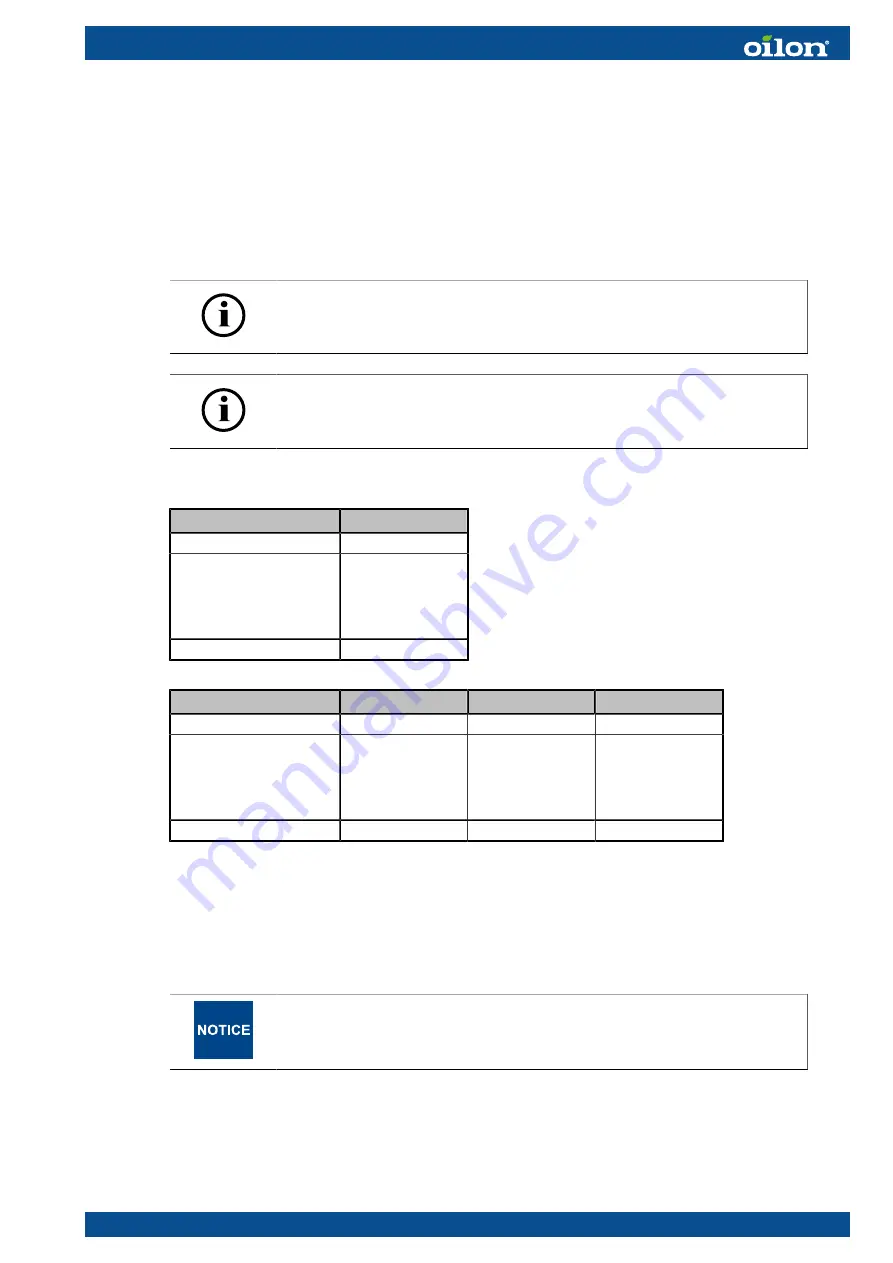
2 Technical data
2.1 Burner technical data
This manual may include additional information about other burner
types. However, the manual is valid only for the burner, mentioned on
the front page and in the burner data table.
Following information applies to standard deliveries.
Burner data
Burner
GP-600 M
Capacity, MMBtu/h
3.7–25.6
Burner motor
3~ 208–600 V 60 Hz
● Output, hp
● Current, A/460 V
● Speed, rpm
20.0
23.5
3,510
Weight, lbs*
1014
Burner
GP-700 M
GP-700 M-II
GP-700 M-III
Capacity, MMBtu/h
4.5–31.8
5.1–36.0
5.7–39.8
Burner motor
3~ 208–600 V 60 Hz
● Output, hp
● Current, A/460 V
● Speed, rpm
25
31
3,510
30
35.8
3,510
+variable
speed drive
40
45
2,970**
Weight, lbs*
1,179
1,246
1,488
*Burner only. The weight varies depending on the content of the delivery.
Turndown ratio, gas 1:6 (100...16.6%)
**The frequency must be converted to 50 Hz.
In 700 M-III burners with a 60-Hz configuration, use 50 Hz instead of
the nominal frequency. Make sure that the motor rpm does not exceed
3000.
M4219 2305EN
11 (111)
Summary of Contents for GP-600 M
Page 2: ......
Page 16: ...Block diagram of contact links Block diagram ver 7 14 111 M4219 2305EN...
Page 87: ...5 5 Time sequence diagram gas use 7550f57e 0515 Gp1 ver 6 M4219 2305EN 85 111...
Page 113: ...M4219 2305EN 111 111...
Page 114: ...112 111 M4219 2305EN...
Page 115: ......