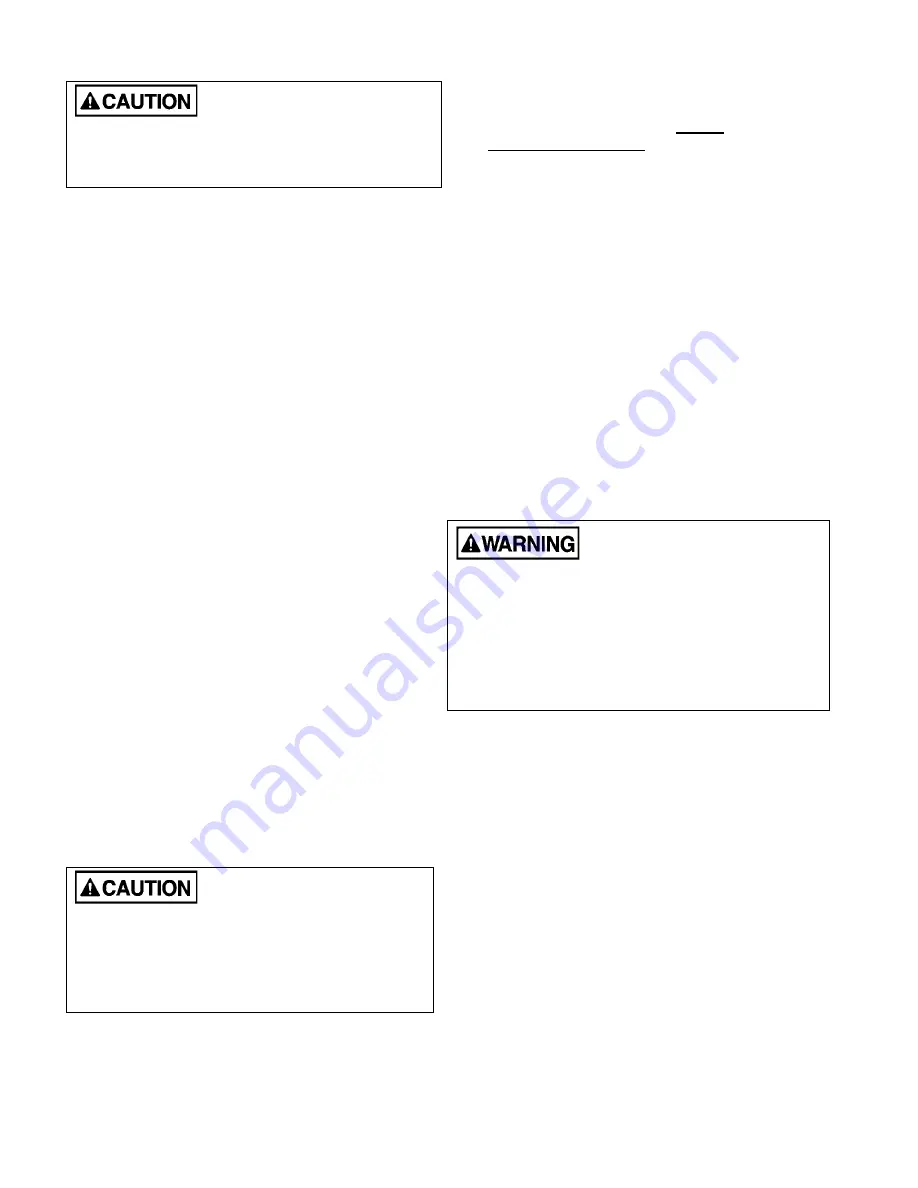
240005126 Rev A 10/27/2005
8
DO NOT START THE BURNER UNLESS THE
BLOWER ACCESS DOOR IS SECURED IN
PLACE.
20. CIRCULATING AIR BLOWER
The HTL furnace may be equipped with either a Direct
Drive blower systems, or a Belt Drive blower system.
