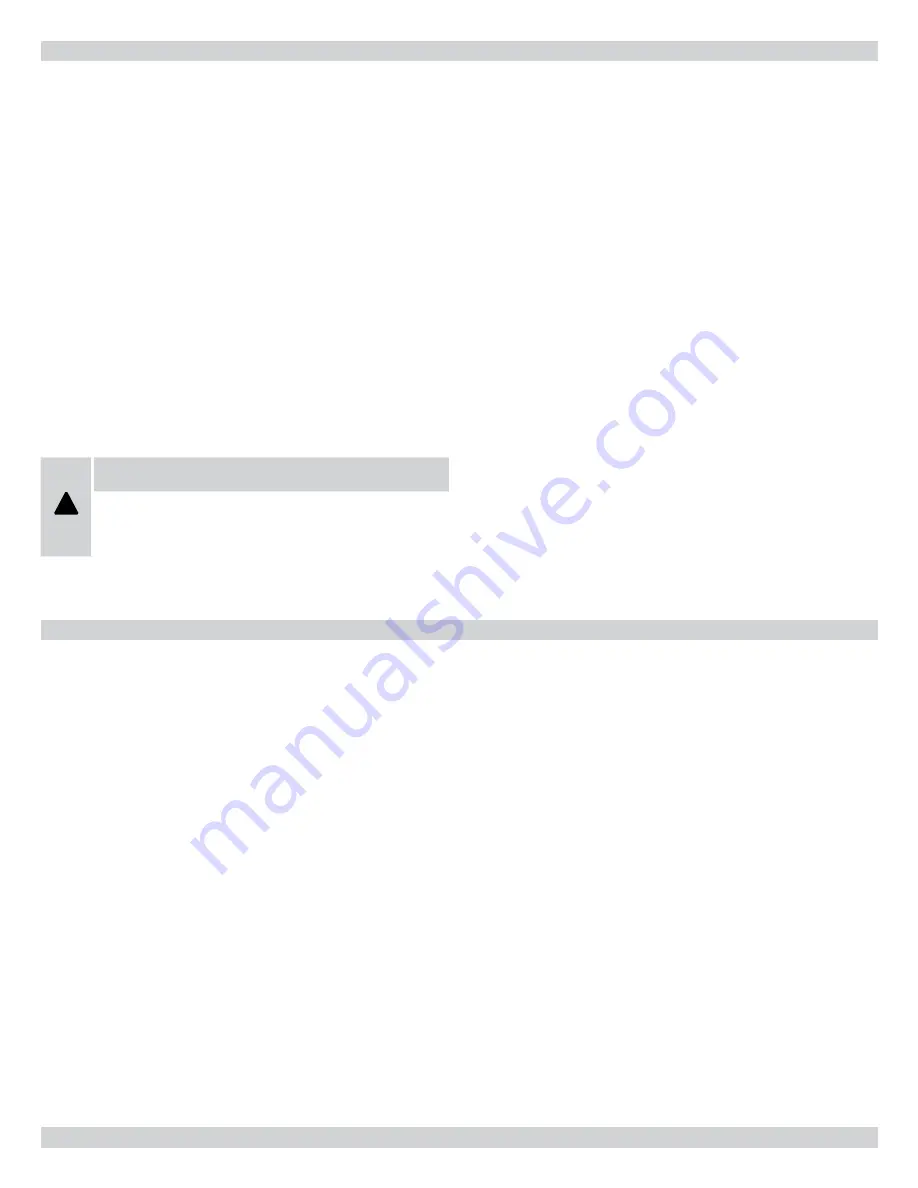
9
MAINTeNANce AND seRVIce
Routine Maintenance by home Owner
Other than remembering to arrange for the annual professional
servicing of the furnace by the service or installation contractor, the
most important routine service performed by the homeowner is to
maintain the air filter or filters. A dirty filter can cause the furnace to
over-heat, fail to maintain indoor temperature during cold weather,
increase fuel consumption and cause component failure.
The furnace filter(s) should be inspected, cleaned or replaced month-
ly. The furnace is factory equipped with a semi-permanent type filter.
If the filter is damaged, replace with filters of the same size and type.
(See Parts Listing Ref. No. 21).
