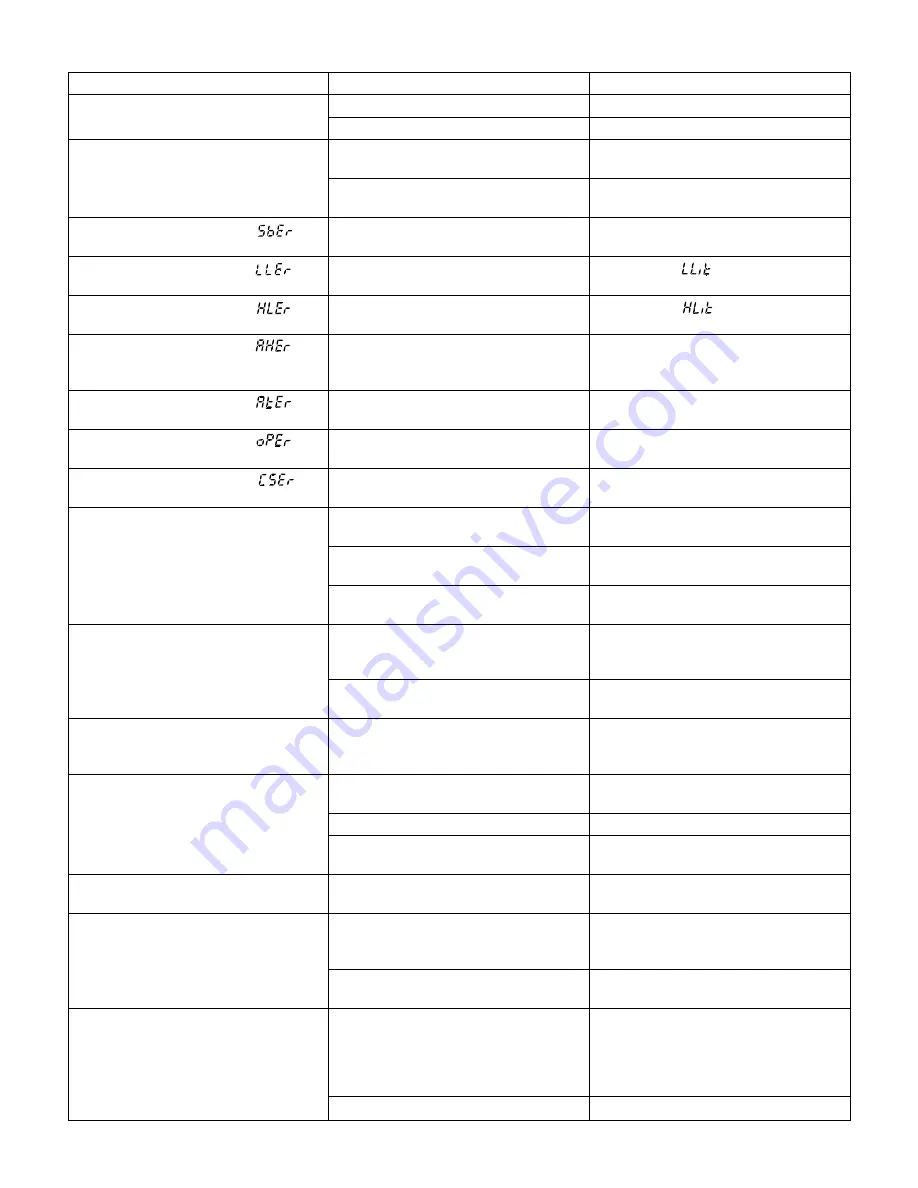
Table 7.1 Troubleshooting
Symptom
1.) LED’s will not light.
2.) Some segments of the display or
LED lamps not lit or lit erroneous-
ly.
3.) Process Display shows:
4.) Process Display shows:
5.) Process Display shows:
6.) Process Display shows:
7.) Process Display shows:
8.) Process Display shows:
9.) Process Display shows:
10.) Display Unstable
11.) Considerable error in tempera-
ture indication.
12.) Display goes in reverse direction
(counts down scale as process
warms).
13.) No heat or output
14.) Heat or output stays on but indi-
cator reads normal.
15.) Control abnormal or operation
incorrect.
16.) Display blinks, entered values
change by themselves.
Probable Cause(s)
—No power to instrument.
—Power supply defective.
—LED display or LED Lamp defec-
tive.
—Related LED driver defective.
—Sensor break error.
—Process value beyond the low
range setpoint.
—Process value beyond the high
range setpoint.
—Analog hybrid module damage.
—Incorrect operation of auto tune
procedure. Prop. Band set to 0.
—Manual mode is not allowable for
an ON-OFF control system.
—Check sum error, values in memory
may have changed accidentally.
—Analog portion or A-D converter
defective.
—Thermocouple, RTD or sensor
defective.
—Intermittent connection of sensor
wiring
—Wrong sensor or thermocouple
type. Wrong input mode selected.
—Analog portion A-D converter
defective.
—Reversed input wiring of sensor.
—No heater power (output), incorrect
output device used.
—Output device defective.
—Open fuse outside of the instru-
ment.
—Output device shorted, or power
service shorted.
—CPU or EEPROM (non-volative
memory) defective. Key switch
defective.
—Operation of control incorrect.
—Electromagnetic interference (EMI),
or Radio Frequency Interface (RFI).
—EEPROM defective.
Solution(s)
—Check power line connections.
—Replace power supply board.
—Replace LED display or LED lamp.
—Replace the related transistor or IC
chip.
—Replace RTD or sensor.
—Use manual mode operation.
—Re-adjust
value.
—Re-adjust
value.
—Replace module. Check for outside
source of damage such as tran-
sient voltage spikes.
—Repeat procedure. Increase Prop.
Band to a number larger than 0.
—Increase proportional band.
—Check and reconfigure the control
parameters.
—Replace related components or
board.
—Check thermocouple, RTD or sen-
sor.
—Check sensor wiring connections.
—Check sensor or thermocouple type
and if proper input mode was
selected.
—Replace related components or
board.
—Check and correct.
—Check output wiring and output
device.
—Replace output device.
—Replace output fuse.
—Check and replace.
—Check and replace.
—Read the operation procedure care-
fully.
—Suppress arcing contacts in system
to eliminate high voltage spike
sources. Separate sensor and con-
troller wiring from “dirty” power
lines, ground heaters.
—Replace EEPROM.