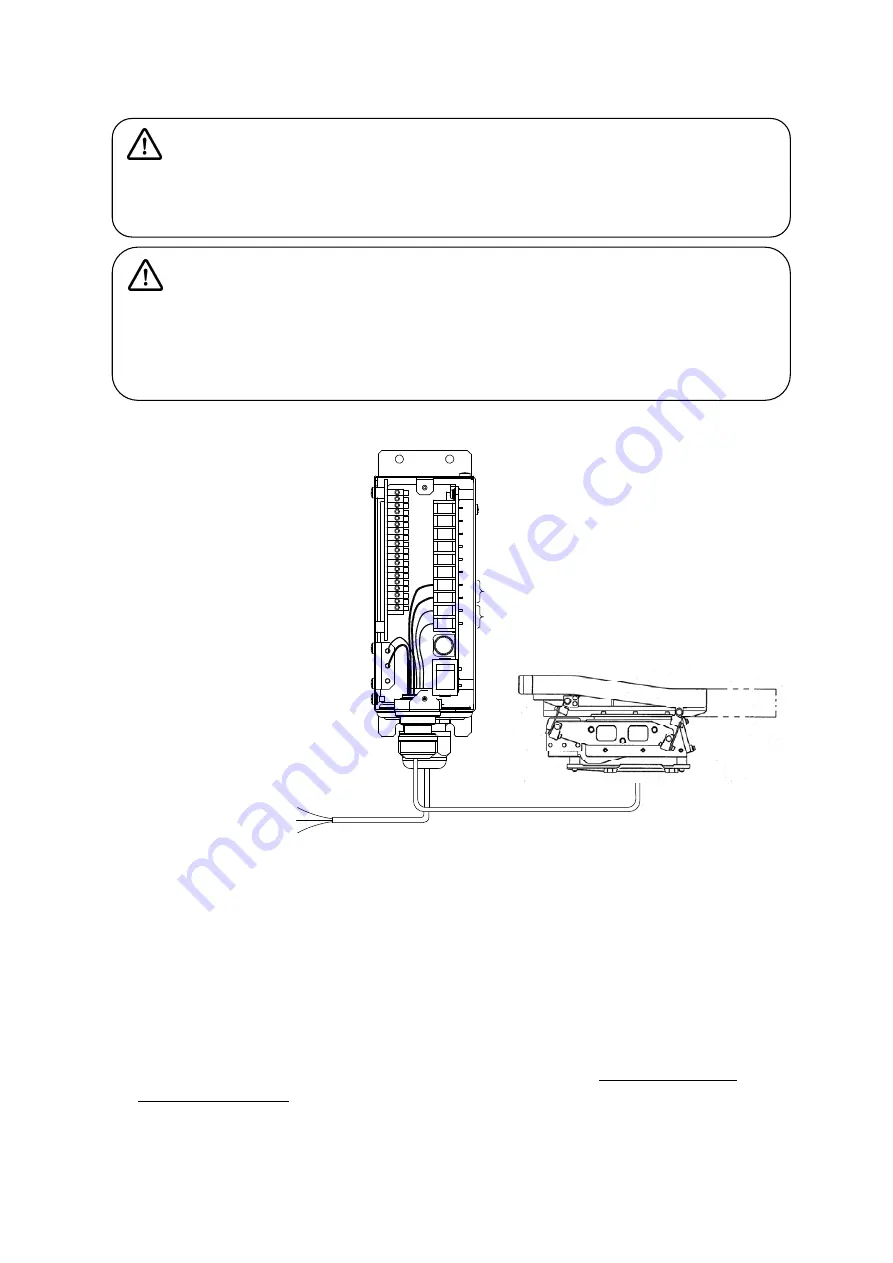
- 9 -
7.
Wiring and Operating Methods
Controller (K-ECF25 as example)
*1 Power cable to the single-phase AC power source (feeder body specified voltage).
In the case of three-phase power source, use two phases out of three. Do not use the remaining one
phase.
(1) Remove transportation fixtures (Red tag) fixing the feeder body and the chute as well as
transportation members, if attached.
(2) Connect power supply. (See the operation manual of the controller for connection in detail.)
(3) Turn the speed adjusting knob of the controller counterclockwise to set the graduation at "0".
(Make sure that the feeder body is free and in no contact with something around.)
(4) Turn on the power switch of the controller. (Confirm lighting of LED on the operation panel.)
(5) Turn the speed adjusting knob of the controller slowly clockwise to set the graduation at a workpiece
speed that matches with supply capacity. Operate this machine under the maximum acceptable
amplitude of leaf spring in the item 8 in order to prevent breakage of leaf spring.
CAUTION
When setting F-V curve and other data for a controller of variable frequency
controllers, make settings conform to the specification and power conditions of
the body. Wrong setting may result in accidents such as burning of the magnet.
For setting for controllers, refer to the Controller Operation Manual.
WARNING
Ensure that the supply voltage is as shown on the machine nameplate (seal
bearing the type, power supply and manufacturer’s serial No.) of the vibrator body.
Be sure to connect the grounding wire of the power source.
L
N
1
2
C2
EM
C1
AL1
Y1C
Y1A
・
It is connected to the single phase AC power.
Please connect it to AC100-115V or
AC200-230V according to the voltage of the
main vibration body.
・
The frequency is both for 50 and 60Hz.
・
Connect green or green/ yellow to the earth.
Power source
Load(Parts feeder)
Green
Red
White
Power cable
Load cable
*
1