During the routine service, inspect the general condition of the fur-
nace watching for signs of oil leaks in the vicinity of the oil burner,
soot forming on any external part of the furnace, soot forming
around the joints in the vent pipe, etc. If any of these conditions are
present, please advise your service or installation contractor.
Annual service by contractor
!
CAUTION
THE COMBUSTION CHAMBER (FIREPOT) IS FRAG-
ILE. USE CARE WHEN INSPECTING AND CLEANING
THIS AREA.
The heat exchanger should be inspected periodically and cleaned
if necessary. If cleaning is necessary, SHUT OFF POWER TO THE
FURNACE and remove the burner. Using a stiff brush with a wire
handle, brush off scale and soot from inside the drum and flue pipe.
To clean the radiator, remove the clean-out caps screws, and remove
the caps carefully to avoid tearing the gaskets. A wire brush can be
used to loosen dirt and debris on the inside surfaces of the radiator.
Clean out all accumulated dirt, soot and debris with a wire handled
brush and an industrial vacuum cleaner. Before replacing the clean-
out caps, inspect the gaskets. If the gaskets are broken, remove the
remnants and replace with new gaskets.
The blower motor is factory oiled and permanently sealed. DO NOT
LUBRICATE. Excess oil causes premature electric motor failure.
Inspect the blower fan. Clean if necessary.
Oil Burner Maintenance: Follow the instructions of the oil burner
manufacturer. (See oil burner manufacturer's instructions supplied
with furnace or burner). It is advisable to change the oil burner
nozzle and oil filter on an annual basis.
The venting system should be cleaned and inspected for signs of
deterioration. Replace pitted or perforated vent pipe and fittings. The
barometric damper should open and close freely.
All electrical connections should be checked to ensure tight con-
nections. Safety controls such as the high limit controls should be
tested for functionality. The fan control should be checked to ensure
that the fan on and off delay function continues to start and stop the
blower fan at the optimal settings.
before lighting
Open all supply and return air registers and grilles.
Open all valves in oil pipes.
Turn on electric power supply.
To light unit
Set the thermostat above room temperature to call for heat. The
burner should start. NOTE: It may be necessary to press the RESET
button on the primary combustion control relay.
There will be a fan on time delay before the circulating fan is ener-
gized. The United Technologies 1158-120 has an adjustable fan on
time that is set by selecting the dipswitch combination displayed in
Table 2
on page 6
.
This fan on delay can be set at 30, 60, 90 or 120
seconds. Set the thermostat below room temperature. The oil burner
should stop.
The air circulation blower will continue to run until the time off
setting selected on the electronic fan timer control times out. The
United Technologies 1158-120 has an adjustable fan off time of 1, 2,
4,or 6 minutes.
The necessary adjustments to the fan control settings should be
determined by measuring the temperature of the air in the supply
air take-off, or within the first few inches of the supply air trunk. The
OPeRATINg INsTRucTIONs (hTl-D)
side mid point of the transition is usually ideal, providing that the
thermometer probe is beyond the "line of sight" wherein false read-
ings from radiant heat could be observed. System temperature rise is
the difference in temperature between the supply air and return air.
To check the operation of the limit switch, shut off power to the
furnace. Temporarily remove the neutral wire from the direct drive
blower motor. Restore the electrical power to the furnace and set the
thermostat above room temperature.
After three or four minutes of burner operation, the limit control
should turn the burner off. When the limit function test is complete,
shut off electrical power to the furnace, replace the neutral wire to
the blower fan motor, and then restore power. The blower fan will
start up immediately. Once the temperature has dropped and the
limit control has reset, the fan will operate until the fan off time is
achieved. The oil burner will then resume operation and continue
until the thermostat is satisfied. Restore the thermostat setting to a
comfortable temperature.
To shut Down unit
Set the thermostat to the lowest possible setting.
Set the manual switch (if installed) in the Electrical Power Supply
Line to "OFF".
Summary of Contents for HTL-90D
Page 18: ...18 Wiring Diagrams Figure 6 Chimney Vent Burner Wiring Diagram HTL D HTLV D...
Page 22: ...22 Oil Primary Control Sequence of Operation...
Page 31: ...31 Homeowner s Reference Table...
Page 33: ...33 PARTS LISTING HIGHBOY MODEL HTL D AND HTLV D Figure 9 Model HTL D and HTLV D...
Page 34: ...34 HTL D HTLV D Oil Fired Warm Air Furnace NOTES...