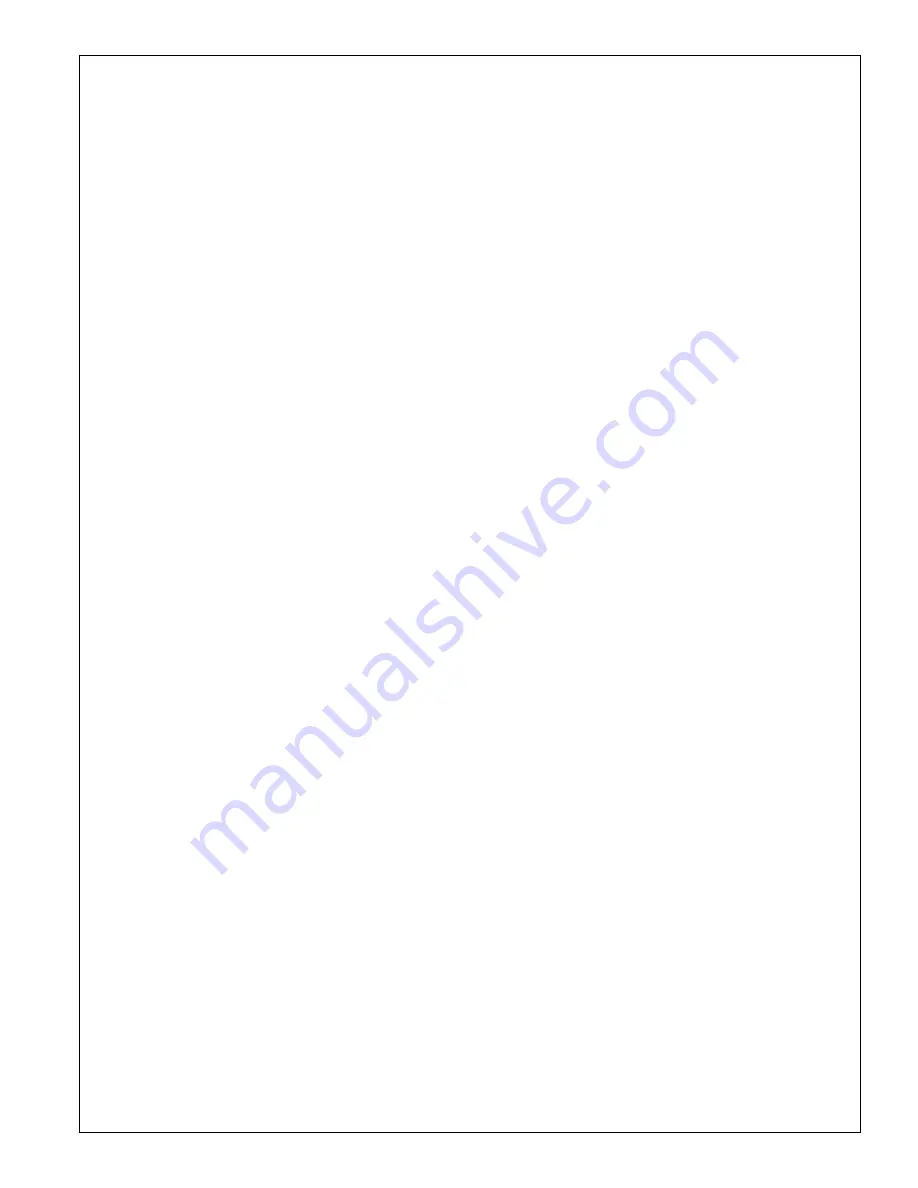
7
MACHINE MAINTENANCE
Routine maintenance is critical to ensure proper
machine operation and cleaning performance.
Perform all maintenance procedures as follows.
Always turn OFF all machine switches before
performing any maintenance.
Daily Maintenance
Battery Charging
The master power switch and all other switches
must be turned OFF
.
•
You must recharge the batteries at the end of
every work shift or when the battery meter
indicates the “recharge” during the work shift.
•
Connect the battery charger plug (red) to the
machine's charging plug.
•
Connect the battery charger power cord into a
grounded A.C. outlet of the proper voltage.
•
After a few seconds the amp meter (or light) will
indicate the battery charger is operating.
•
When the recharge cycle is complete, the battery
charger will turn off automatically. The amp meter
will register “0” or the light will be off.
•
If the battery charger will not start operating, check
the charging plug connections, the battery cable
connections and the battery voltage.
•
If the batteries have been discharged (used) too
deeply, the battery charger will not start. Consult
your local authorized NSS distributor or service
center for assistance.
Battery Electrolyte (Liquid) Level
Inspect the electrolyte level of at least one cell in
each battery before charging. The liquid must be
visible above the internal plates. Do not charge the
batteries if the liquid is below the plates.
•
Add only water to the cell of a battery to adjust the
liquid level. Before charging, add only enough
water to cover the top of the internal plates. After
charging add only enough water to bring the level
to the bottom of the fill tube.
•
Do Not overfill the battery liquid level, this will
cause electrolyte (acid) spill. Spilled electrolyte
(acid) can cause machine damage and personal
injury. Clean up and dispose of all spills
immediately. See the battery-warning sheet for
more details.
Solution and Recovery Tanks
•
Empty all liquids from both solution and
recovery
tanks.
•
Rinse both tanks with clean water to prevent
chemical residue build-up. Empty both tanks.
•
Remove any residue from screen and float ball to
ensure proper operation. Replace float assembly
on tube in recovery tank.
•
Leave recovery tank clear lid open to allow tank to
air dry and prevent odors.
Pad Drivers or Brushes
•
Remove both pad drivers (or brushes) from machine.
•
Rinse with clean water to prevent chemical residue
build-up.
•
Inspect for wear or damage. Repair or replace as
needed.
•
Allow to air dry on a shelf or rack.
Squeegee Assembly
•
Remove squeegee assembly from machine.
•
Rinse with clean water to prevent chemical residue
build-up.
•
Inspect for wear or damage. Repair or replace as
needed.
•
Allow to air dry on a shelf or rack.
Weekly Maintenance
•
Verify all daily maintenance has been performed.
•
Inspect battery liquid level, adjust to proper level as
needed.
•
Check all battery terminal and cable connections.
Tighten as needed.
•
Clean any corrosion from battery terminals and
cables.
•
Check solution flow to pad drivers / brushes.
Remove, inspect and clean the solution filter
assembly.
•
Flush clean solution tank and hoses with a mixture of
8 oz. (250ml.) white vinegar to one-gallon (4 liter)
warm water.
•
Repair or replace any worn or damaged components
as needed.
Monthly Maintenance
•
Verify all daily and weekly maintenance has been
performed.
•
Inspect vacuum motor exhaust filter behind metal
plate at rear of battery compartment. Clean or
replace as necessary.
•
Grease the caster axle and swivel bearing. Use a
hand held grease gun and a high grade of water
resistant lithium base grease.
•
Inspect all mechanical linkages, pivot points and ball
joints for freedom of movement. Use a penetrating
spray lubricant that is water resistant. Do not use WD
40 lubricant.
•
Check return springs of the twist grip (deadman)
handles. If they appear weak or do not return twist
grips to the neutral position, replace both springs.
•
Inspect all fasteners (bolts, screws, nuts) at
mechanical linkages, pivot points and ball joints for
tightness. Tighten as needed.
•
Repair or replace any worn or damaged components.
https://harrissupplyind.com - To Order Parts Call 608-268-8080