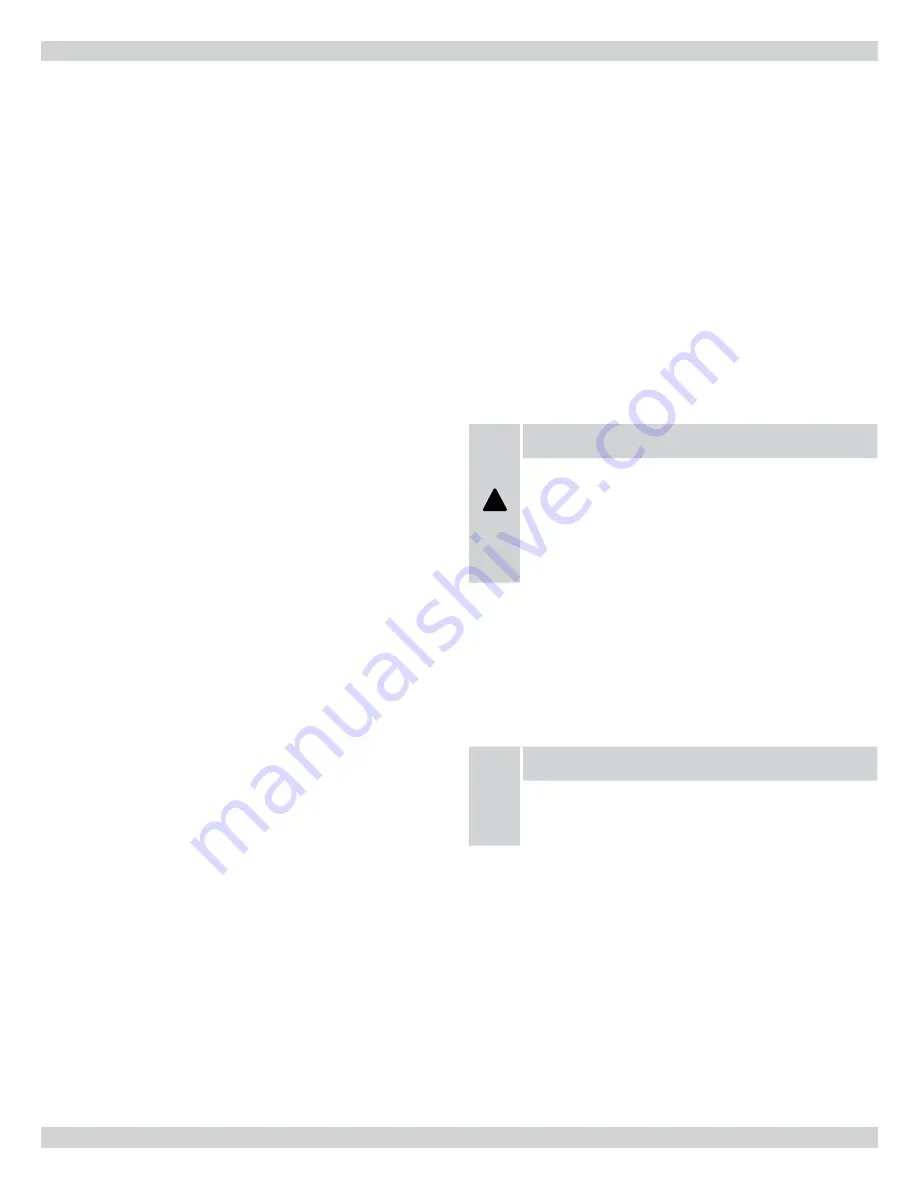
7
OIl buRNeRs
The thermostat should be located approximately 5 feet above the
floor, on an inside wall where there is good natural air circulation,
and where the thermostat will be exposed to average room tempera-
tures. Avoid locations where the thermostat will be exposed to cold
drafts, heat from nearby lamps and appliances, exposure to sunlight,
heat from inside wall stacks, etc.
