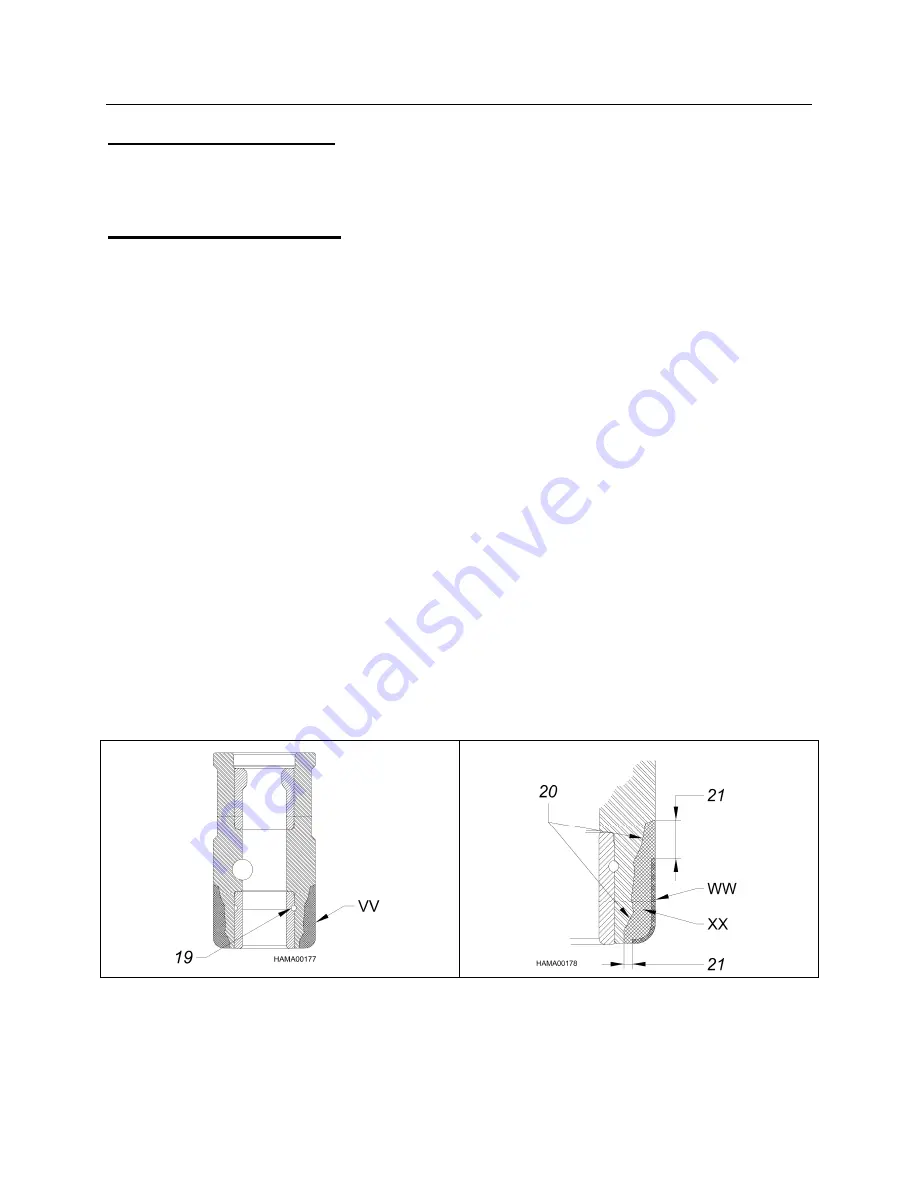
-
101
-
TOOL HOLDER
REPAIR OF EXTERIOR
When the hammer has been used for a long period of time, or operated with penetration
of the tool holder into the material being broken, the exterior of the tool holder may
become worn.
REBUILD PROCEDURE
1. Underlayment
- Underlayment weld is necessary to build up the base material or
over existing hardface weld. NOTE: You cannot hardface directly over old
hardfacing.
Welding Rod: Airco Austex 361, Cronatron 7770, Eutectic 3205, Postalloy 205,
Stoody 2110 or equal. In Canada; NCH Canada, Inc. Hi-Pact #194 or equal.
Dry welding rod at 300°F +.
Pre-heat the tool holder weld area to 150°F and maintain this temperature during the
welding operation. It is very important to maintain this temperature in cold
environments.
Adjust weld current to rod manufacturer’s specification.
Peen each layer.
Cool slowly. Cover weld in cold environments.
2. Hardface
- Hardface can only be applied over base material or underlayment weld.
Never hardface existing hardface.
Welding Rod: Airco Tubecraft 1A, Cronatron 7355, Eutectic N6006, Postalloy 214,
Stoody 31 or equal. In Canada; NCH Canada, Inc. Wear-X #176 or equal.
Dry welding rod at 300°F +.
Pre-heat the tool holder weld area to 350°F and maintain this temperature during the
welding operation. It is very important to maintain this temperature in cold
environments.
Adjust weld current to rod manufacturer’s specification.
Peen each layer. Do not exceed 2-3 layers of hardface.
Cool slowly. Cover weld in cold environments.
19
– RETAINING PIN BORE
Leave sufficient clearance around the tool bushing
retaining pin bore for removal or assembly. If
necessary, a short length of 1 inch pipe can be
welded in position over the hole to provide
clearance. Grind flush after welding.
VV – REPAIR WELDMENT (see detail)
20
– GRIND SMOOTH
21
– GRIND SMOOTH (no overlapping)
WW – HARDFACING
XX – UNDERLYING WELD