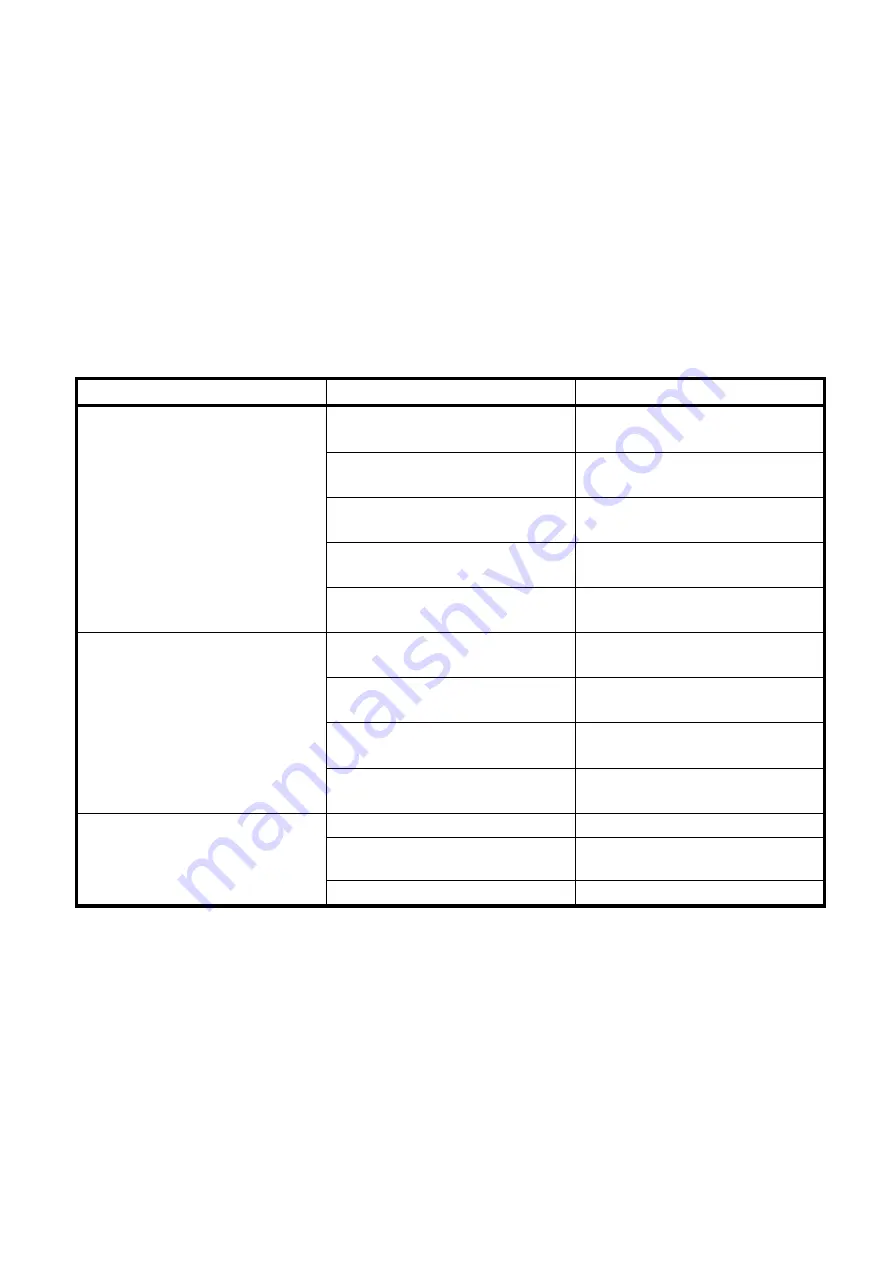
VERS. 2016.04.29
TR 232_MAN_EN
25
7
FAULTS: CAUSES AND CURES
7.1
Fault-finding procedures
Should any fault occur during the use of the machine, turn it off, and isolate it from the electrical
supply. Any works dealing with the electrical system or supply of the machine can only be carried
out by a qualified electrician.
7.2
Trouble-shooting guide
Trouble
Possible source
Resolution
Motor is not running
No electricity
Check the electrical supply
(fuse for example)
Connection cable section too
small
Change connection cable
Defective connection cable
Change connection cable
Defective switch
CAUTION : can only be solved
by qualified electrician
Defective motor
Change motor or contact motor
manufacturer
Motor stops during the cutting,
but can be restarted after a
short period (overload
protection)
Cutting feed speed too quick
Cut slowly
Blade is blunt or glazed
Sharpen the blade in
calcareous stone
Defective blade
Change blade
Wrong blade specification for
the application
Change blade
No water on the blade
Not enough water in the pan
Refill the water pan
Water supply system is blocked
up
Clean water supply system
Water pump is not working
Change the pump