The thermostat heat anticipator should be adjusted to the amper-
age draw of the heating control circuit as measured at the "R" and
"W" terminals of the thermostat. To reduce the risk of damaging the
heat anticipator, do not measure this current with the thermostat
connected to the circuit. Measure the amperage by connecting an
ammeter between the two wires that will connect to the thermostat
"R" and "W" terminals.
humidifier
A humidifier is an optional accessory available through most heating
supply outlets. Installation should be carried out in accordance with
the humidifier manufacturer's installation instructions. Water or
water droplets from the humidifier should not be allowed to come
into contact with the furnace heat exchanger. Do not use direct drive
motor connections as a source of power for 120 VAC humidifiers
and humidifier transformers.
Piping Installation
The entire fuel system should be installed in accordance with the
requirement of CAN/CSA B-139, and local regulations. Use only ap-
proved fuel oil tanks, piping, fittings and oil filter.
In the United States the installation must be in accordance with
NFPA No. 31 and local codes and authorities.
Install the oil filter as close to the burner as possible. For further
details of the oil supply tank and piping requirements, please refer
to the instructions and illustrations in the oil burner and oil pump
instructions shipped with the furnace.
Oil filter
All fuel systems should include an oil filter between the fuel oil stor-
age tank and the oil burner. When using an oil burner nozzle smaller
than 0.65 U.S. Gallons Per Hour, install an additional 7 to 10 micron
filter as close as possible to the oil burner.
Oil burner Nozzles
The HTL-D and HTLV-D are certified for multiple firing rates, rang-
ing from 89,000 to 140,000 Btu/h. By manipulating the oil burner
nozzle, flame retention head, static plate and temperature rise; the
furnace may be fired at an ideal rate for a wide range of structures.
Refer to Tables 3A, B and C,
page 11 and the furnace rating plate
to determine the proper combinations.
Oil burner Adjustment
The burner air supply is adjusted to maintain the fuel to air ratio
to obtain ideal combustion conditions. A lack of air causes "soft"
and "sooty" flames, resulting in soot build-up throughout the heat
exchanger passages. Excess combustion air causes a bright roaring
fire and high stack temperatures resulting in poor fuel efficiency. The
HTL-D and HTLV-D furnaces operate most efficiently with a No. 1
smoke spot on the Bacharach Scale. This is not necessarily the opti-
mum setting; however, because dust will inevitably build up on the
air moving components of the oil burner assembly. This will result
in decreased air supply with the potential result of soot building up
in the flue gas passageways of the heat exchanger. Soot behaves as an
insulator and impairs good heat transfer. Stack temperature will in-
crease, and the overall efficiency will decrease. As a means of avoid-
ing this problem, it is advisable to adjust the air supply to provide no
more than a trace smoke spot on the Bacharach Scale.
!
CAUTION
BEFORE OPERATING THE FURNACE CHECK BURN-
ER ALIGNMENT WITH COMBUSTION CHAMBER.
THE END CONE OF THE AIR TUBE MUST BE CEN-
TRED TO THE ACCOMMODATING RING PROVIDED
IN THE DESIGN OF THE COMBUSTION CHAMBER.
ADJUST AS NECESSARY.
burner electrodes
Correct positioning of the electrode tips with respect to each other,
to the fuel oil nozzle, and to the rest of the burner is essential for
smooth light ups and proper operation. Refer to the oil burner in-
structions shipped with the furnace for electrode specifications.
NOTICE
Beckett AF Series Burner electrode specifications have
been revised. They should be adjusted to be 5/16” above
the nozzle centerline.
burner Primary (safety) control
The furnace is equipped with a primary combustion control, some-
times referred to as the burner relay or burner protector relay, which
uses a light sensing device (cad cell) located in the burner housing,
to monitor and control combustion. Over time, dust or combus-
tion residuals can build up on the lens of the cad cell impairing its
response to the flame. The cad cell should be checked for cleanliness
and proper alignment if the primary control frequently shuts down
combustion.
Summary of Contents for HTL-90D
Page 18: ...18 Wiring Diagrams Figure 6 Chimney Vent Burner Wiring Diagram HTL D HTLV D...
Page 22: ...22 Oil Primary Control Sequence of Operation...
Page 31: ...31 Homeowner s Reference Table...
Page 33: ...33 PARTS LISTING HIGHBOY MODEL HTL D AND HTLV D Figure 9 Model HTL D and HTLV D...
Page 34: ...34 HTL D HTLV D Oil Fired Warm Air Furnace NOTES...