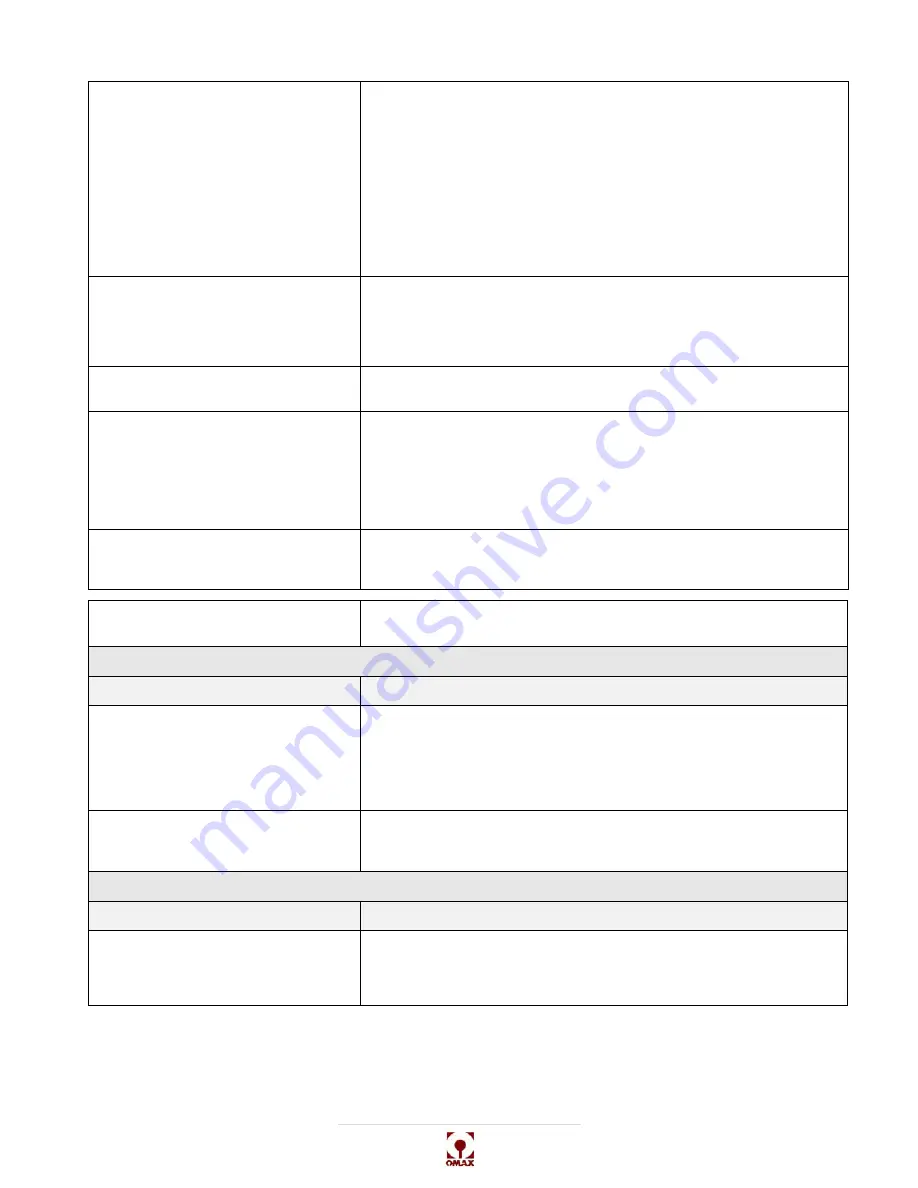
Maintenance
OMAX JetMachining® Center Operator’s Guide
400433D-EN
4 - 49
An abrasive other than the
recommended garnet is being used.
Many abrasives do not cut as well as garnet, and the machinability
should be reduced when using these abrasives. It may be necessary to
experiment to determine the best settings.
Garnet is recommended because it allows a good cutting rate with
relatively low mixing tube wear. Garnet is also nonhazardous and, as
such, is easily disposed. Other abrasives may increase mixing tube
wear and may be a disposal hazard.
WARNING!
Never use silica sand as a cutting abrasive. Fine
silica dust produced by the cutting process can
lead to silicosis, a serious lung disease.
The mixing tube is excessively worn
and unable to form a perfect jet
stream
Mixing tube wear occurs first at the inlet, then a conical wear zone
grows toward the exit end of the mixing tube. Check the tube bore at
both ends using a drill or gage pin. When the outlet has increased in
size by 0.005" (0.13 mm), the mixing tube is near the end of its useful
life for precise cutting.
The jewel that forms the jet is chipped,
dirty, or out-of-tolerance.
Replace the jewel and the jewel holder.
The abrasive flow is stopped or has
been reduced by the presence of dirt
or wet abrasive.
Disassemble the plugged items, blowing them clean and dry with an air
hose.
WARNING!
Never point the air stream at anyone during the
cleaning process. Always wear eye protection!
Poor fixturing of the cutting material.
Improperly secured material will vibrate, causing a rough edge on the
cut part. Never fixture directly to slats. They can move during cutting.
Specify a low cut quality such as 1 or 2.
The pump is not delivering the
pressure specified.
Measure the pressure to see if it is below specification.
Follow the pump troubleshooting procedures.
Holes are Too Large and Parts Undersized
Condition and Possible Causes
Corrective Action
The tool offset is set incorrectly.
If not enough material is being removed (hole too small or part too
large), decrease the tool offset by half the dimensional error observed.
If too much material is being removed, increase the offset by half the
dimensional error. By measuring parts as they are finished, you can
monitor the wear of the mixing tube and periodically reset the tool
offset to achieve more precise cutting.
Tool offset is on the wrong side of the
path.
Switch the lead-in and lead-out and then use the
Generate Tool Path
command in Layout to recreate the part.
You can check your tool offset using
Preview
in Make.
Excessive Taper on Part Edges
Condition and Possible Causes
Corrective Action
The cut was made with the quality
value set too low.
A quality of 1 will just barely pierce the material and usually has
significant taper. Both taper and surface finish should improve as the
quality value is raised (taking longer to make the part). Remember that
different qualities can be set on different portions of the same part.
Summary of Contents for JetMachining Center 2626
Page 8: ...OMAX JetMachining Center Operator s Guide viii 400433D EN ...
Page 12: ...OMAX JetMachining Center Operator s Guide xii 400433D EN ...
Page 22: ...OMAX JetMachining Center Operator s Guide Safety First 1 10 400433D EN ...
Page 140: ...OMAX JetMachining Center Operator s Guide OMAX Glossary 6 16 400433D EN ...
Page 144: ...OMAX JetMachining Center Operator s Guide Index 4 400433D EN ...