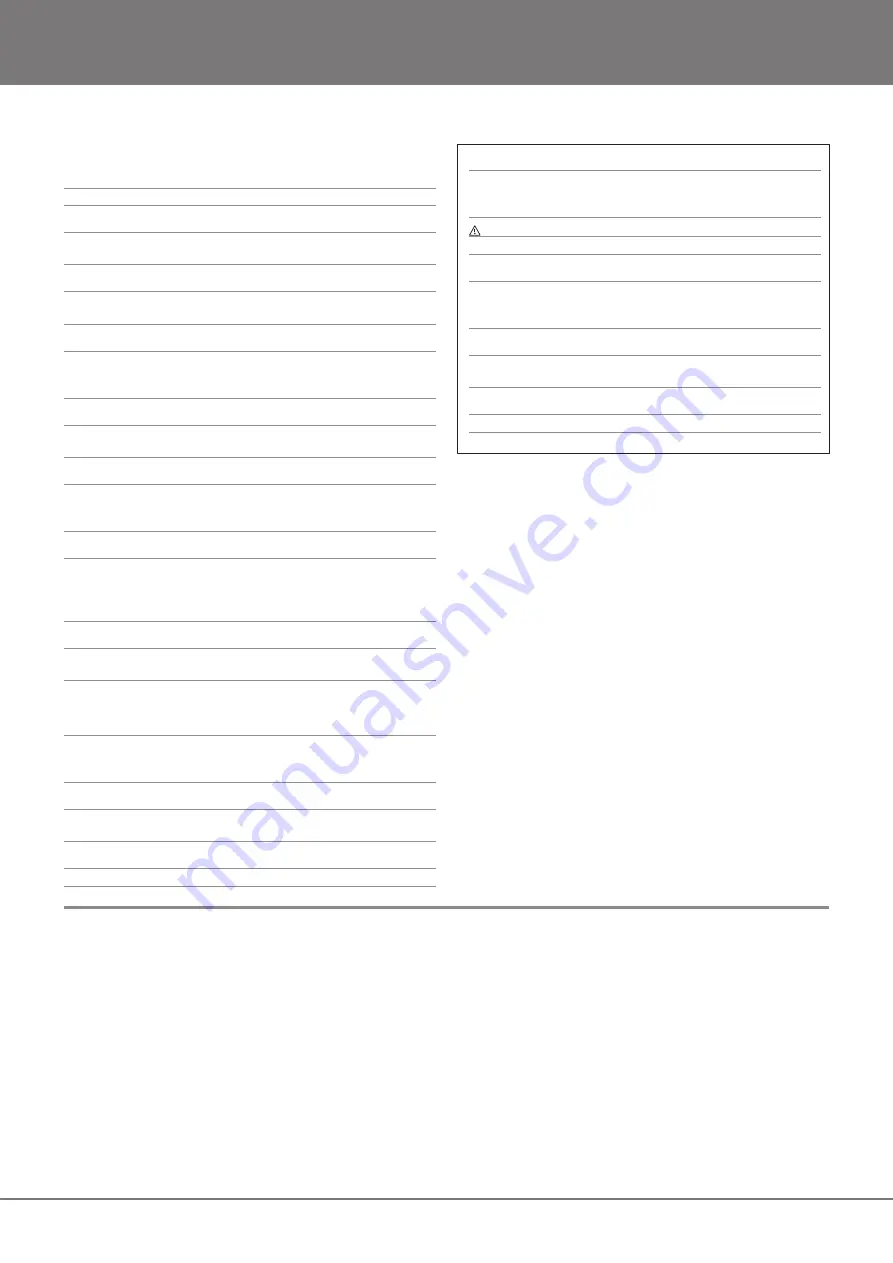
2
© Öhlins Racing AB. All rights reserved.
Any reprinting or unauthorized use without the written
permission of Öhlins Racing AB is prohibited.
General Warnings
Note!
1
When working with the Öhlins product, always read the Vehicle Service Manual.
Note!
1
The shock absorber/front fork/steering damper is an important part of the vehicle
and will affect the stability.
Note!
1
Read and ensure you understand the information in this manual and other
technical documents provided by Öhlins, before using the product.
Note!
1
Öhlins Racing AB can not be held responsible for any damage to the shock
absorber/front fork/steering damper, vehicle, other property or injury to persons, if
the instructions for mounting, usage and maintenance are not followed exactly.
Warning!
⚠
After installing the Öhlins product, take a test ride at low speed to ensure your
vehicle has maintained stability.
Warning!
⚠
If the suspension makes an abnormal noise, or the function is irregular, or if you
notice any leakage from the product, stop the vehicle immediately and return the
product to an Öhlins Service Centre.
Warning!
⚠
The product warranty shall only apply if the product has been operated and
maintained in accordance with recommendations in this manual. If you have any
questions regarding usage, service, inspection and/or maintenance please contact
Öhlins.
Note!
1
Before working on the product make sure that the vehicle is washed and cleaned
properly. Do not use alcobased products on the outside or inside of the product.
Product Specific Warnings
Warning!
⚠
This product was developed and designed exclusively for a specific vehicle model
and shall only be installed on the intended vehicle model in its original condition as
delivered from the vehicle manufacturer.
Warning!
⚠
This product is pressurized. Do not open, service or modify this product without
proper education (authorized Öhlins dealer/distributor) and proper tools.
Caution!
✋
Do not use a pressure washer or a power washer when cleaning the fork.
SAFETY SYMBOLS
In this manual, mounting instructions and other technical documents,
important information concerning safety is distinguished by the following
symbols:
The Safety Alert Symbol means: Warning! Your safety is involved.
Warning!
⚠
The Warning Symbol means: Failure to follow warning instructions can result
in severe or fatal injury to anyone working with, inspecting or using the shock
absorber/front fork, or to bystanders.
Caution!
✋
The Caution Symbol means: Special precautions must be taken to avoid
damage to the shock absorber.
Note!
1
The Note Symbol indicates information that is important regarding procedures.
TABLE OF CONTENTS
Tools ...........................................................................................................................................3
Overview - General layout ..........................................................................................................3
Kit contents .................................................................................................................................4
Remove air spring from lower legs (RXF34/RXF36/RXF36 m.2) ...............................................5
Remove air spring from lower legs (DH38) ................................................................................7
Rebuild of air spring cartridge.....................................................................................................9
Reinstall air spring cartridge (RXF34/RXF36/RXF36 m.2) .......................................................22
Reinstall Air spring cartridge (DH38) ........................................................................................23
Appendix A................................................................................................................................24
SAFETY PRECAUTIONS