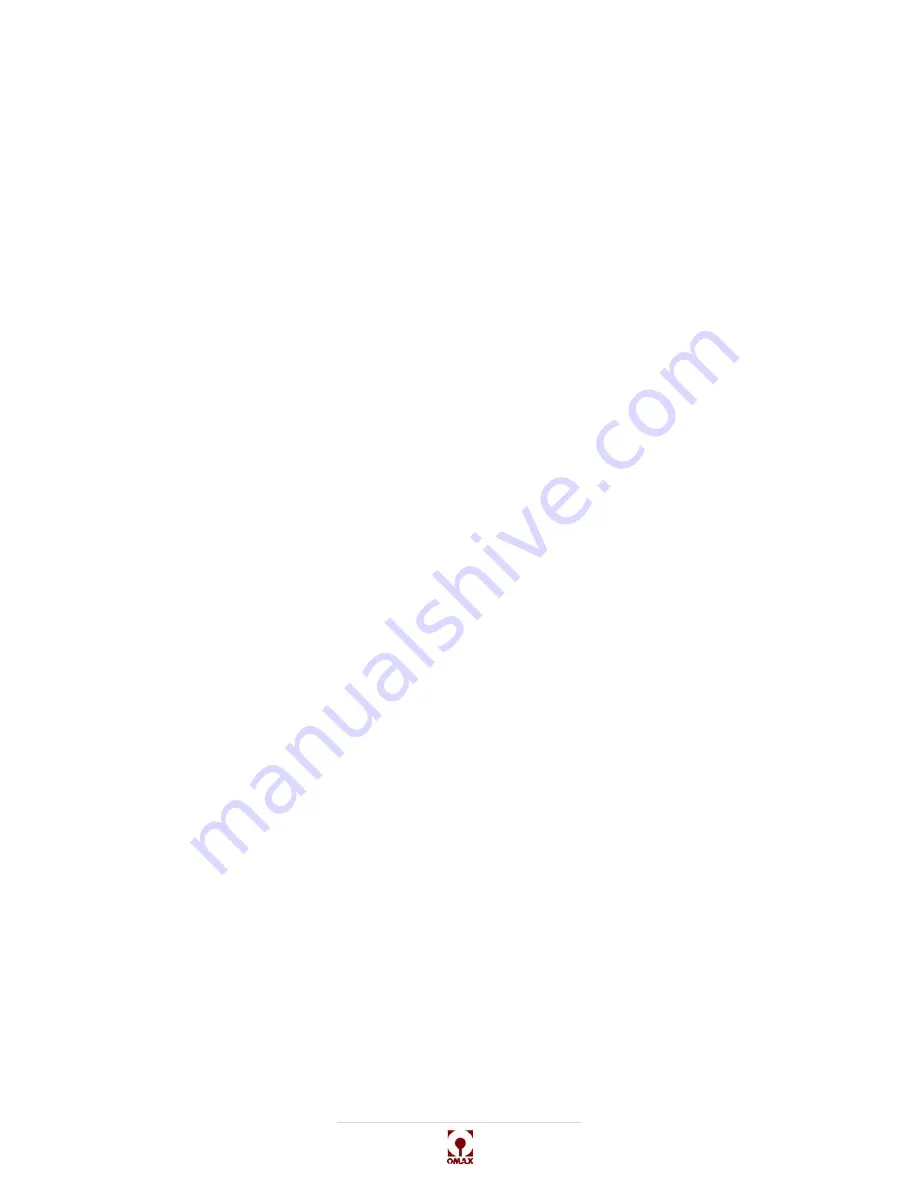
OMAX JetMachining® Center Operator’s Guide
Maintenance
4 - 20
400433D-EN
Nozzle Tests
Once the nozzle has been installed, run the standard nozzle tests provided in OMAX’s Make software to
verify the water seal of the assembly fittings and the jet stream quality:
1.
Set the tip of the
mixing tube
no higher than 1.5" above the water level to prevent the jet stream
from piercing too far down into the tank.
WARNING!
Eye protection must be worn at all times when operating the OMAX JetMachining Center.
Always wear ear protection when operating the abrasivejet nozzle out of water. An out-of-
water abrasivejet can produce noise in excess of 120 decibels.
2.
First, test
nozzle
operation with
Water
only at
Low
pressure and then follow by testing with
Water
and Abrasive
at
High
pressure. Refer to Figure 4-18 for an illustration of the pump and nozzle
test screen.
3.
When running these
pressure tests
, inspect for water leaking from the
high-pressure fittings
and inspect the jet stream to ensure it remains straight and focused. Refer to Figure 3-13,
“Example of Both Good and Poor Quality Jet Streams“ on page 3-15. The jet stream should be
narrow and well-formed near the nozzle. A certain amount of spreading is to be expected at
approximately 1.5 to 2.0 inches (3.8 to 5.1 cm) down the jet stream. A bad jet stream will be wide
and poorly formed and flares almost immediately upon leaving the nozzle. Refer to Figure 3-13 on
page 3-15.
Caution:
Always repair all problems noted during nozzle testing prior to operating the equipment.
Maximizing Nozzle Life
There are a number of simple things you can do to maximize the life of your nozzle components:
• Don't change the Mixing Tube simply because the jet stream looks wide.
• Cut test parts and do kerf checks on a regular basis to see when cutting performance begins to
degrade.
• If the surface quality and accuracy are as expected, continue using the Nozzle Assembly.
• If the quality of the cut part is not as expected, prompt correction of the problem minimizes
complications.
• Take advantage of features in the OMAX Make software that allow the using of different offset values
and mixing tube diameters to adjust for Mixing Tube wear.
• Maintain part tolerances and extend Mixing Tube use by entering the correct offset value in Make.
All nozzle components are negatively affected by contamination, dirt, or other materials present in high-
pressure systems. In general, cleanliness is a key controllable factor in extending the life of nozzle
components. Some simple but effective ways to maintain cleanliness include:
• Keep your work area clean.
• Store spare nozzle components and other parts in sealed, clean containers or bags until ready for
use.
• Thoroughly clean all parts and high-pressure fittings prior to assembly or reassembly.
• Use an ultrasonic cleaner with white vinegar to remove mineral build-up in the orifice assembly.
• Prevent garnet contamination:
-
Don’t store garnet in open bags or buckets – store in closed containers.
-
Use a sharp blade to open abrasive bags.
-
Always keep the top of the abrasive hopper covered to prevent water from entering.
Some best practices pertaining to parts and components will also lead to extended nozzle life:
• Do not use damaged parts. Visually inspect parts and all orifices prior to use.
• Always use pump manifold and last chance nozzle filters. Inspect and replace them on a regular
basis.
Summary of Contents for JetMachining Center 2626
Page 8: ...OMAX JetMachining Center Operator s Guide viii 400433D EN ...
Page 12: ...OMAX JetMachining Center Operator s Guide xii 400433D EN ...
Page 22: ...OMAX JetMachining Center Operator s Guide Safety First 1 10 400433D EN ...
Page 140: ...OMAX JetMachining Center Operator s Guide OMAX Glossary 6 16 400433D EN ...
Page 144: ...OMAX JetMachining Center Operator s Guide Index 4 400433D EN ...