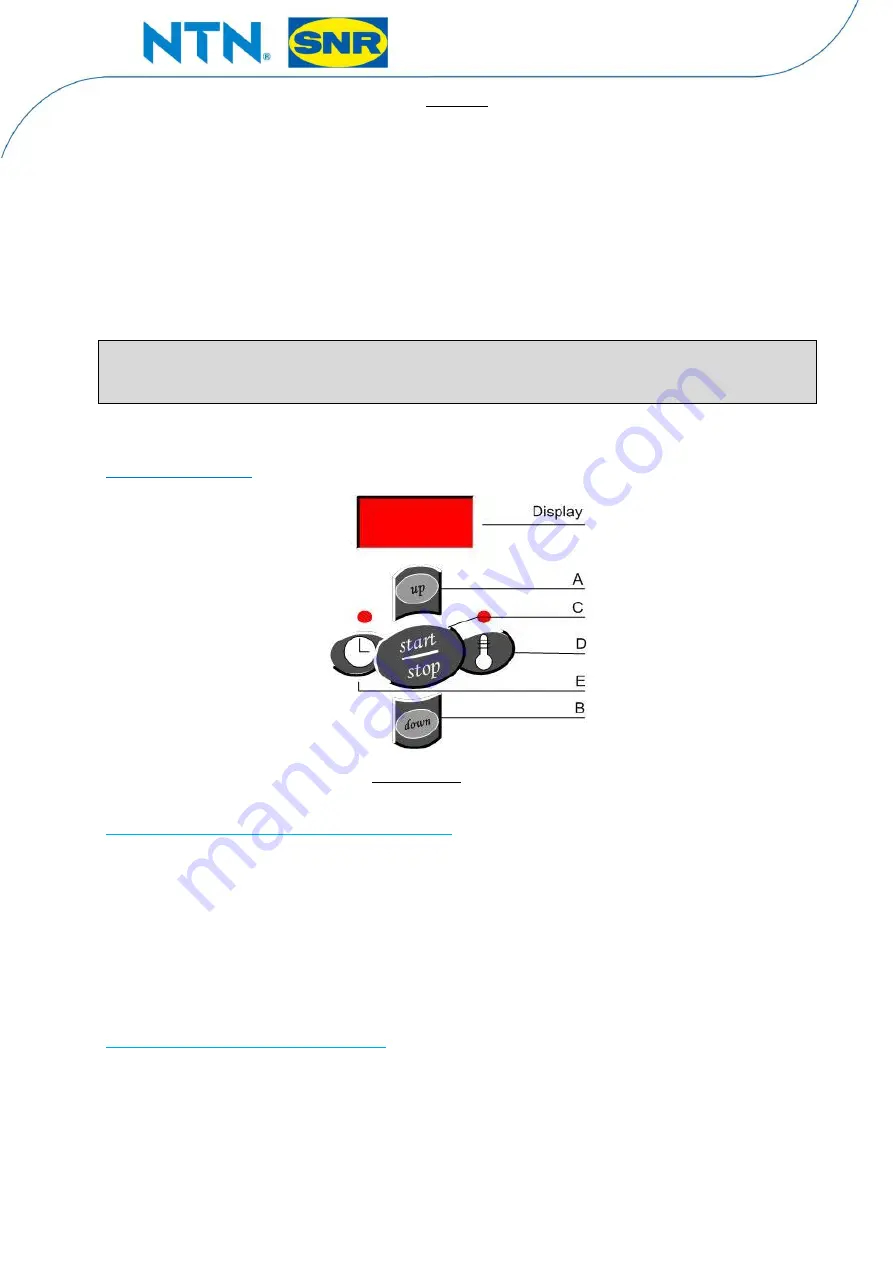
8
Sketches
Always use magnetic temperature probe (hereafter referred to as the 'probe') for heating in the
Temperature Mode.
The probe is suitable for operation up to a maximum temperature of 240ºC (484°F)
As a safety feature, the connection between magnet and probe will break above the maximum
temperature. If this occurs when operating in the Temperature Mode, the machine will turn itself off
since the probe will fail to register any increase in the temperature over a set period of time.
A probe fixed to a clamp is also available when heating non-magnetic work pieces.
Ensure that the area where the probe is located is completely clean.
Connect the probe by inserting the plug into the socket at the side of the heater,
watch out for + -!
CAUTION:
Treat the probe with care. It is a valuable part of the heater and can easily be broken through
careless handling. After use, we suggest that it is placed on the side of the vertical pole.
6. OPERATIONS:
Control panel
Heating with temperature pre-selection function:
When heater is switched on the display will show: 110°C (230°F)
With A and B you can decrease the temperature to 0°C (32°F) and increase to 240°C. (484°F)
Select temperature and press "start/stop” to start the heating process. The heater will first count down for
30 seconds; this makes it able for the user to step away from the heater 1 meter (
38”), start heater with
remote control. The display will now show progress of heating cycle. Once pre-selected temperature is
reached the acoustic signal will sound and the display will flash. Press
“stop on the remote control and
place probe on one of the poles, remove work piece.
Heating time versus temperature ramp:
This is specially developed for the heating of gears and bearings with a small clearance. The user
can set the temperature and time; the heater will heat the part exactly to the preset temperature in the
preset time. The major advantage this provides is the temperature differential between the internal and
external component material remains low thus reducing the potential for material stress accumulation and
subsequent potential distortional damage.
Summary of Contents for Safe Therm 1200
Page 13: ...12 8 ELECTRICAL DRAWING Safe Therm 700 Safe Therm 1200...
Page 14: ...13...