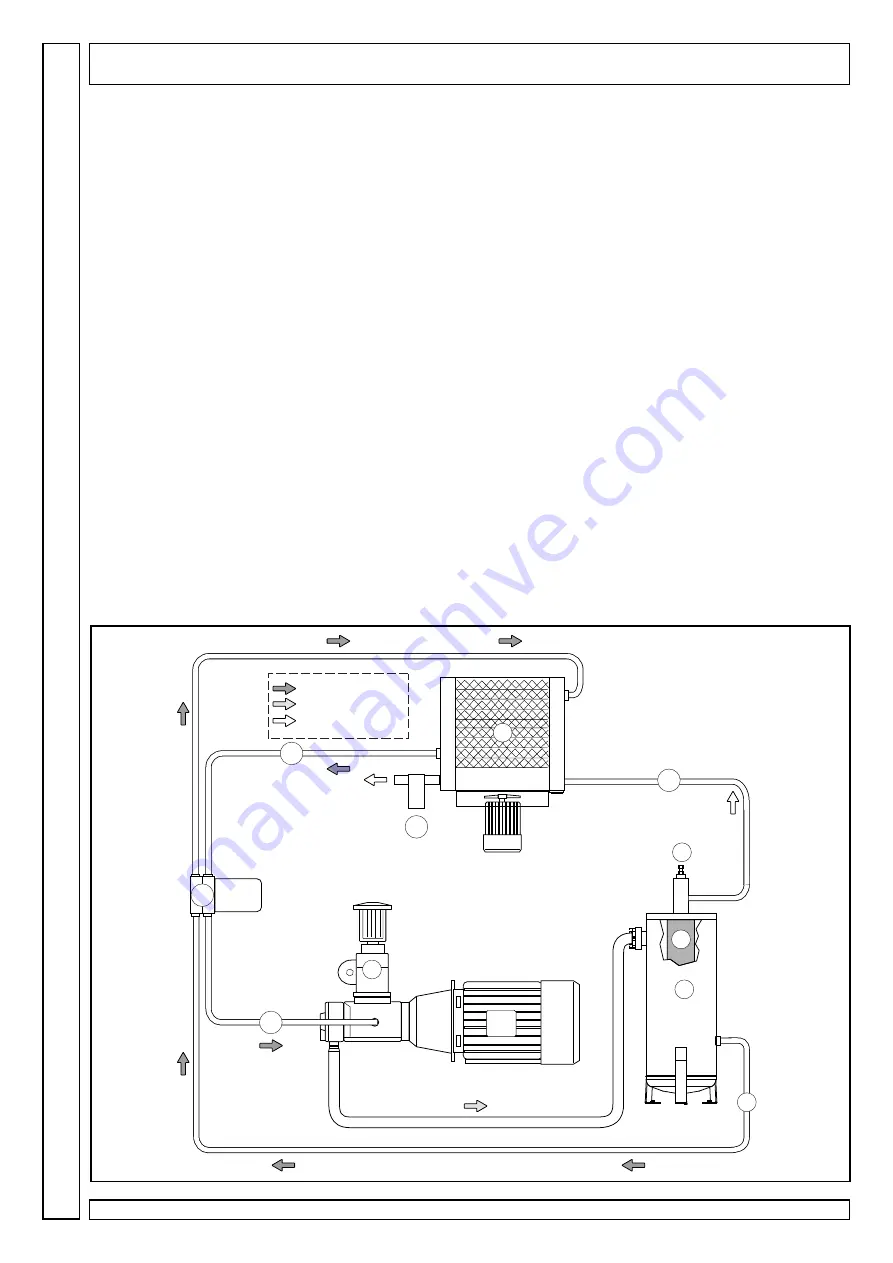
14
14
2
8
olio / oil
aria+olio / air+oil
aria / air
6
5
4
9
3
11
7
9
10
EN
START-UP AND OPERATION
WORKING CYCLE
• At the end of the start-up cycle, the electric motor reaches the maximum working speed; for pressure under approx. 4 bar, the
compressed air produced accumulates inside the tank (4), not being able to cross the minimum pressure valve, whose opening
is calibrated to approx. 4 bar.
• As soon as the line pressure reaches a value equal to the target pressure (see “vacuum pressure” in the User menu on page 19)
reduced by 0.5 bar, the inverter (item 16) starts to change the rotation speed of the electric motor, for the purpose of maintaining
the selected line pressure constant, despite the air flow rate required by the user undergoing variations.
• The compressed air inside the tank (4) forces the oil to flow through the tubing (7) towards the oil filter/thermostatic valve (10).
If the oil temperature is lower than the temperature calibration of the thermostatic element, the oil returns to the screw through
the hoses (9). If the oil temperature is higher than the temperature calibration of the thermostatic element, the oil is flowing in
the radiator (8) where it is cooled.
• Subsequently, the oil passing through the pipe (9) reaches the compressor, mixing with the suction air and thereby creating
an air/oil mixture which ensures sealing and lubrication of the moving organs of the compressor.
• The air/oil mixture goes back to tank (4), where air and oil are first separated by centrifugation and then by the oil separator
filter (6).
• Downstream of the oil separator filter only air exits, which through the tubing (3) reaches the air radiator (8) passing through
the condensate separator and going to the mains.
• The condensate recovered in the condensate separator (11) is automatically released by the timed solenoid valve.
• Min. pressure valve (5) serves also as a check valve.
• Compressor delivers compressed air to outer air tank.
• Having reached the minimum rotation value of the motor, the pressure sensor sends a signal that starts the running on no load
timer and disconnects current to the solenoid valve (1) of the regulator (2).
• Regulator (2) closes and compressor stops compressing and starts idling.
• The timer continues the count until the value set is reached, and on reaching it if there were no pressure variations, commands
stoppage of the electric motor.
• If the pressure goes under the minimum value set on the controller before the timer has terminated the count, the solenoid
valve receives current and opens.
• Regulator (2) opens and compressor operates under normal load; timer is reset.
• This cycle is automatically repeated.
STORM 38 VS - Cod.197DD9910 - Rev.2 01/2016
NOBEL DV 45-55_NOBEL 75 E DV CSA - Cod.197EE0696ML - Rev.0 02/2020