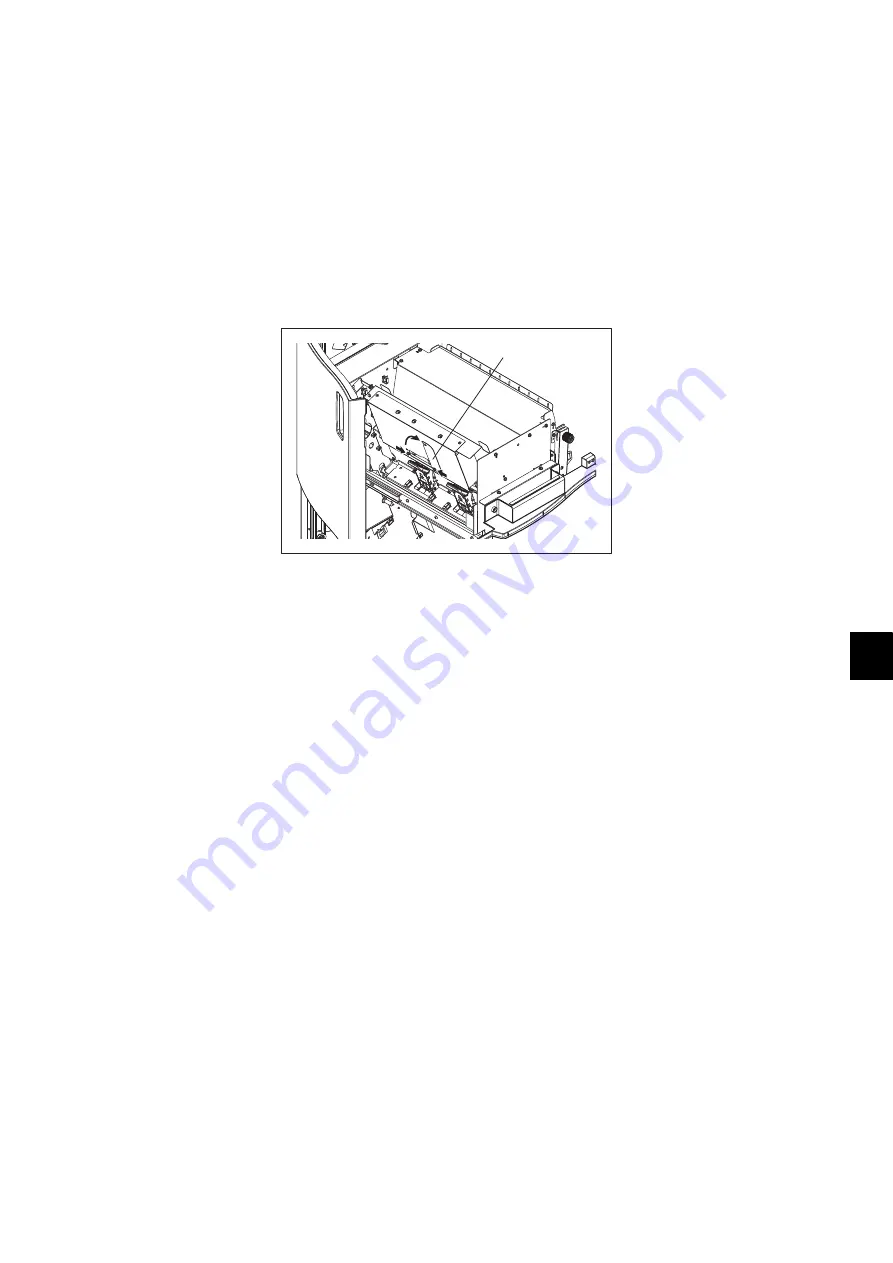
11
© 2012 OKI DATA CORPORATION All rights reserved
ES9160 MFP / ES9170 MFP
FIRMWARE UPDATING
11 - 67
11.5.13 Saddle stitcher firmware (MJ-1106)
[A] Update Procedure
(1)
Install the ROM to the download jig.
Make sure the direction is correct.
(2)
Turn OFF the power of the equipment.
(3)
Open the front upper cover and then pull out the saddle stitch unit.
(4)
Loosen 2 screws and open the saddle control PC board access cover [1].
Fig.11-68
[ 1 ]
Summary of Contents for ES9160
Page 12: ......
Page 24: ...ES9160 MFP ES9170 MFP 2012 OKI DATA CORPORATION All rights reserved FEATURES 1 2...
Page 308: ...ES9160 MFP ES9170 MFP 2012 OKI DATA CORPORATION All rights reserved SELF DIAGNOSIS MODES 5 56...
Page 832: ...ES9160 MFP ES9170 MFP 2012 OKI DATA CORPORATION All rights reserved REMOTE SERVICE 10 38...
Page 920: ...ES9160 MFP ES9170 MFP 2012 OKI DATA CORPORATION All rights reserved BACKUP FUNCTION 12 12...
Page 1086: ......
Page 1087: ......