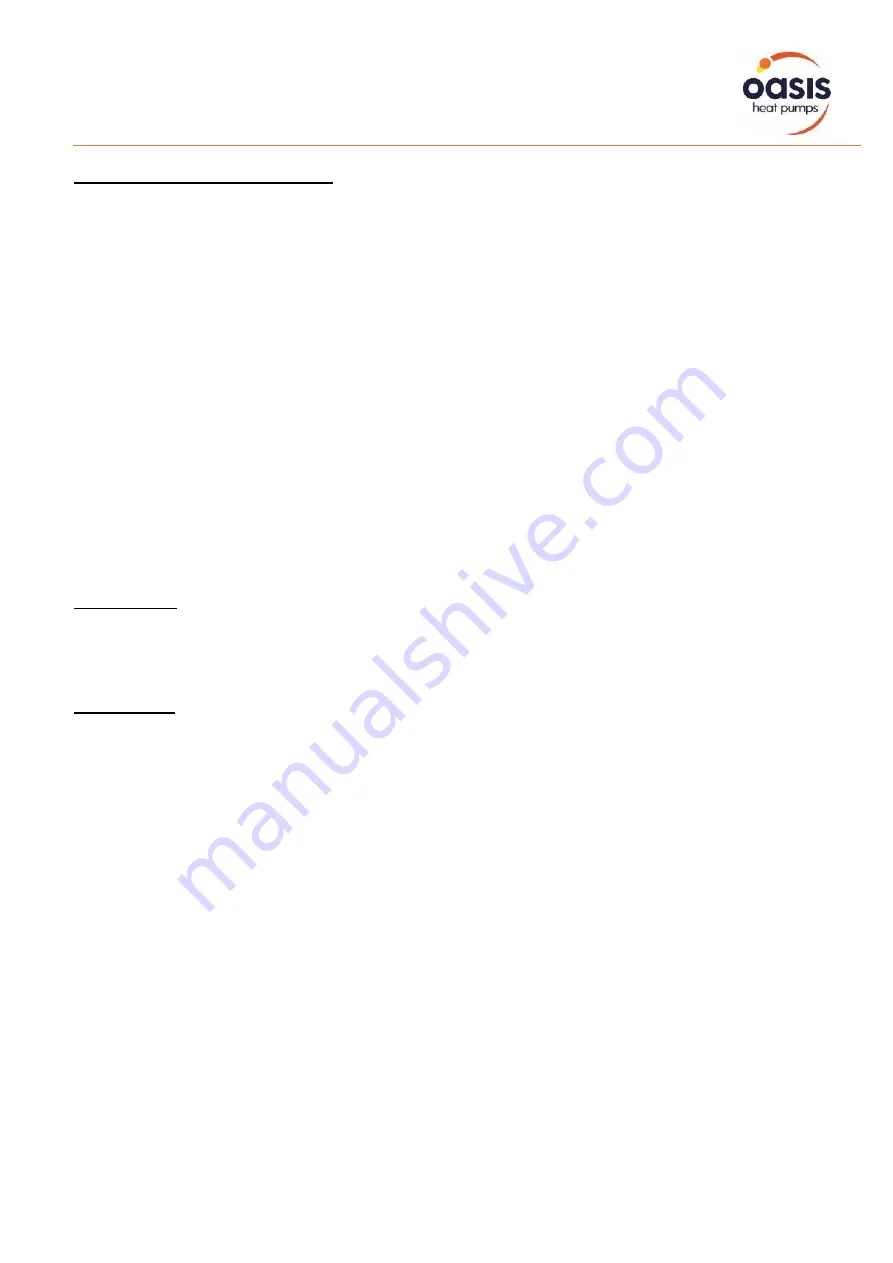
Page 36 of 43
Maintenance & Information
REMOVAL AND EVACUATION
When breaking into the refrigerant circuit to make repairs or for any other purpose conventional
procedures shall be used. However, it is important that best practice is followed since flammability is a
consideration. The following procedure shall be adhered to:
•
Remove refrigerant;
•
Purge the circuit with inert gas;
•
Evacuate;
•
Purge again with inert gas;
•
Open the circuit by cutting or brazing.
The refrigerant charge shall be recovered into the correct recovery cylinders. The system shall be
"flushed" with OFN to render the unit safe. This process may need to be repeated several times.
Compressed air or oxygen shall not be used for this task.
Flushing shall be achieved by breaking the vacuum in the system with OFN and continuing to fill until
the working pressure is achieved, then venting to atmosphere, and finally pulling down to a vacuum.
This process shall be repeated until no refrigerant is within the system. When the final OFN charge is
used, the system shall be vented down to atmospheric pressure to enable work to take place. This
operation is absolutely vital if brazing operations on the pipe-work are to take place.
Ensure that the outlet for the vacuum pump is not close to any ignition sources and there is ventilation
available.
LABELLING
Equipment shall be labelled stating that it has been de-commissioned and emptied of refrigerant. The
label shall be dated and signed. Ensure that there are labels on the equipment stating the equipment
contains flammable refrigerant.
RECOVERY
When removing refrigerant from a system, either for servicing or decommissioning, it is recommended
good practice that all refrigerants are removed safely.
When transferring refrigerant into cylinders, ensure that only appropriate refrigerant recovery cylinders
are employed. Ensure that the correct number of cylinders for holding the total system charge is
available. All cylinders to be used are designated for the recovered refrigerant and labelled for that
refrigerant (i.e. special cylinders for the recovery of refrigerant). Cylinders shall be complete with
pressure relief valve and associated shut- off valves in good working order. Empty recovery cylinders
are evacuated and, if possible, cooled before recovery occurs.
The recovery equipment shall be in good working order with a set of instructions concerning the
equipment that is at hand and shall be suitable for the recovery of flammable refrigerants. In addition,
a set of calibrated weighing scales shall be available and in good working order. Hoses shall be
complete with leak-free disconnect couplings and in good condition. Before using the recovery machine,
check that it is in satisfactory working order, has been properly maintained and that any associated
electrical components are sealed to prevent ignition in the event of a refrigerant release. Consult
manufacturer if in doubt.
The recovered refrigerant shall be returned to the refrigerant supplier in the correct recovery cylinder,
and the relevant Waste Transfer Note arranged. Do not mix refrigerants in recovery units and especially
not in cylinders.
If compressors or compressor oils are to be removed, ensure that they have been evacuated to an
acceptable level to make certain that flammable refrigerant does not remain within the lubricant. The
evacuation process shall be carried out prior to returning the compressor to the suppliers. Only electric
heating to the compressor body shall be employed to accelerate this process. When oil is drained from
a system, it shall be carried out safely.
Summary of Contents for RAPID PRO RP14
Page 1: ......
Page 30: ...Page 29 of 43 Troubleshooting WIRING DIAGRAM 1...
Page 31: ...Page 30 of 43 Troubleshooting WIRING DIAGRAM 2...
Page 32: ...Page 31 of 43 Troubleshooting WIRING DIAGRAM 3...
Page 43: ...Page 42 of 43 Notes...