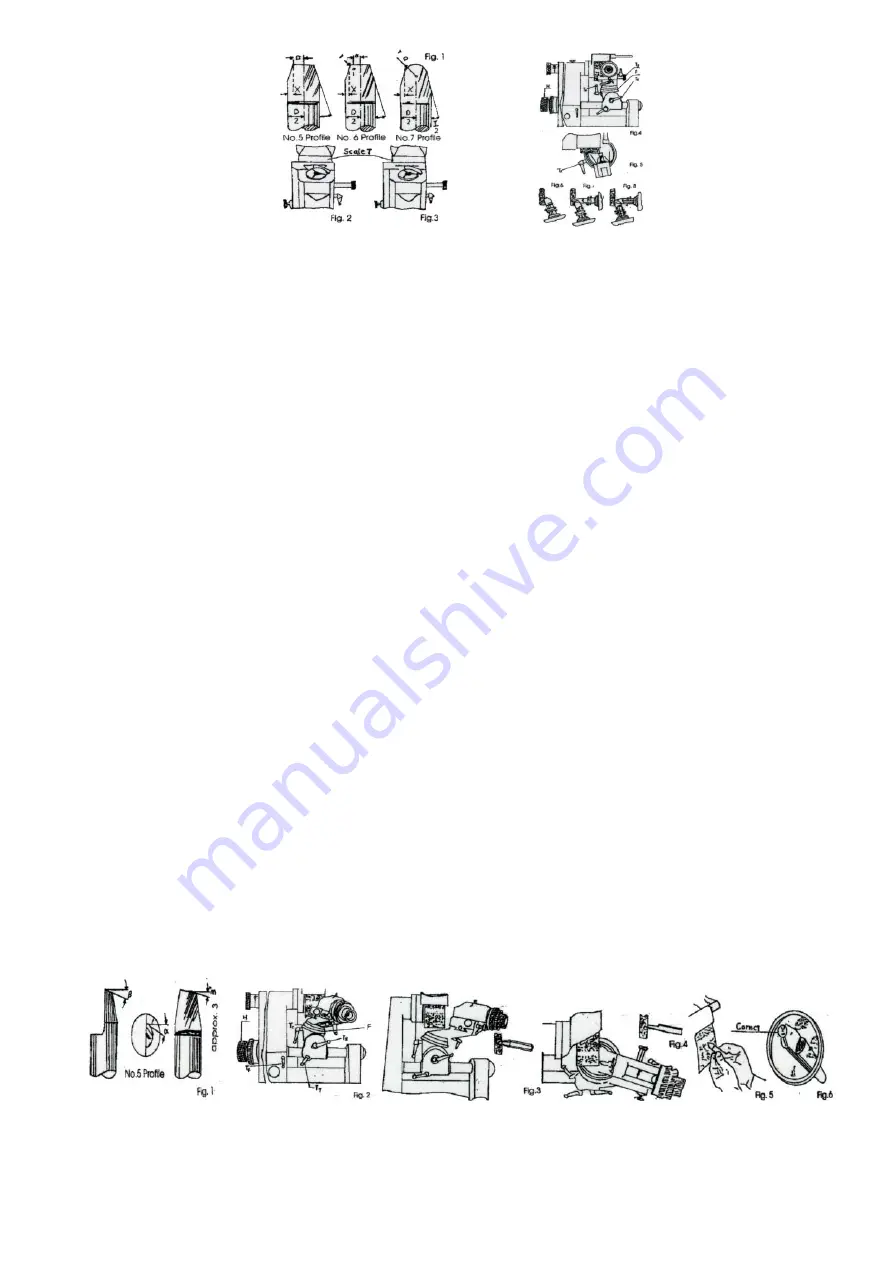
Grinding Tapered Cutters-
Circular Grinding of side and End Cutting Edges
Tapered cutters can be ground to size in the machine without the use of any measuring instrument, except for the scales provided on
the machine. For circular grinding operations on profiled cutters follow this procedure:
Setup Operations
1.
Align cutter lip by means of gauge ’C; grip cutter in position; return gauge C.
2.
Draw index pin P out of slot hole to enable collets bearing to be rotated through 360
o
Release clamping levers T2, T3, T6. Set
scale S2 and F at zero. Tighten clamping levers T4, T2, T3, T6 see Fig.
3.
Release clamping lever T7;bring cutter diameter into light contact with grinding wheel; tighten clamping lever T7,taking care to
keep index mark of vertical swivel mount aligned with tubular guide; release clamping lever T4,see Fig.4.
4.
A.N0.5 profile 9Fig. 1 and 2): Release clamping lever T1; rotate knurled knob S4 to shift cross slide to the right by one-half of
dialog the taper (‘Fig.1). For this purpose use cross slide venire scale T. Tighten clamping lever T1.
B.No.6 profile (Fig. and 2): Release clamping lever T1; rotate knurled knob S4 to shift cross slide to the right by the desires
amounts” (use cross slide venire scale T). Tighten clamping lever T1.
C.No.7 profile (Fig. 1 and 3): Set cross slide venire scale at zero.
5.
A.No.5 and 7 profiles: Rotate fine adjustment screw H to bring cutter diameter into light contact with grinding wheel: again
rotate screw H to shift cutter to the left by amount x = D/2-a. To facilitate this setting operation, set scale drum of screw H at
zero without disturbing the setting of the screw (see Fig.4).
b.No.6 profile :Rotate screw H to bring cutter diameter into light contact with grinding wheel; again rotate screw H to shift cutter
to left by the amount x=D/2-(a+r). To facilitate this setting operation, set scale drum of screw H at zero without disturbing the
setting of the screw (see Fig.4).
6.
Release clamping lever T3; ratate swivel arm through 90
o
; release clamping lever T5; rotate index head slide micrometer
screw S to advance end face of cutter towards grinding wheel. Wheel tapered cutters are to be retargeted; the length of the
cutting edge at the end of the cutter should be made greater than the small diameter of the tapered portion.
7.
Release clamping lever T6; hold index drum F against its stop and counting from the zero position, set swivel arm at the
desired taper angle; tighten clamping lever T3 and T6, sgg Fig.6.
8.
A.No.5 profile: Slowly return stop screw Gad and continuously rate the collets bearing through 360
o
to advance the cutter
past the grinding wheel. Prior to the circular grinding operation ratite fine adjustment screw H to shift the cutter to the right; the
advance the cutter towards the wheel by small increment unit the desired size has been obtained (see Fig.6).
b.No.6 and 7 profiles: Release clamping lever T3; first slowly return stop screw G, then slowly swing the swivel arm while
continuously rotating the collets bearing through 360
o
to move the cutter past the wheel and thus to circular grinding
operation ratite fine adjustment screw H to shift the cutter to the right; then advance the cutter towards the wheel by small
increments until the desired size has been obtained (see Fig.7 & 8).
Circular Tapered Cutters-
Grinding the Back Angle of Side and End Cutting Edges
6