Direct Drive
Direct drive blower speed adjustments are not
normally required in properly sized extended plenum
duct systems. The motor RPM and air CFM delivery
will vary automatically to accommodate conditions
within the usual range of external static pressures
typical of residential duct systems. Under-sized duct
systems may require a higher blower speed to obtain a
reasonable system temperature rise. Some older duct
systems were not designed to provide static pressure.
They typically feature special reducing fittings at each
branch run and lack block ends on the trunk ducts.
These systems may require modification to provide
some resistance to the airflow to prevent over-amping
of the direct drive blower motor. Selecting a lower
blower speed may correct this problem. Direct drive
blower speeds are adjusted by changing the "hot"
wires to the motor winding connections. Please refer to
wiring diagrams in Appendix B or the wiring diagram
label affixed to the furnace.
THE NEUTRAL WIRE
(normally the white wire) IS NEVER MOVED TO
ADJUST THE BLOWER SPEED
.
It is possible and acceptable to use a single blower
speed for both heating and cooling modes. The
simplest method to connect the wiring from both
modes is to use a "piggy-back connector"
accommodating both wires on a single motor tap. It is
also acceptable to connect the selected motor speed
with a pigtail joined to both heating and cooling speed
wires with a wire nut. As a safety precaution against
accidental disconnection of the wires by vibration, it is
advisable to secure the wire nut and wires with a few
wraps of electricians tape.
DO NOT CONNECT POWER LEADS
BETWEEN MOTOR SPEEDS. THE NEUTRAL
WIRE MUST ALWAYS BE CONNECTED TO
THE MOTOR'S DESIGNATED NEUTRAL
TERMINAL.
If the joining of the blower speed wiring is done in the
furnace junction box, tape off both ends of the unused
wire.
Do not use the blower speed wires as a source of
power to accessories as electronic air cleaners
and humidifier transformers unless it is certain
that only one motor speed will be used
. The unused
motor taps auto-generate sufficiently high voltages to
damage accessory equipment.
Belt Drive
If the blower is a belt drive type with a pulley and V-belt
system, air delivery and system temperature rise may
be varied by adjusting the variable-speed motor pulley.
The circulating air blower adjustment must be such as
to obtain an air temperature rise specified on the rating
plate.. Loosen the set screw in the pulley outer flange,
close the pulley to increase speed and decrease air
temperature rise; open the pulley to decrease the
speed and increase the air temperature rise. Align the
motor and blower pulley to minimize noise and belt
wear. Check belt tension by flexing belt midway
between the pulleys. Correct belt tension permits
approximately 1" flexing. Too much tension will cause
motor to overload and bearing wear, too little tension
will permit belt slippage. The recommended minimum
return air temperature is 50ºF (10ºC).
DISCONNECT THE POWER SUPPLY TO THE
FURNACE BEFORE OPENING THE BLOWER
ACCESS DOOR TO SERVICE THE AIR FILTER,
FAN AND MOTOR. FAILURE TO SHUT OFF
POWER COULD ALLOW THE BLOWER TO
START UNEXPECTEDLY, CREATING A RISK
OF DEATH OR PERSONAL INJURY.
21. MAINTENANCE AND SERVICE
A: Routine Maintenance By Home Owner
Other than remembering to arrange for the annual
professional servicing of the furnace by the service or
installation contractor, the most important routine
service performed by the homeowner is to maintain the
air filter or filters. A dirty filter can cause the furnace to
over-heat, fail to maintain indoor temperature during
cold weather, increase fuel consumption and cause
component failure.
The furnace filter(s) should be inspected, cleaned or
replaced monthly. The furnace is factory equipped with
a semi-permanent type filter. If the filter is damaged,
replace with filters of the same size and type. (See
Appendix A, Table A-8).
During the routine service, inspect the general
condition of the furnace watching for signs of oil leaks
in the vicinity of the oil burner, soot forming on any
external part of the furnace, soot forming around the
joints in the vent pipe, etc. If any of these conditions