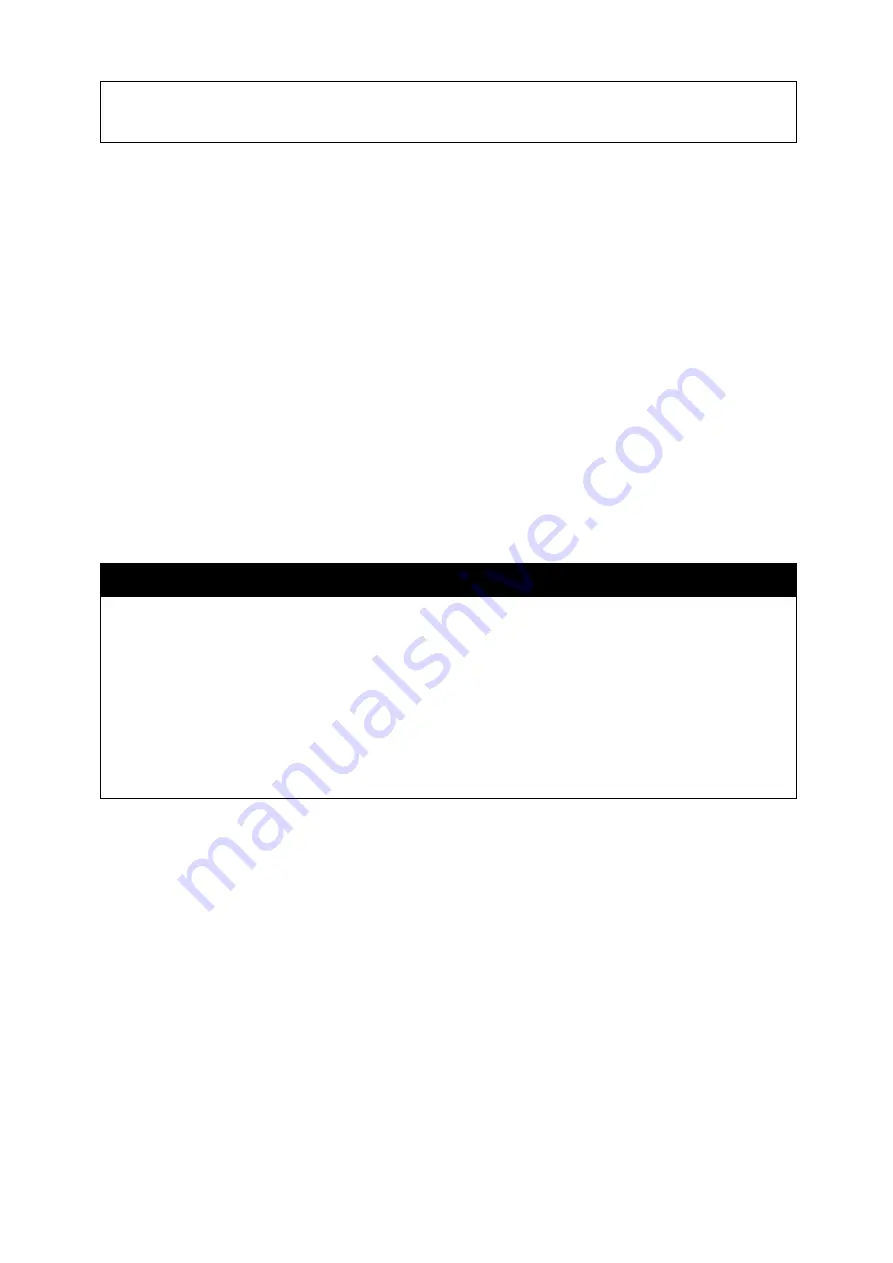
Page 27 of 35
•
Never drain gasoline near an open flame or where a spark may ignite gasoline fumes.
•
Never smoke while handling fuel.
1. Park the machine on a level surface to assure fuel tank drains completely.
2. Lower the loader arms and turn the ignition key to the OFF position to stop the engine. Remove
the ignition key from the key switch.
3. Loosen the hose clamp at inlet side of the fuel filter and slide it up the fuel line away from the fuel
filter.
4. Pull the fuel line off the fuel filter, open the fuel valve, and allow the gasoline to drain into an
approved fuel container.
5. Loosen the clamp on the fuel line inlet to the fuel shut-off valve and pull the fuel line off of the
valve fitting. Remove the fuel tank from the machine by unscrewing the nut at the clamp at the top
of the tank. Remove the tank and drain completely into an approved fuel container by tipping the
tank upside down. Clamp the fuel line and flush the tank by pouring a small amount of clean fuel
into the tank and swirling around to loosen any sediment from the bottom of the tank.
6. Reverse the procedure to reinstall the clean tank.
Note:
Now is the best time to install a new fuel filter because the fuel tank is clean and empty.
7. Install the fuel line onto the fuel filter. Slide the hose clamp close to the fuel filter to secure the fuel
line.
Hydraulic System Maintenance
⚠
WARNING
•
Inspect hydraulic system regularly for leaks.
•
Hydraulic fluid escaping through even a pin-size hole opening can puncture skin and cause blood
poisoning.
•
Wear proper hand and eye protection when searching for leaks. Never check for leaks with your
hand while system is pressurized. Use wood or cardboard instead of hands
•
Relieve pressure on hydraulic system before servicing or disconnecting hoses.
•
Seek medical attention immediately if injured by escaping fluid.