exhaust valves
Loose tube of fittings
Tighten fittings
Restricted air filter
Clean or replace filter
Dirty or defective check valve
Remove and clean or replace check valve
Excessive air usage
Decrease air usage
Excessive moisture
in discharge
Excessive water in air tank
Drain tank, tilt tank to drain. Drain tank
more frequently.
High ambient temperature and / or humidity
Move compressor to area with less
humidity, or use airline filter.
Compressor runs
continuously
causing pressure
relief valve to open
Defect pressure switch or improper
adjustment
Check for proper adjustment and if problem
persists replace pressure switch
Defective pressure relief valve
Replace valve
Excessive noise
Loose valves
Inspect valve for damage